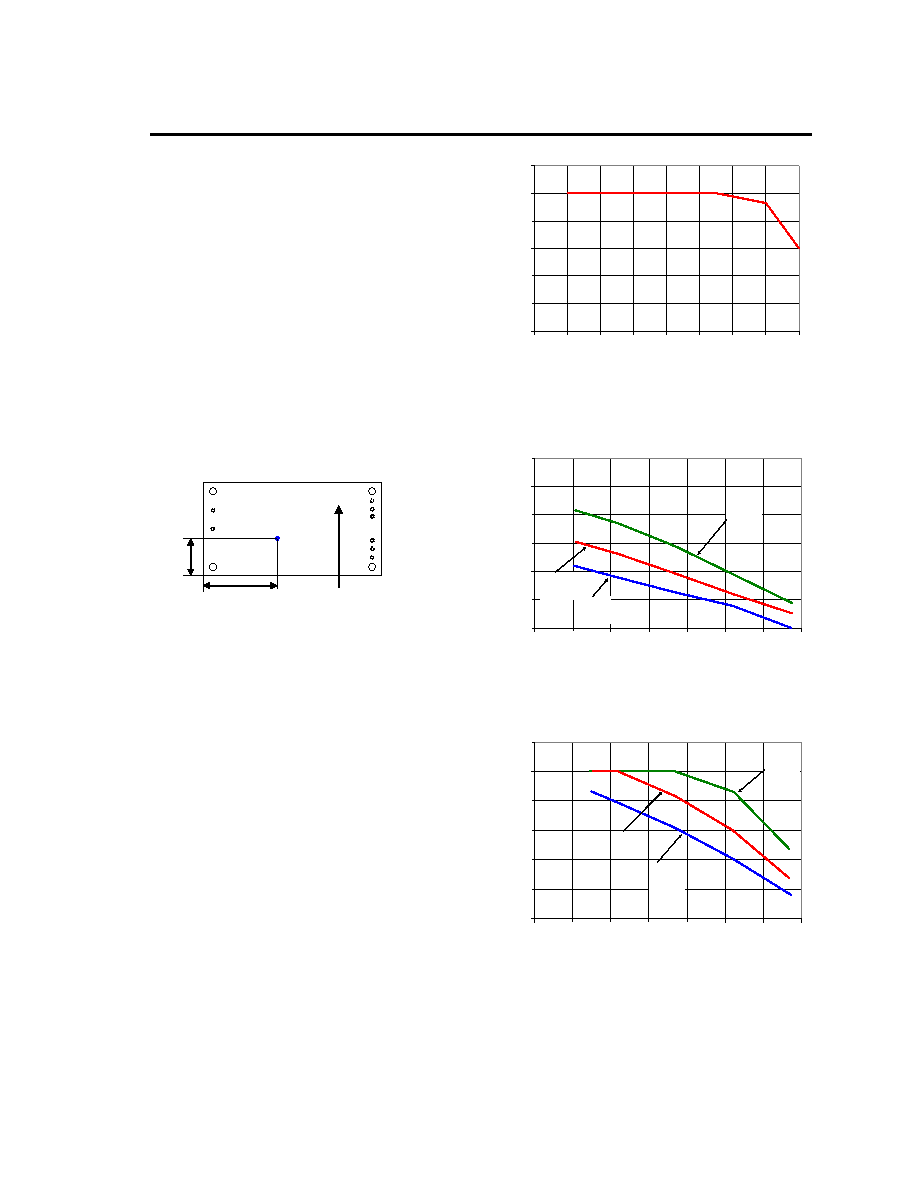
Data Sheet
October 5, 2009
FNW700R Power Modules; DC-DC Converters
36 – 75 Vdc Input; 28Vdc Output; 700W Output
LINEAGE POWER
10
Thermal Considerations
The power modules operate in a variety of thermal
environments; however, sufficient cooling should be
provided to help ensure reliable operation of the unit.
Heat-dissipating components inside the unit are
thermally coupled to the case. Heat is removed by
conduction, convection, and radiation to the
surrounding environment. Proper cooling can be
verified by measuring the case temperature. Peak
temperature (TC) occurs at the position indicated in
Figure 14.
Considerations include ambient temperature, airflow,
module power dissipation, and the need for increased
reliability. A reduction in the operating temperature of
the module will result in an increase in reliability. The
thermal data presented here is based on physical
measurements taken in a wind tunnel.
For reliable operation this temperature should not
exceed 100C.
Figure 14. Case (Tc ) Temperature Measurement
Location (top view).
The output power of the module should not exceed the
rated power for the module as listed in the ordering
Information table.
Although the maximum TC temperature of the power
modules is 100 °C, you can limit this temperature to a
lower value for extremely high reliability.
Please refer to the Application Note “Thermal
Characterization Process For Open-Frame Board-
Mounted Power Modules” for a detailed discussion of
thermal aspects including maximum device
temperatures.
Thermal Derating
Thermal derating is presented for two different
applications: 1) coupled to a cold plate inside a sealed
clamshell chassis, without any internal air circulation,
and 2) traditional open chassis or cards with force air
flow. In application 1, the module is cooled entirely by
conduction of heat from the module primarily through
the top surface to a coldplate, with some conduction
through the module’s pins to the power layers in the
system board; for application 2; the module is cooled
by heat removal into a forced airflow that passes
through the interior of the module and over the top
baseplate and/or an attached heatsink.
0
5
10
15
20
25
30
20
30
40
50
60
70
80
90
100
CASE TEMERATURE, TC, (
oC)
O
U
T
P
U
T
C
U
R
E
N
T
,I
o(A
)
Figure 15. Derating Output Current vs. case
temeprature for FNW700R in Conduction cooling
(cold plate) applications; Ta <72C in vicinity of
module interior; VIN = 48V.
0
5
10
15
20
25
30
20
30
40
50
60
70
80
90
AMBIENT TEMERATURE, TA, (
oC)
O
U
T
P
UT
C
URRE
NT
,I
o(A
)
0.5 m/S
(100 lfm)
1.0 m/S
(200 lfm)
2.0 m/S
(400 lfm)
Figure 16. Derating Output Current vs. Local
Ambient Temperature and Airflow, No Heatsink, Vin
= 48V.
0
5
10
15
20
25
30
20
30
40
50
60
70
80
90
AMBIENT TEMERATURE, TA, (
oC)
O
U
T
P
UT
CURRE
NT
,
Io
(A
)
0.5 m/S
(100 lfm)
1.0 m/S
(200 lfm)
2.0 m/S
(400 lfm)
Figure 17. Derating Output Current vs. Local
Ambient Temperature and Airflow, 1” Transverse
Heatsink, Vin = 48V.
TOP VIEW
23mm
45mm
AIRFLOW
OU
TPUT