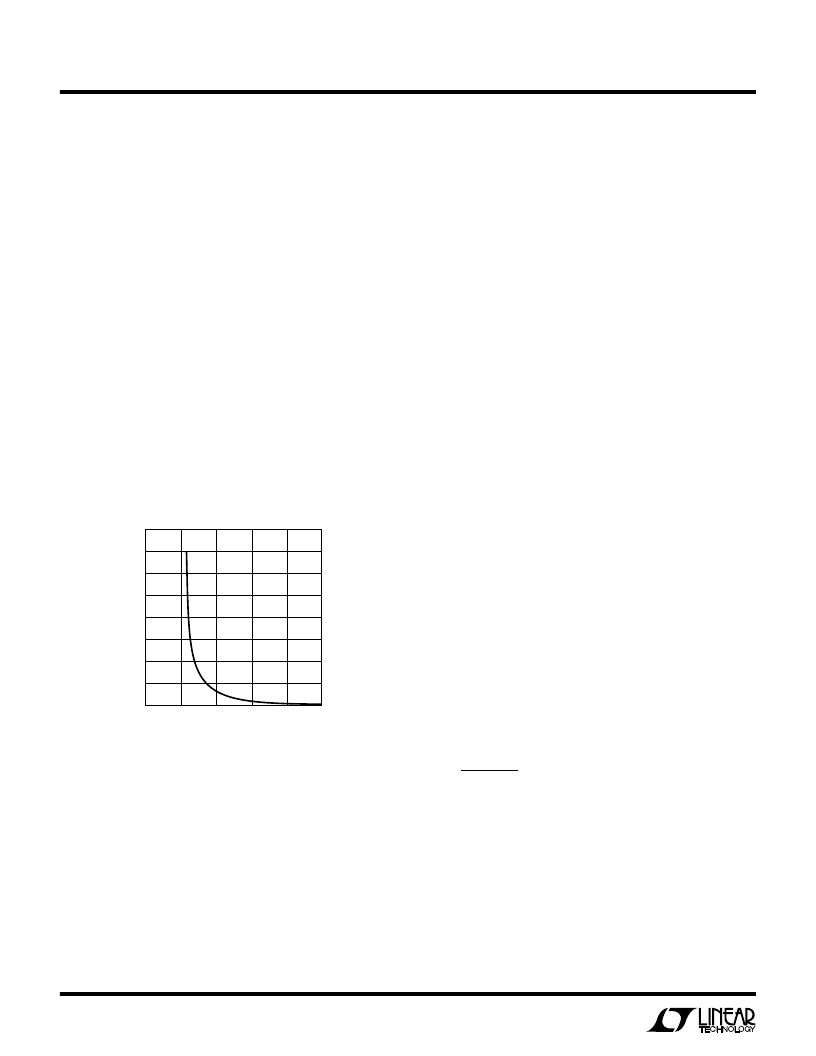
16
LT1432
Inductor Selection
Inductor selection would be easy if money and space didn’t
count. Unfortunately, these two factors usually count the
most, and compromises must be made. High efficiency
converters generally cannot afford the core loss found in
low cost powdered iron cores, forcing the use of more
expensive cores such as ferrite, molypermalloy, or KoolM
μ
.
Actual core loss is independent of core size for a fixed
inductor value, but it is very dependent on inductance
selected. As inductance increases, core loss goes down.
Unfortunately, increased inductance requires more turns
of wire and therefore copper loss will increase. The trick is
to find the smallest inductor whose inductance is high
enough to limit core loss, and whose series resistance is
low enough to limit copper loss. Historically, inductor
manufacturers have a tendency to be ultra conservative
when designing inductors, and unless you are very specific
about your constraints and requirements, they will more
often than not come up with a unit which is 50% larger than
the optimum. Part of this is due to manufacturing consid-
erations. The trade-off of core loss and copper loss is
optimized by “filling the winding window” with wire, but
especially for toroids this can require more expensive
winding techniques than the widely used “single layer”
design. The lesson here is to spend time with the manufac-
turer exploring the cost trade-offs of different inductor
designs. The following guidelines may be helpful in this
regard.
1. For most buck converter applications using the
LT1070, LT1170, or LT1270 families of parts at 40kHz to
100kHz, inductor value will be in the range of 25
μ
H to
200
μ
H. The lower values would be used for higher output
currents and/or higher frequencies, with higher values
used for low output current, low frequency applications.
Lower inductance obviously means smaller size, but at
some point the core loss will begin to hurt, or the large
peak-to-peak inductor currents will cause high output
ripple voltage or limit available output current. The follow-
ing formula is a rough guide for picking an initial inductor
value:
8
I
f
MAX
I
MAX
= maximum load current, including surges
f = switching frequency
This formula assumes that a switcher IC is selected which
has a maximum switch current of 1.5 to 2.5 times maxi-
mum load current. For a 2.5A design using the LT1271 at
60kHz, L would calculate to 53
μ
H. This formula is very
arbitrary, so do not hesitate to modify the calculated value
by as much as 2:1 if the need arises. Keep in mind that all
the IC switchers have a peak current rating which is a
L
=
(
)( )
U
S
A
O
PPLICATI
IU
U
At heavy loads, switch on-resistance increases minimum
input voltage. With an LT1071 for instance, minimum
input is 6.1V at 1A load, but increases to 6.3V at 2A load.
If absolute minimum input voltage is needed, use lower
frequency devices with higher current rating than is actu-
ally needed. The LT1070, for instance, operates down to
6.15V at 2A. Current limit is defined by the LT1432, so
higher current switchers used in lower current applica-
tions do not degrade performance or reliability.
Minimum Load Current in Normal Mode
There is a minimum load current requirement in normal
mode. This is caused by the necessity to “pump” the IC
switcher floating power supply capacitor during switch
“off” time. This pumping current comes from inductor
current, so load current must not be allowed to drop too
low, or the floating bias supply for the switcher will
collapse. Minimum load current is a function of input
voltage as shown in Figure 16.
INPUT VOLTAGE (V)
0
M
30
40
50
15
25
LT1432 F15
20
10
0
5
10
20
60
70
80
Figure 16. Minimum Normal Mode Load Current