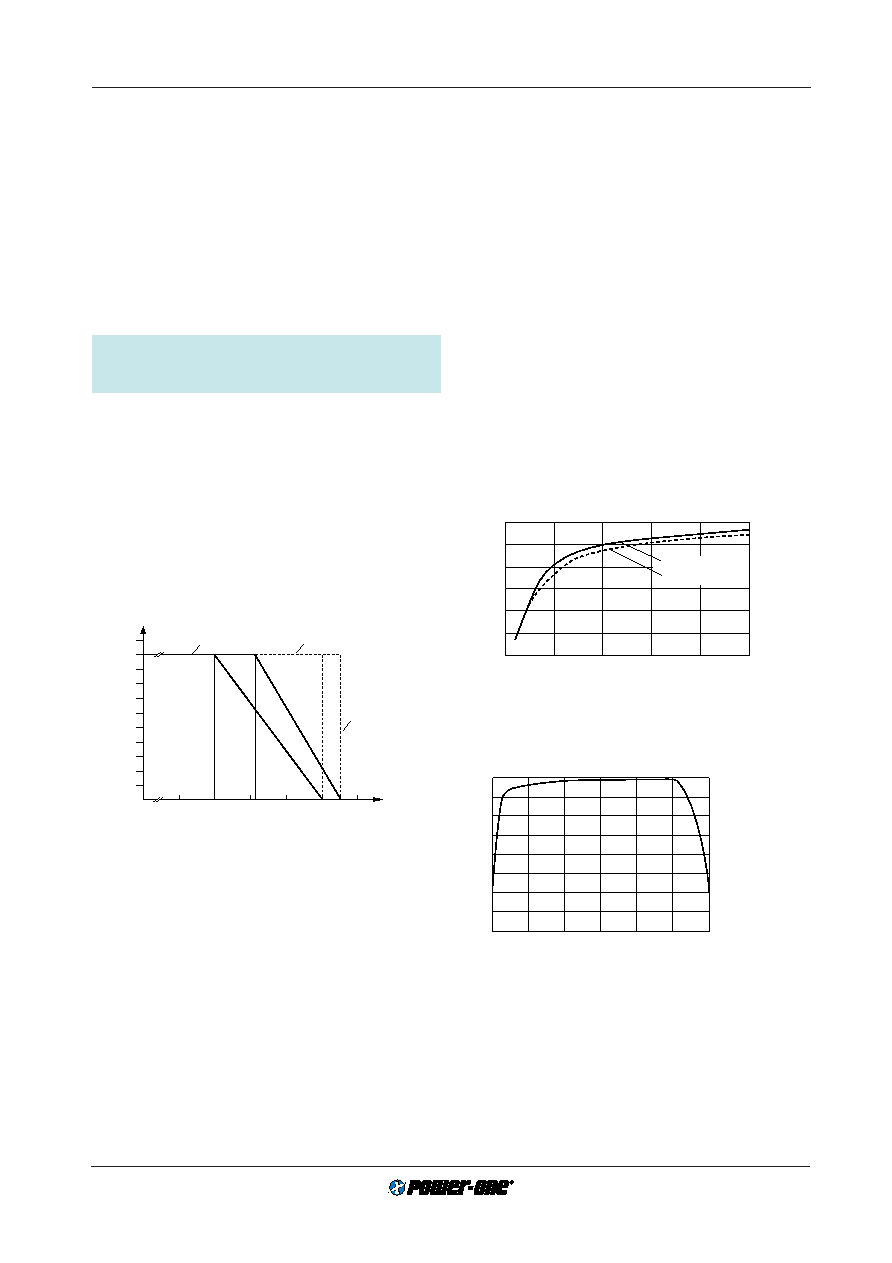
Cassette Style
AC-DC Converters
S Series PFC
Edition 5/5.2000
10/28
Thermal Protection
A temperature sensor generates an internal inhibit signal
which disables the outputs if the case temperature exceeds
TC max. The outputs are automatically re-enabled if the tem-
perature drops below this limit.
Output Protection
Each output is protected against overvoltage which could
occur due to a failure of the control circuit by means of a
voltage suppressor diode which, under worst case condi-
tions, may become a short circuit. The suppressor diodes
are not designed to withstand externally applied over-
voltages. Overload at any of the two outputs will cause a
shut-down of both outputs. A red LED indicates the over-
load condition.
Thermal Considerations
If a converter is located in free, quasi-stationary air (con-
vection cooling) at the indicated maximum ambient tem-
perature
TA max (see table: Temperature specifications) and
is operated at its nominal input voltage and output power,
the temperature measured at the
Measuring point of case
temperature TC (see: Mechanical Data) will approach the
indicated value
TC max after the warm-up phase. However,
the relationship between
TA and TC depends heavily on the
conditions of operation and integration into a system. The
thermal conditions are influenced by input voltage, output
current, airflow and temperature of surrounding compo-
nents and surfaces.
TA max is therefore, contrary to TC max,
an indicative value only.
Caution: The installer must ensure that under all operat-
ing conditions
TC remains within the limits stated in the
table:
Temperature specifications.
Notes: Sufficient forced cooling or an additional heat sink
allows
TA to be higher than 71
°C (e.g. 85°C) if T
C max is not
exceeded.
For -7 or -9 units at an ambient temperature
TA of 85
°C with
only convection cooling, the maximum permissible current
for each output is approx. 40% of its nominal value as per
figure.
It is recommended that continuous operation under simulta-
neous extreme worst case conditions of the following three
parameters be avoided: Minimum input voltage, maximum
output power and maximum temperature.
-6 versions have reduced
TA and TC
0
0.1
0.2
0.3
0.4
0.5
0.6
0.7
0.8
TA min 50
60
70
80
90
100
Io/Io nom
TA [°C]
0.9
1.00
forced cooling
convection cooling
TC max
-6 -7
-6
-7
05139
Fig. 8
Output current derating versus temperature for –7 and –9
units.
Efciency versus Load
0.2
0.4
0.6
0.8
1
0
0.90
0.30
0.40
0.50
0.60
0.70
0.80
Efficiency
Io/Io nom
Ui = 230 V AC
Ui = 85 V AC
05007
Fig. 9
Efciency versus load at Ui; 230 V AC and 88 V AC
Switching Frequency versus Load
0.2
0.4
0.6
0.8
1
0
60
0
10
20
30
40
50
Frequency [kHz]
load [Io/Io nom]
70
80
1.2
05008
Fig. 10
Switching frequency versus load. (The boost converter at
the input stage has a xed frequency of 100 kHz)
Parallel or Series Connection of Units
Single or double output units with equal nominal output volt-
age can be connected in parallel without any precautions
using option T.
With option T (current sharing), all units share the current
approximately equally.
Single output units and/or main and second outputs of dou-
ble output units can be connected in series with any other
(similar) output.
Note:
– Parallel connection of double output units should always
include both, main and second output to maintain good
regulation of both outputs.
– Not more than 5 units should be connected in parallel.
– Series connection of second outputs without involving
their main outputs should be avoided as regulation may
be poor.
– The maximum output current is limited by the output with
the lowest current limitation if several outputs are con-
nected in series.