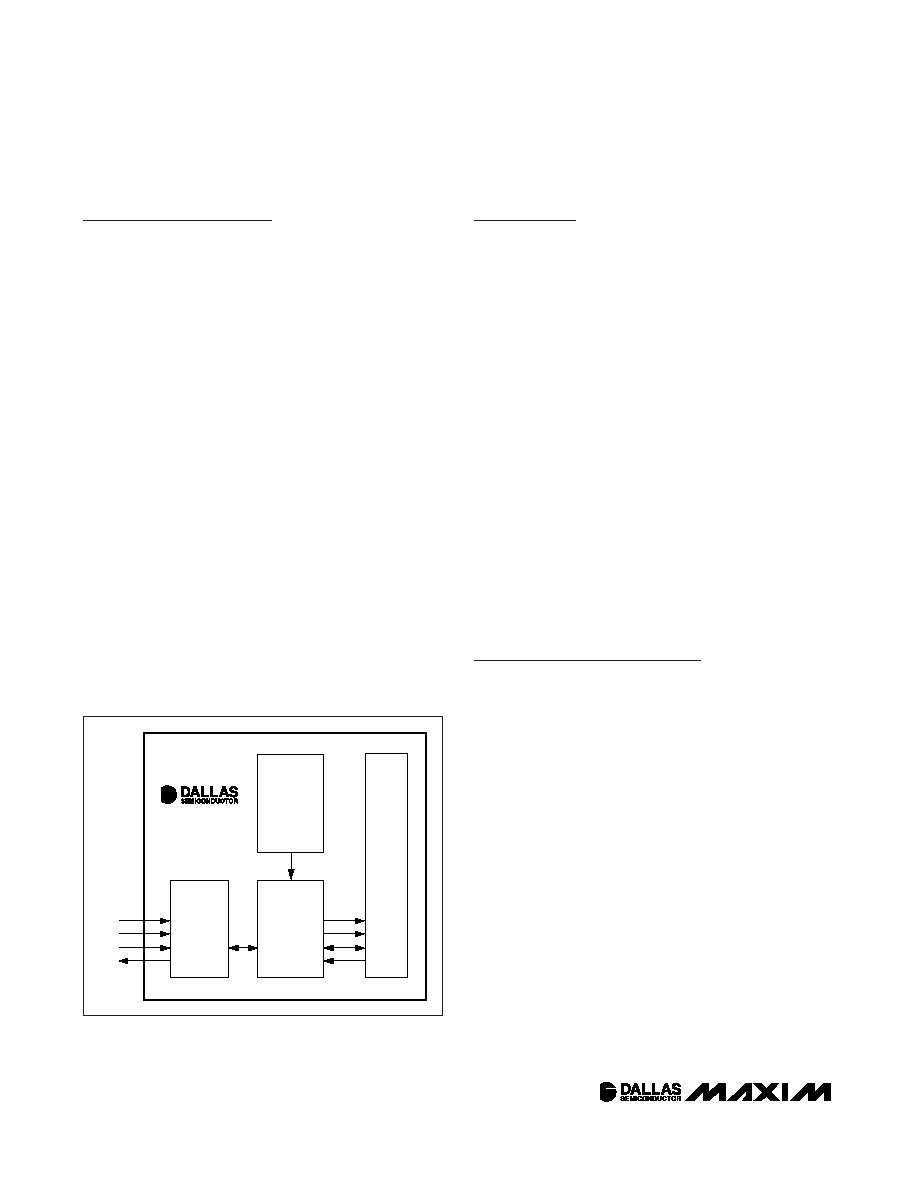
MAXQ3210
In-Circuit Debug
Embedded debugging capability is available through
the JTAG-compatible Test Access Port. Embedded
debug hardware and embedded ROM firmware pro-
vide in-circuit debugging capability to the user applica-
tion, eliminating the need for an expensive in-circuit
emulator. Figure 5 shows a block diagram of the in-cir-
cuit debugger. The in-circuit debug features include:
Hardware debug engine
Set of registers able to set breakpoints on register,
code, or data accesses
Set of debug service routines stored in the utility
ROM
The embedded hardware debug engine is an indepen-
dent hardware block in the microcontroller. The debug
engine can monitor internal activities and interact with
selected internal registers while the CPU is executing
user code. Collectively, the hardware and software fea-
tures allow two basic modes of in-circuit debugging:
Background mode allows the host to configure and
set up the in-circuit debugger while the CPU contin-
ues to execute the application software at full
speed. Debug mode can be invoked from back-
ground mode.
Debug mode allows the debug engine to take con-
trol of the CPU, providing read/write access to inter-
nal registers and memory, and single-step trace
operation.
Applications Information
Grounds and Bypassing
Careful PC board layout significantly minimizes crosstalk
among the reference input, comparator outputs, and dig-
ital inputs. Keep digital and analog lines separate, and
use ground traces as shields between them where pos-
sible. Separate CMPI and VREF from each other by run-
ning a ground trace between these pins. Bypass VDD
with a capacitor as low as 1F and keep bypass capaci-
tor leads short for best noise rejection.
Capacitor Selection and
Regulator Stability
For general purposes, use a combination of a 10F and
0.1F capacitor on REGOUT. Note that the 0.1F
capacitor is always required on REGOUT and must be
a good quality ceramic with low ESR. The internal regu-
lator is designed to be stable with an output filter
capacitor as low as 4.7F and an ESR as high as 6
Ω.
Larger REGOUT capacitor values and lower ESR pro-
vide better supply-noise rejection and transient
response. Note that some ceramic dielectric materials
(e.g., Z5U and Y5V) exhibit a large temperature coeffi-
cient for both capacitance and ESR, and a larger
REGOUT capacitance may be needed to ensure stabil-
ity at low temperatures.
Applications
The low-power, high-performance RISC architecture of
the MAXQ3210 makes it an excellent fit for many
portable or battery-powered applications that require
cost-effective computing. The analog comparator can
function as an A/D converter when simple analog mea-
surements are necessary, and the high-current I/O pin
can drive a power or status LED. Combined with the
high-output piezoelectric horn/transducer, the micro-
controller can function as both the “brain” and “mouth”
in a wide variety of monitoring applications.
The microcontroller includes an on-chip voltage regula-
tor that allows it to be powered directly off a 9V battery.
A low-battery detector allows the microcontroller to
monitor its own battery condition. The internal voltage
regulator can also drive external 5V circuitry while a 9V
battery drives the system.
This device can also be used as a low-cost analog-to-
digital converter (ADC). The single-slope conversion
method can be easily implemented using the internal
comparator and an internal timer. The basic implemen-
tation of such a converter is illustrated below. One of
the benefits of this approach is the small number of
Microcontroller with Internal Voltage Regulator,
Piezoelectric Horn Driver, and Comparator
22
____________________________________________________________________
TAP
CONTROLLER
CPU
DEBUG
ENGINE
DEBUG
SERVICE
ROUTINES
(UTILITY ROM)
TMS
TCK
TDI
TDO
CONTROL
BREAKPOINT
ADDRESS
DATA
MAXQ3210
Figure 5. In-Circuit Debugger