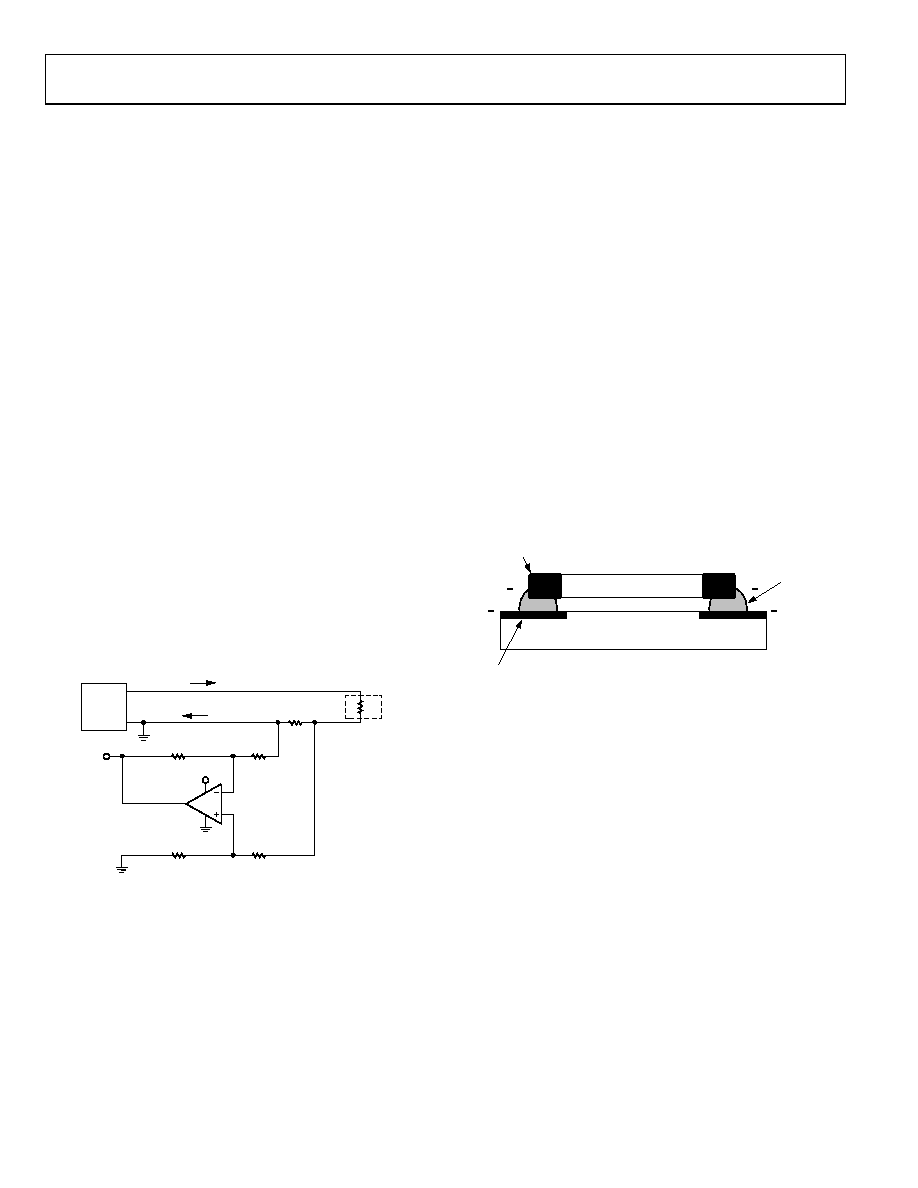
ADA4638-1
Data Sheet
Rev. 0 | Page 20 of 24
PRECISION LOW-SIDE CURRENT SHUNT SENSOR
Many applications require the sensing of signals near the
positive or negative rails. Current shunt sensors are one such
application and are mostly used for feedback control systems.
They are also used in a variety of other applications, including
power metering, battery fuel gauging and feedback controls in
electrical power steering. In such application, it is desirable to
use a shunt with very low resistance to minimize series voltage
drop. This not only minimizes wasted power, but also allows the
measurement of high currents while saving power. A typical
shunt may be 100 mΩ. At a measured current of 1 A, the
voltage produced from the shunt is 100 mV, and the amplifier
error sources are not critical. However, at low measured current
in the 1 mA range, the 100 μV generated across the shunt
demands a very low offset voltage and drift amplifier to
maintain absolute accuracy. The unique attributes of a zero-
drift amplifier provides a solution. The
ADA4638-1, with its
input common-mode voltage that includes the lower supply rail,
can be used for implementing low-side current shunt sensors.
Figure 67 shows a low-side current sensing circuit using the
amplifier with a gain of 1000. Although the
ADA4638-1 has
high common-mode rejection, the CMR of the system is limited
by the external resistors. Therefore, the key to high CMR for the
system are resistors that are well matched from both the
resistive ratio and relative drift, where R1/R2 = R3/R4. The
resistors are important in determining the performance over
manufacturing tolerances, time, and temperature.
R2
100k
VSY
VOUT*
*VOUT = AMPLIFIER GAIN × VOLTAGE ACROSS RS
= 1000 × RS × I
= 100 × I
RL
RS
0.1
R1
100
I
ADA4638-1
R4
100k
R3
100
100
72
-16
7
I
Figure 67. Low-Side Current Sensing Circuit
PRINTED CIRCUIT BOARD LAYOUT
The
ADA4638-1 is a high precision device with ultralow offset
voltage and offset voltage drift. Therefore, care must be taken in
the design of the printed circuit board (PCB) layout to achieve
optimum performance of the
ADA4638-1 at board level.
To avoid leakage currents, keep the surface of the board clean
and free of moisture. Coating the board surface creates a barrier
to moisture accumulation and reduces parasitic resistance on
the board.
Properly bypassing the power supplies and keeping the supply
traces short minimizes power supply disturbances caused by
output current variation. Connect bypass capacitors as close as
possible to the device supply pins. Stray capacitances are a
concern at the outputs and the inputs of the amplifier. It is
recommended that signal traces be kept at a distance of at least
5 mm from supply lines to minimize coupling.
A potential source of offset error is the Seebeck voltage on the
circuit board. The Seebeck voltage occurs at the junction of two
dissimilar metals and is a function of the temperature of the
junction. The most common metallic junctions on a circuit
board are solder-to-board trace and solder-to-component lead.
Figure 68 shows a cross section of a surface-mount component
soldered to a PCB. A variation in temperature across the board
(where TA1 ≠ TA2) causes a mismatch in the Seebeck voltages at
the solder joints thereby resulting in thermal voltage errors that
degrade the performance of the ultralow offset voltage of the
SOLDER
+
COMPONENT
LEAD
COPPER
TRACE
VSC1
VTS1
TA1
SURFACE-MOUNT
COMPONENT
PC BOARD
TA2
VSC2
VTS2
IF TA1 ≠ TA2, THEN
VTS1 + VSC1 ≠ VTS2 + VSC2
100
72-
06
7
Figure 68. Mismatch in Seebeck Voltages Causes Seebeck Voltage Error
To minimize these thermocouple effects, orient resistors so that
heat sources warm both ends equally. Where possible, the input
signal paths should contain matching numbers and types of
components to match the number and type of thermocouple
junctions. For example, dummy components, such as zero value
resistors, can be used to match the thermoelectric error source
(real resistors in the opposite input path). Place matching compo-
nents in close proximity and orient them in the same manner to
ensure equal Seebeck voltages, thus cancelling thermal errors.
Additionally, use leads that are of equal length to keep thermal
conduction in equilibrium. Keep heat sources on the PCB as far
away from amplifier input circuitry as is practical.
It is highly recommended to use a ground plane. A ground plane
helps distribute heat throughout the board, maintains a constant
temperature across the board, and reduces EMI noise pickup.