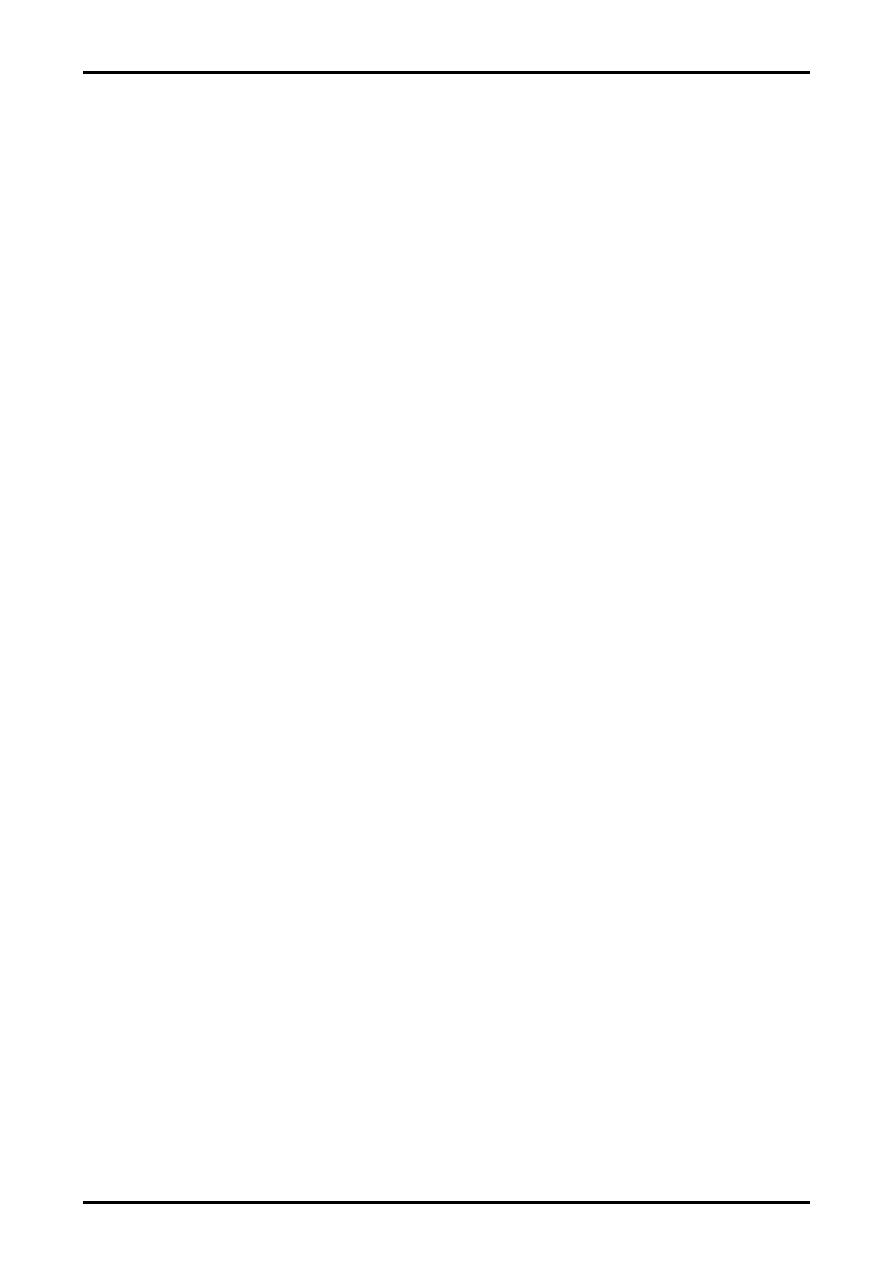
LB1921
No.5439-10/11
15. Sample IC Internal Power Dissipation Calculation (calculated for VCC = 24V and typical rated values)
Power dissipation due to current drain (ICC)
Start mode :
P1 = VCC×ICC1 = 24×34m = 0.82W
Stop mode :
P2 = VCC×ICC2 = 24×8m = 0.19W
Power dissipation when 10mA is drawn from the 7V fixed voltage power supply
P3 = (VCC7)×10m = 17×10m = 0.17W
Power dissipation due to output drive current (when the output on duty is 100%)
P4 = {(VCC1)
2/8k}+{(VCC2)2/10k}
= (232/8k)+(222/10k) = 0.12W
Power dissipation in the output drive transistors (when IO = 2A and the output on duty is 100%)
P5 = VO sat2×IO = 2.7×2 = 5.4W
Therefore, the total power dissipation for the whole IC is :
In stop mode :
P = P2 = 0.19W
In start mode :
P = P1+P3+P4+P5 = 6.51W
(For a output on duty of 100%)
16. IC Temperature Rise Measurement Techniques
Thermocouple measurement
Attach the thermocouple to a fin on the heat sink when using a thermocouple to measure the IC temperature. This
technique is simple but is subject to large measurement errors when the heat generation is not consistent.
Measurement using IC internal diode characteristics
We recommend using the parasitic diode that exists between the INT.IN and ground in this IC. (According to
Sanyo data, the temperature characteristic of this diode is about 1.8V/
°C for ID = 1mA.) The external resistor
must be removed during testing.
17. Servo Constants
Since the servo constant calculation depends strongly on the motor characters and requires significant expertise, we
recommend that the motor manufacturer determine the constants in normal cases. Sanyo can provide the required
IC characteristics data for the servo constant calculations and frequency characteristics simulation data for the filter
characteristics specified by the motor manufacturer.
When the resistor (R10) inserted between DOUT and INT.IN is too small, C8 and C9 will become too large and if
R10 is too large speed errors become more likely to occur due to the speed discriminator cutoff and the integrator
input current. Therefore, a value of between 10 and 100k
is advisable. If the resistor (R8) inserted between POUT
and INT.IN is too small, the influence of the PLL system will be too large and pull-in to synchronization with the
lock state will degrade. Therefore, this resistor must not be too small. We recommend a value of around 1M
when
R10 is 75k
. First determine the constants for the speed discriminator (R9, R10, C8 and C9) and then determine the
value of R8 in the PLL system.