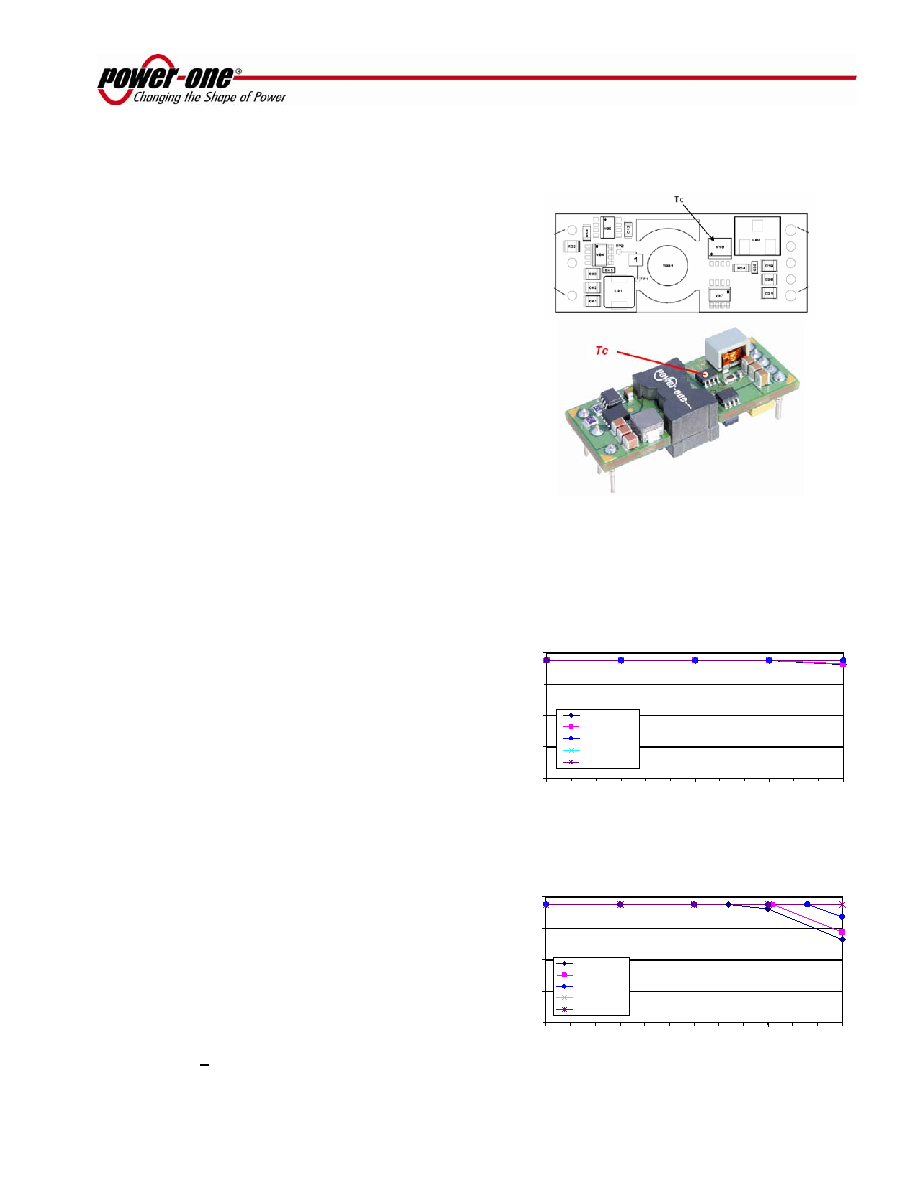
MCD10112 Rev. 1.1, 27-Jan-10
Page 13 of 17
www.power-one.com
EMS Series, DC-DC Converter Data Sheet
Wide-Range Input; 3.3 & 5.0 VDC @ 50W Output
Notes:
1.
When the output voltage is trimmed up, the output power
from the converter must not exceed its maximum rating. The
power is determined by measuring the output voltage on the
output pins, and multiplying it by the output current.
2.
In order to avoid creating apparent load regulation
degradation, it is important that the trim resistors be
connected directly to the remote sense pins, and not to the
load or to traces going to the load.
3.
The output voltage increase can be accomplished either by
the trim or by the remote sense or by the combination of
both. In any case, the absolute maximum output voltage
increase shall not exceed the limits defined in the Features
Specification
section above.
4.
Either Rup or Rdown should be used to adjust the output
voltage according to the equations above. If both Rup and
Rdown are used simultaneously, they will form a resistive
divider and the equations above will not apply.
Thermal Considerations
EMS converters are designed for both natural and forced
convection cooling. To achieve long term reliability, the
recommended power derating curves below, were
established by comparing measured junction and hot spot
temperatures against those allowed per Power-One’s
component derating guidelines
The graphs in Figures 27 through 29 and 30 through 32
show the maximum recommended output current of each
EMS converter at various ambient temperatures under
both natural and forced-convection cooling (longitudinal
airflow direction, from pin 1 to pin 3). Ratings at input
voltages of 24, 36, and 48 VDC are provided.
Thermal Measurements
Measurements requiring airflow were made in Power-
One’s vertical wind tunnel equipment using both Infrared
(IR) thermography as well as the traditional thermocouple
method. The converter was soldered to a test board
consisting of a 0.060” thick printed wiring board (PWB)
with four layers. The top and bottom layers were not
metalized. The two inner layers, comprised of two-ounce
copper, were used to provide traces for connectivity to the
converter. The lack of metalization on the outer layers as
well as the limited thermal connection ensured that heat
transfer from the converter to the PWB was minimized.
This provides a worst-case but consistent scenario for
thermal derating purposes.
With the converter installed into the host application,
customer verification that all components are at or below
their safe operating temperatures may be performed
similarly. However, for a more simplified testing method,
monitoring the converter’s designated thermal reference
point (TC) will yield effective results.
The
recommended
location
of
the
measuring
thermocouple is shown below. This reference point should
be maintained at < 100
OC.
It is recommended to use a 32AWG to 40AWG
thermocouple wire probe on the location identified below;
labeled
TC
Figure 26. EMS Thermal Reference Point, TC.
Power Derating f (VIN, TA, Airflow)
Direction of airflow: from –VIN (Pin 1) to +VIN (Pin 3)
0
4
8
12
16
25
40
55
70
85
Ambient Temperature (Deg C)
Load
C
ur
rent
(
A
)
NC (25 - 35 LFM)
100 LFM
200 LFM
300 LFM
400 LFM
Figure 27. EMS15DE, Vin = 24 VDC
0
4
8
12
16
25
40
55
70
85
Ambient Temperature (Deg C)
Lo
ad
C
ur
rent
(
A
)
NC (25 - 35 LFM)
100 LFM
200 LFM
300 LFM
400 LFM
Figure 28. EMS15DE, Vin = 36 VDC