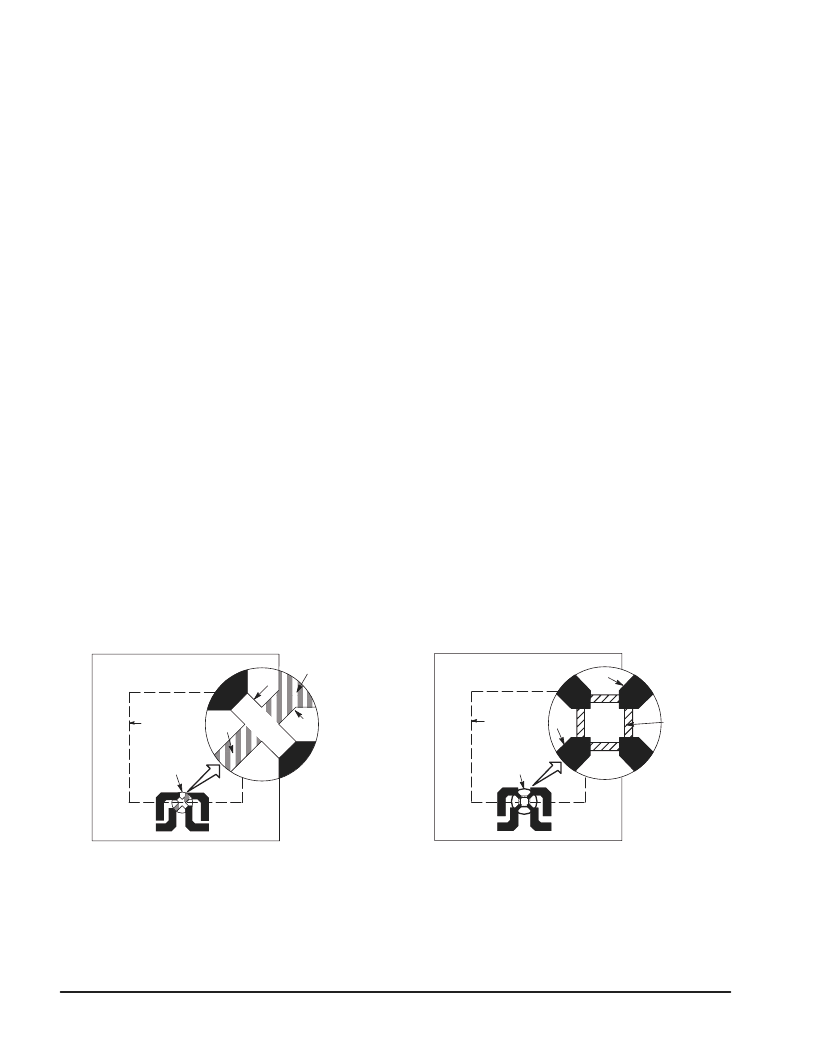
3–8
Motorola Sensor Device Data
For More Information On This Product,
Go to: www.freescale.com
Motorola Pressure Sensors
INTRODUCTION
Motorola pressure sensors combine advanced piezoresistive sensor architecture with integrated circuit technology to offer a
wide range of pressure sensing devices for automotive, medical, consumer and industrial applications. Selection versatility
includes choice of:
Pressure Ranges in PSI
0 to 1.45, 0 to 6, 0 to 7.3, 0 to 14.5, 0 to 29, 0 to 75, 0 to 100,
0 to 150 psi.
Sensing Options
Uncompensated, Temperature Compensated/Calibrated,
and Signal Conditioned (with on–chip amplifiers)
Application Measurements
Absolute, Differential, Gauge
Package Options
Basic Element, Ported Elements for specific measurements
Surface Mount and Through Hole, Low Profile packages
THE BASIC STRUCTURE
The Motorola pressure sensor is designed utilizing a
monolithic silicon piezoresistor, which generates a changing
output voltage with variations in applied pressure. The
resistive element, which constitutes a strain gauge, is ion
implanted on a thin silicon diaphragm.
Applying pressure to the diaphragm results in a resistance
change in the strain gauge, which in turn causes a change in
the output voltage in direct proportion to the applied
pressure. The strain gauge is an integral part of the silicon
diaphragm, hence there are no temperature effects due to
differences in thermal expansion of the strain gauge and the
diaphragm. The output parameters of the strain gauge itself
are temperature dependent, however, requiring that the
device be compensated if used over an extensive tempera-
ture range. Simple resistor networks can be used for narrow
temperature ranges, i.e., 0
°
C to 85
°
C. For temperature
ranges from –40
°
C to +125
°
C, more extensive compensa-
tion networks are necessary.
MOTOROLA’S LOCALIZED SENSING ELEMENTS
Excitation current is passed longitudinally through the
resistor (taps 1 and 3), and the pressure that stresses the
diaphragm is applied at a right angle to the current flow. The
stress establishes a transverse electric field in the resistor
that is sensed as voltage at taps 2 and 4, which are located
at the midpoint of the resistor (Figure 3a).
The transducer (Figure 3) uses a single element eliminat-
ing the need to closely match the four stress and tempera-
ture sensitive resistors that form a distributed Wheatstone
bridge design. At the same time, it greatly simplifies the
additional circuitry necessary to accomplish calibration and
temperature compensation. The offset does not depend on
matched resistors but instead on how well the transverse
voltage taps are aligned. This alignment is accomplished in
a single photolithographic step, making it easy to control,
and is only a positive voltage, simplifying schemes to zero
the offset.
Figure 3. X–ducer
Sensor Element — Top View
PIN #
1. GROUND
2. +VOUT
3. VS
4. –VOUT
ETCHED
DIAPHRAGM
BOUNDARY
TRANSVERSE
VOLTAGE STRAIN
GAUGE RESISTOR
ELEMENT
S+
S –
VOLTAGE
TAPS
3
2
1
4
ETCHED
DIAPHRAGM
BOUNDARY
TRANSVERSE
VOLTAGE STRAIN
GAUGE RESISTOR
ACTIVE ELEMENT
HAS FOUR
P– RESISTORS
S+
S –
3
2
1
4
PIN #
1. GROUND
2. +VOUT
3. VS
4. –VOUT
Figure 3a. Localized Sensing Element
F
Freescale Semiconductor, Inc.
n
.