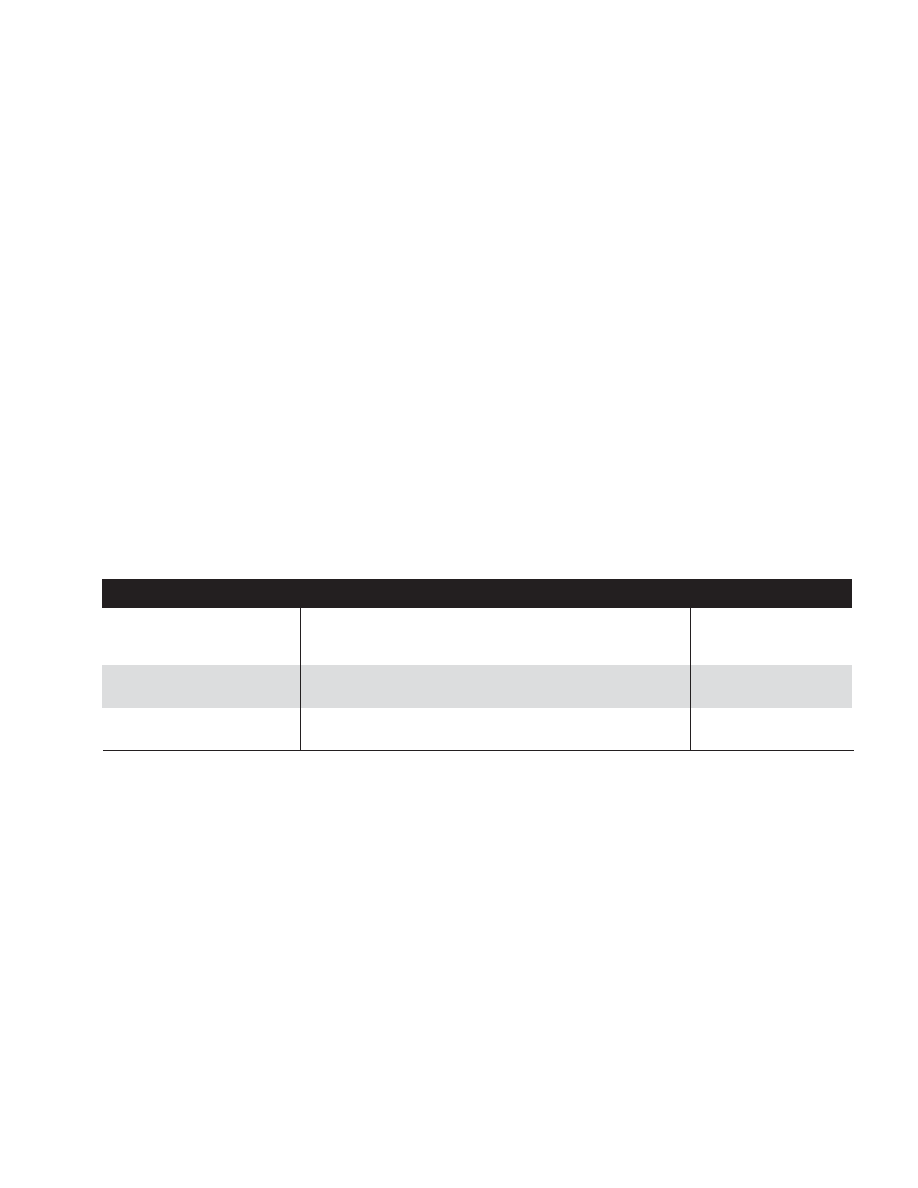
3M
Thermally Conductive Adhesive Transfer Tapes
9882
9885 9890
Application Guidelines
1.) Substrate surfaces should be clean and dry prior to tape application. Isopropyl alcohol (isopropanol) applied with a lint-
free wipe or swab should be adequate for removing surface contamination such as dust or finger prints. Do not use
“denatured alcohol” or glass cleaners, which often contain oily components. Allow the surface to dry for several
minutes before applying the tape. More aggressive solvents (such as acetone, methyl ethyl ketone [MEK] or toluene)
may be required to remove heavier contamination (grease, machine oils, solder flux, etc.) but should be followed by a
final isopropanol wipe as described above.
Note: Be sure to read and follow the manufacturers’ precautions and directions when using primers and solvents.
2.) Apply the tape to one substrate at a modest angle with the use of a squeegee, rubber roller or finger pressure to help
reduce the potential for air entrapment under the tape during its application. The liner can be removed after positioning
the tape onto the first substrate.
3) Assemble the part by applying compression to the substrates to ensure a good wetting of the substrate surfaces with the
tape. Proper application of pressure (amount of pressure, time applied, temperature applied) will depend upon design of
the parts. Rigid substrates are more difficult to bond without air entrapment as most rigid parts are not flat. Use of a
thicker tape may result in increased wetting of rigid substrates. Flexible substrates can be bonded to rigid or flexible
parts with much less concern about air entrapment because one of the flexible substrate can conform to the other
substrates.
4.) Application pressure guideline table for 3M Thermally Conductive Adhesive Transfer Tapes 9882, 9885, and 9890.
Substrate
Application Conditions
Time
Rigid to rigid
Minimum: 15 psi at room temperature
2 sec
Preferred: 50 psi at room temperature
5 sec
More pressure equals better wetting
Flexible to rigid
Minimum: 5 psi at room temperature
1 sec
Preferred: 15 psi at room temperature
5 sec
Flexible to flexible
Minimum: 5 psi at room temperature
1 sec
Preferred: 15 psi at room temperature
5 sec
5.) Application Tips:
For rigid to rigid bonding, a twisting motion during assembly of the substrates will improve wetting. This should be a
back and forth twisting motion during the application of compression.
For flexible to rigid or flexible to flexible bonding, a roll lamination system may be employed to apply the flexible
substrate down to the rigid (or other flexible) substrate. Rubber nip rollers, heated steel rollers, and other methods can be
employed to bond in a continuous manner.
Heat can be employed to increase wetting percentage and wetting rate of the substrates and to build room temperature
bond strength.
Primers may be employed to increase adhesion to low surface energy substrates (eg. plastic packages). Contact your
3M representative for more information about primers.
For best product performance, it is important to use pressure and time conditions to achieve as much wetting as possible.
(3)