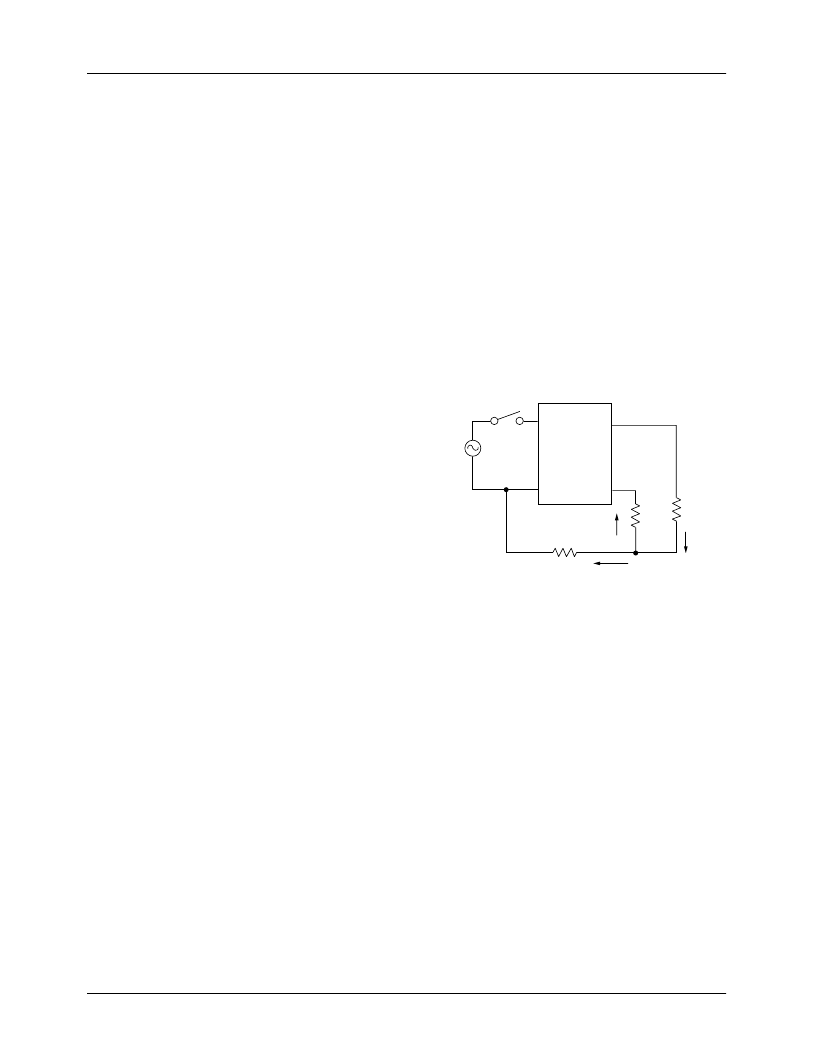
LM1851
PRODUCT SPECIFICATION
6
Applications Discussion
A typical ground fault interrupter circuit is shown in
Figure 10. It is designed to operate on 120 VAC line voltage
with 5 mA normal fault sensitivity.
A full-wave rectifier bridge and a 15k/2W resistor are used
to supply the dc power required by the IC. A 1
m
F capacitor
at pin 8 is used to filter the ripple of the supply voltage and is
also connected across the SCR to allow firing of the SCR on
either half-cycle. When a fault causes the SCR to trigger, the
circuit breaker is energized and line voltage is removed from
the load.
At this time no fault current flows and the C
T
discharge cur-
rent increases from I
TH
to 3I
TH
(see Block Diagram). This
quickly resets both the timing capacitor and the output latch.
The circuit breaker can be reset and the line voltage again
supplied to the load, assuming the fault has been removed. A
1000:1 sense transformer is used to detect the normal fault.
The fault current, which is basically the difference current
between the got and neutral lines, is stepped down by 1000
and fed into the input pin of the operational amplifier
through a 10
m
F capacitor. The 0.0033
m
F capacitor between
pin 2 and pin 3 and the 200 pF between pins 3 and 4 are
added to obtain better noise immunity. The normal fault sen-
sitivity is determined by the timing capacitor discharging
current, I
TH
. I
TH
can be calculated by:
(1)
At the decision point, the average fault current just equals the
threshold current, I
TH
.
(2)
Where I
F
(rms) is the rms input fault current to the opera-
tional amplifier and the factor of 2 is due to the fact that I
F
charges the timing capacitor only during one half-cycle,
while I
TH
discharges the capacitor continuously. The factor
0.91 converts the rms value to an average value. Combining
equations (1) and (2) we have:
(3)
For example, to obtain 5 mA(rms) sensitivity for the circuit
in Figure 7 we have:
(4)
I
TH
R
SET
-7V
2
=
I
TH
I
rms
(
2
)
-------------------
0.91
′
=
R
SET
)
I
F
rms
(
0.91
′
-------------7V
=
R
SET
1000
5 mA
0.91
----------7V
1.5M
W
=
=
The correct value for R
SET
can also be determined from the
characteristic curve that plots equation (3). Note that this is
an approximate calculation; the exact value of R
SET
depends
on the specific sense transformer used and LM1851 toler-
ances. Inasmuch as UL943 specifies a sensitivity “window”
of 4 mA to 6mA, provision should be made to adjust R
SET
with a potentiometer.
Independent of setting sensitivity, the desired integration
time can be obtained through proper selection of the timing
capacitor, C
T
. Due to the large number of variables involved,
proper selection of C
T
is best done empirically. The follow-
ing design example should only be used as a guideline.
Assume the goal is to meet UL943 timing requirements.
Also assume that worst case timing occurs during GFI start-
up (S1 closure) with both a heavy normal fault and a 2
W
grounded neutral fault present. This situation is shown dia-
grammatically in Figure 8.
Figure 8.
UL943 specifies
£
25 ms average trip time under these condi-
tions. Calculation of C
T
based upon charging currents due to
normal fault only is as follows:
1.
Start with a
£
25 ms specification. Subtract 3 ms GFI
turn-on time (15k and 1
m
F). Subtract 8 ms potential
loss of one half-cycle due to fault current sense of half-
cycles only.
2.
Subtract 4 ms time required to open a sluggish circuit
breaker.
3.
This gives a total
£
10 ms maximum integration time that
could be allowed.
4.
To generate 8 ms value of integration time that accom-
modates component tolerances and other variables:
(5)
65-1851-12
Line
Neutral
Hot
S1
GFI
Hot
Neutral
R
B
500
I
R
B
500
(0.2)I
(0.8)I
R
N
0.4
C
T
1
T
′
V
=