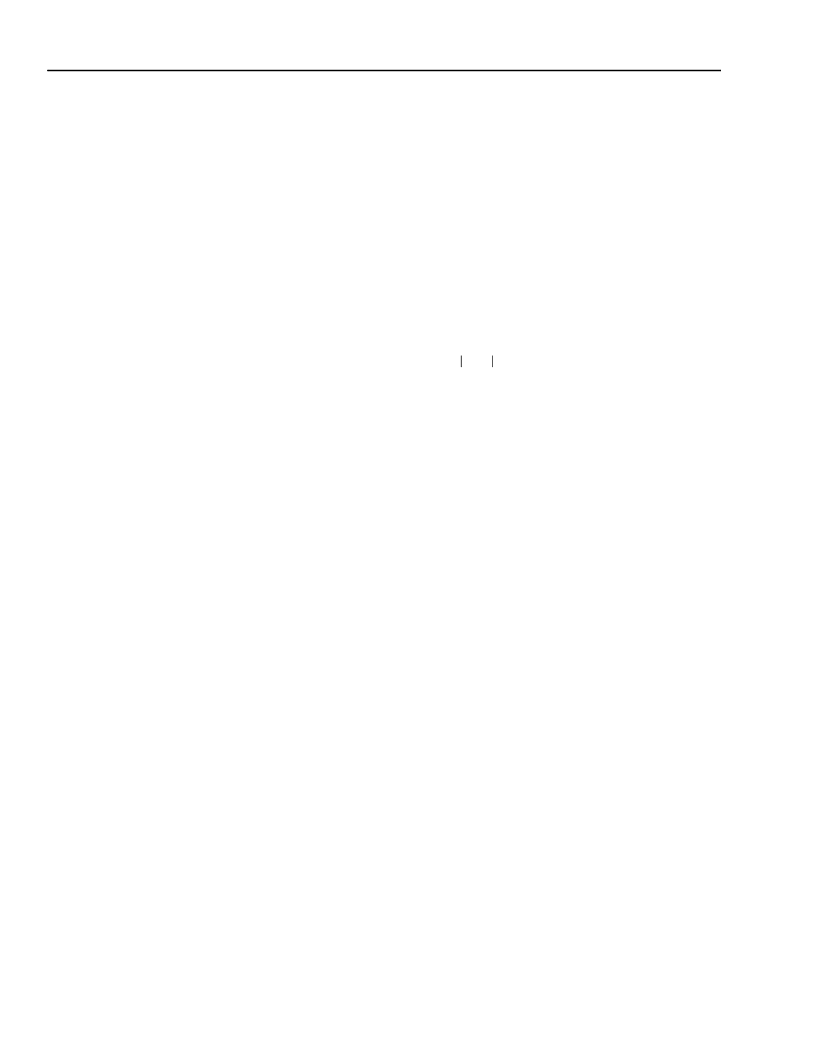
Data Sheet
July 2001
Full-Feature SLIC, Ringing Relay, and Test Access Device
L9310 Line Interface and Line Access Circuit
34
Agere Systems Inc.
Applications
(continued)
dc Characteristics
(continued)
Power Control Resistor
Device temperature rise may be controlled with use of
a single battery voltage by use of a power control resis-
tor. This technique will reduce power dissipation on the
chip, by sharing the total power not dissipated in the
loop between the L9310 and the power control resistor.
It does not, however, reduce the total power con-
sumed, as does use of the auxiliary battery. The power
control resistor is connected from the primary battery to
the V
BAT2
/PWR node of the device.
The magnitude of the power control resistor must be
low enough to ensure that sufficient power is dissipated
on the resistor to ensure the L9310 does not exceed its
thermal shutdown temperature. At the same time, the
more power that is dissipated by the power control
resistor, the higher the resistor’s power rating must be,
and thus, the more costly the resistor. The following
equations are used to optimize the choice (magnitude
and power rating) of the power control resistor.
Again assume:
T
TSD
– T
AMBIENT(max)
= allowed thermal rise
150
°
C – 85
°
C = 65
°
C
Allowed thermal rise =
package thermal impedance x SLIC power dissipation
65
°
C = 38
°
C/W x SLIC power dissipation
Allowed SLIC power dissipation (P
D
) = 1.71 W
This time, assume a maximum ambient operating tem-
perature of 85
°
C, a maximum current limit of 45 mA
(including tolerance), and a maximum battery of –56 V.
Again, assume a (worst-case) minimum dc loop of 0
and that 50
protection resistors are used. Assume
the handset is 200
:
Total P
D
= (56 V x 45 mA) + 0.100 W
Total P
D
= 2.34 W + 0.100 W
Total P
D
= 2.4375 W
Again, the power dissipated in the SLIC is the total
power dissipation less the power that is dissipated in
the loop.
SLIC P
D
= total power – loop power
Loop power = (I
LIM
)
2
x (R
LOOPdcmin
+ 2R
P
+ R
HANDSET
)
Loop power = (45 mA)
2
x (0
+ 100
+ 200
)
Loop power = 0.6075 W
SLIC power = 2.4375 W – 0.6075 W
SLIC power = 1.83 W > 1.5 W
Under these extreme conditions, thermal margin is
increased via an external power control resistor.
The power dissipated in the power control resistor is
calculated by:
P
PRW
=
where in this example:
P
PRW
is power in the resistor
V
BAT
= –52 V
V
LOOP
= I
LIM
* (R
LOOP
+ R
PROT
)
V
ROH
is the ring-side overhead voltage of the SLIC.
Since this device is dc unbalanced, the tip side over-
head will remain typically at –2 V and the ring side over-
head will vary with the voltage at V
OH
. For the total tip/
ring default overhead of 5.5 V, the ring overhead is typi-
cally 3.5 V.
dc Loop Current Limit
In the active modes, dc current limit is programmable
via an applied voltage source at the device’s V
PROG
control input. The voltage source may be an external
voltage source or derived via a resistor divider network
from the V
REF
SLIC output or an external voltage
source. A programmable external voltage source may
be used to provide software control of the loop current
limit. The loop current limit (I
LIM
) is related to the V
PROG
voltage by:
I
LIM
(mA) = 50 x V
PROG
(V)
BAT
----V
V
ROH
R
PWR
–
V
LOOP
–
(
)
2