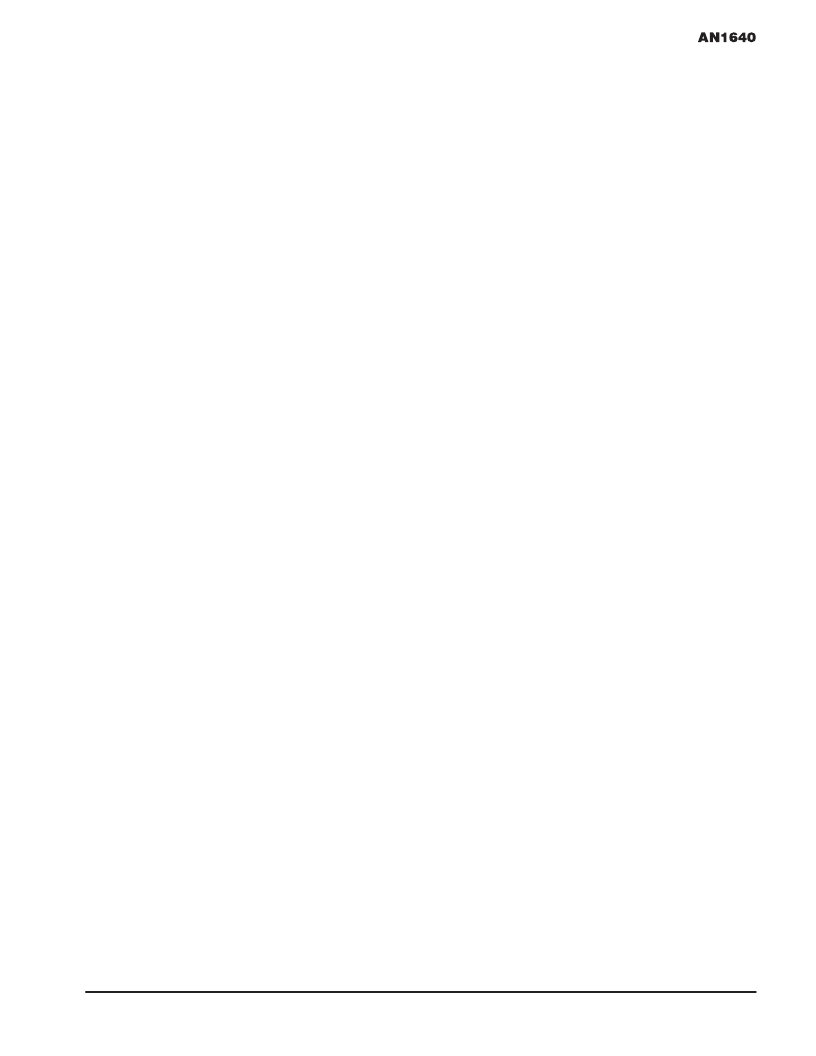
2–103
Motorola Sensor Device Data
For More Information On This Product,
Go to: www.freescale.com
voltage will result in the same proportional change in the
output. For example, if the 5 V supply were to change by 10%,
from 5.0 V to 5.5 V, the accelerometer offset will change by
10% also, from 2.5 V to 2.75 V. This phenomena would also
occur if the ground were to shift. A 100 mV change in ground
would result in a 50 mV change in the output. If the
accelerometer does not have low impedance path to ground
and parasitics from a poor ground are present as a result, the
ground seen by the accelerometer may change over
frequency. So, during a BCI test, if the 5.0 V supply does not
shift but the output of the accelerometer does, the ground to
the accelerometer may be moving.
It was found with some experimentation that the offset shift
can be eliminated with proper board layout techniques as
described below.
PROPER LAYOUT TECHNIQUES
Since the Motorola accelerometer is a sensitive analog
device that relies on a clean supply to function within
established parameters, there are some techniques that can
be employed to minimize the effects of BCI on the
accelerometer performance. PCB layout is paramount to
reducing susceptibility to BCI.
A low impedance path to ground will provide shunting of the
high frequency interference and minimize its effect on the
accelerometer. The best way to provide a good path is by
putting a solid, unbroken ground plane in the PCB. This
ground plane should be shunted to chassis ground at the
module connector. This will ensure that the high frequency
BCI will be shunted before interfering with accelerometer
performance.
All accelerometer pins that require ground connection
should be tied together to a common ground.
Traces attached directly to the connector pins can receive
high RF noise, which can couple to nearby traces and com-
ponents. Increasing series impedance of the traces helps
reduce the couple or conducted noise. High frequency fil-
ters on the supply line and other susceptible lines may be
required to filter out high frequency interference introduced
by the BCI test. Signal lines that carry low current can toler-
ate series resistances of 100–200
.
Decoupling capacitors on every input line to the common
ground plane will help shunt the high frequency away from
the system. These should be placed near the connector.
Signal trace lengths to and from the accelerometer should
be kept at a minimum. The shorter the trace, the less
chance it has of picking up high frequency BCI signals as
it crosses the board. Trace lengths can be reduced by plac-
ing the accelerometer and the microcontroller as close
together as possible. Signal and ground traces looping
should be minimized.
A decoupling capacitor on the accelerometer Vcc pin will
also help minimize BCI effects. The recommended value is
0.1
μ
F. This capacitor should be placed as close as pos-
sible to the accelerometer to achieve the best results.
To maximize ratiometricity, the accelerometer Vcc and the
microcontroller A/D reference pin should be on the same
trace. The accelerometer ground and the microcontroller
ground should also share the same ground point. There-
fore, when there is signal interference due to BCI, the A/D
converter and the accelerometer will see the interference
at the same level. This will result in the same digital code
representation of acceleration without signal interference.
A clean power supply to both the accelerometer and the
microcontroller should be provided. Supply traces should
avoid high current traces that might carry high RF currents
during the BCI test. The traces should be as short as
possible.
The accelerometer should be placed on the opposite end
of the PCB away from the connector. The farther the dis-
tance, the lower the chance high frequency RF from BCI
will interfere with the accelerometer.
The accelerometer should be placed away from high cur-
rent paths that may carry high RF currents during the BCI
test.
Automotive customers will continue to require airbag
systems to have high standards for EMC. One way to test for
EMC is perform the Bulk Current Injection test. Because of the
high current involved, BCI is one of the most difficult EMC tests
to pass. Being part of the airbag system, the accelerometer
must continue to function normally under application of high
frequency BCI. The accelerometer is highly sensitive to
placement on the board and its connection to ground. Poor
design will caused the device to fail the BCI test. The practice
of good PCB layout, device placement and good grounding
will allow the accelerometer to function within specification
and pass the BCI test.
F
Freescale Semiconductor, Inc.
n
.