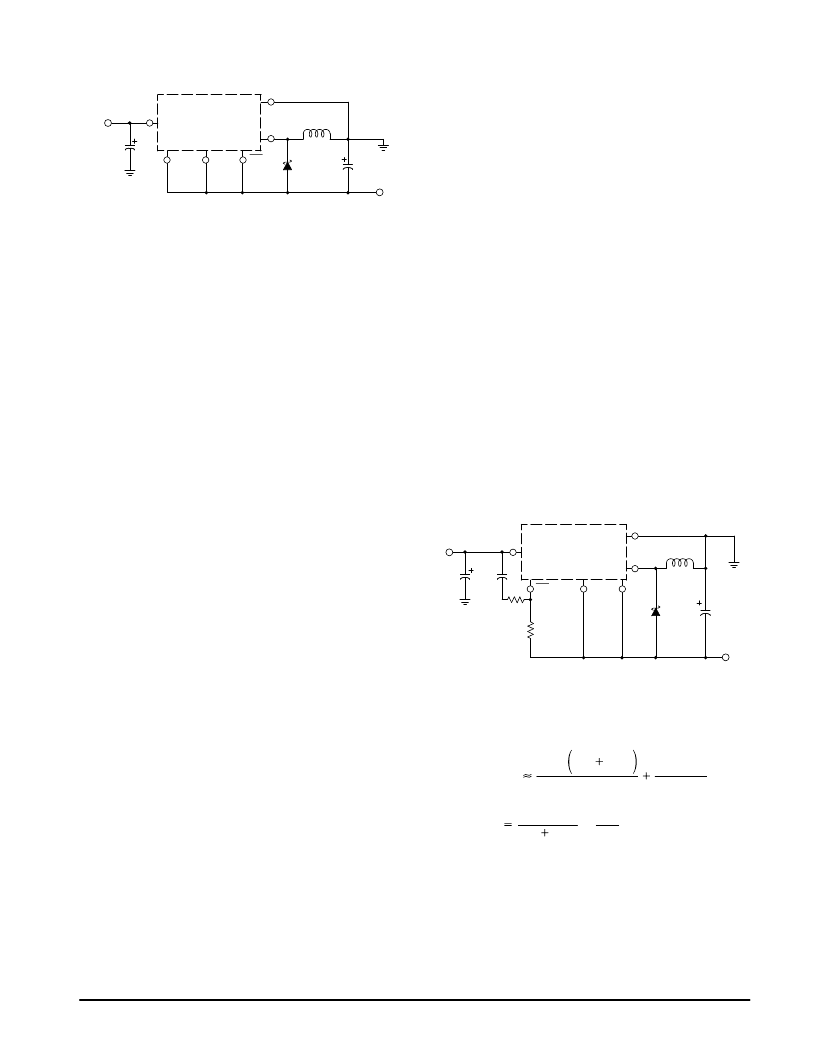
LM2574
18
MOTOROLA ANALOG IC DEVICE DATA
D1
MBR150
L1
68
μ
H
Output
7
1
Feedback
8.0 to 25 V
Unregulated
DC Input
Cin
22
μ
F
5
3
4
ON/OFF
Pwr
Gnd
+Vin
–12 V @ 100 mA
Regulated
Output
Cout
680
μ
F
LM2574–12
2
Sig
Gnd
Figure 27. Inverting Buck–Boost Develops –12 V
The dynamic switching losses during turn–on and turn–off
can be neglected if a proper type catch diode is used. The
junction temperature can be determined by the following
expression:
TJ = (R
θ
JA)(PD) + TA
where (R
θ
JA)(PD) represents the junction temperature rise
caused by the dissipated power and TA is the maximum
ambient temperature.
Some Aspects That can Influence Thermal Design
It should be noted that the package thermal resistance and
the junction temperature rise numbers are all approximate,
and there are many factors that will affect these numbers,
such as PC board size, shape, thickness, physical position,
location, board temperature, as well as whether the
surrounding air is moving or still. At higher power levels the
thermal resistance decreases due to the increased air
current activity.
Other factors are trace width, total printed circuit copper
area, copper thickness, single– or double–sided, multilayer
board, the amount of solder on the board or even color of the
traces.
The size, quantity and spacing of other components on the
board can also influence its effectiveness to dissipate the
heat. Some of them, like the catch diode or the inductor will
generate some additional heat.
ADDITIONAL APPLICATIONS
Inverting Regulator
An inverting buck–boost regulator using the LM2574–12 is
shown in Figure 27. This circuit converts a positive input
voltage to a negative output voltage with a common ground
by bootstrapping the regulators ground to the negative output
voltage. By grounding the feedback pin, the regulator senses
the inverted output voltage and regulates it.
In this example the LM2574–12 is used to generate a –12 V
output. The maximum input voltage in this case cannot
exceed 28 V because the maximum voltage appearing
across the regulator is the absolute sum of the input and
output voltages and this must be limited to a maximum of 40 V.
This circuit configuration is able to deliver approximately
0.1 A to the output when the input voltage is 8.0 V or higher.
At lighter loads the minimum input voltage required drops to
approximately 4.7 V, because the buck–boost regulator
topology can produce an output voltage that, in its absolute
value, is either greater or less than the input voltage.
Since the switch currents in this buck–boost configuration
are higher than in the standard buck converter topology, the
available output current is lower.
This type of buck–boost inverting regulator can also
require a larger amount of startup input current, even for light
loads. This may overload an input power source with a
current limit less than 0.6 A.
Because of the relatively high startup currents required by
this inverting regulator topology, the use of a delayed startup
or an undervoltage lockout circuit is recommended.
While using a delayed startup arrangement, the input
capacitor can charge up to a higher voltage before the
switch–mode regulator begins to operate.
The high input current needed for startup is now partially
supplied by the input capacitor Cin.
Design Recommendations:
The inverting regulator operates in a different manner than
the buck converter and so a different design procedure has to
be used to select the inductor L1 or the output capacitor Cout.
The output capacitor values must be larger than what is
normally required for buck converter designs. Low input
voltages or high output currents require a large value output
capacitor (in the range of thousands of
μ
F).
The recommended range of inductor values for the
inverting converter design is between 68
μ
H and 220
μ
H. To
select an inductor with an appropriate current rating, the
inductor peak current has to be calculated.
D1
MBR150
L1
68
μ
H
Output
7
1
Feedback
12 to 25 V
Unregulated
DC Input
Cin
22
μ
F
/50 V
5
4
3
ON/OFF
Pwr
Gnd
+Vin
–12 V @ 100 mA
Regulated
Output
Cout
μ
F
/16 V
LM2574–12
C1
0.1
μ
F
R1
47 k
R2
47 k
2
Sig
Gnd
Figure 28. Inverting Buck–Boost Regulator with
Delayed Startup
The following formula is used to obtain the peak inductor
current:
Ipeak
ILoadVin
|VO|
Vin
Vinx ton
2L1
where ton
|VO|
Vin
|VO|xfosc, and fosc = 52 kHz.
Under normal continuous inductor current operating
conditions, the worst case occurs when Vin is minimal.
It has been already mentioned above, that in some
situations, the delayed startup or the undervoltage lockout
features could be very useful. A delayed startup circuit