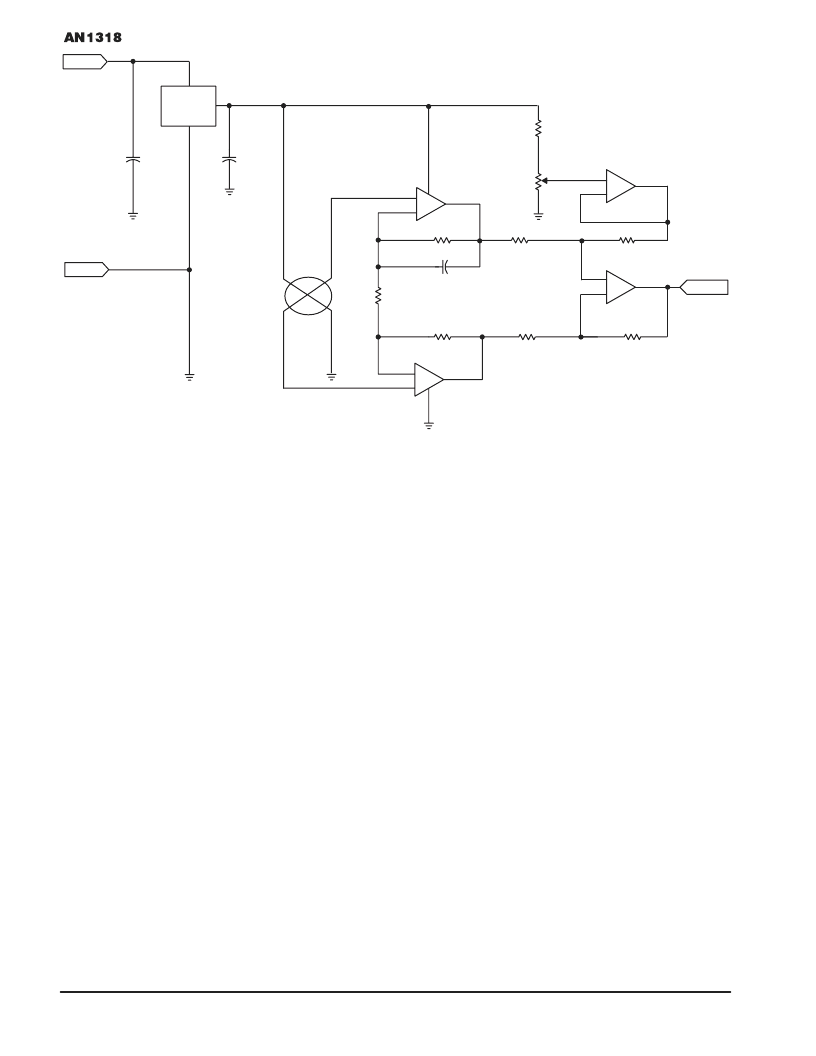
3–270
Motorola Sensor Device Data
For More Information On This Product,
Go to: www.freescale.com
Figure 2. Instrumentation Amplifier Interface
B+
GND
C1
1
μ
F
C2
0.1
μ
F
C3 .001
μ
F
U2
MC78L08ACP
U1B
MC33274
I
G
O
3
R7
7.5 k
R6
1 k
12
13
14
8
R2
1 k
R5
R9
15 k
1 k
U1A
MC33274
R10
240*
5
6
4
7
R4
1 k
R3 1 k
U1C
MC33274
10
9
2
3
1
2
3
4
1
XDCR1
MPX2000 SERIES
PRESSURE SENSOR
OUTPUT
11
2
R8 15 k
+
–
+
–
+
–
–
+
U1D
MC33274
* NOTE: FOR MPX2010, R10 = 150 OHMS
ZERO
1
For applications requiring greater precision a fully
integrated instrument amplifier such as an LTC1100CN8 gives
better results. In Figure 3 one of these amplifiers is used to
provide a gain of 100, as well as differential to single ended
conversion. Zero offset is provided by dividing down the
precision reference to 0.5 V and buffering with U2B. This
voltage is fed into the LTC1100CN8’s ground pin which is
equivalent to returning R3 to pin 14 of U1D in Figure 2. An
additional non–inverting gain stage consisting of U2A, R1 and
R2 is used to scale the sensor’s full scale span to 4 V. R2 is
also returned to the buffered .5 V to maintain the 0.5 V zero
offset that was established in the instrumentation amplifier.
Output voltage range is therefore 0.5 to 4.5 V.
Both of these instrumentation amplifier circuits do their
intended job with a relatively straightforward tradeoff between
cost and performance. The circuit of Figure 2 has the usual
cumulative tolerance problem that is associated with
instrumentation amplifiers that have discrete resistors, but it
has a relatively low cost. The integrated instrumentation
amplifier in Figure 3 solves this problem with precision
trimmed film resistors and also provides superior input offset
performance. Component cost, however, is significantly
higher.
SENSOR SPECIFIC INTERFACE AMPLIFIER
A low cost interface designed specifically for pressure
sensors improves upon the instrumentation amplifier in Figure
2. Shown in Figure 4, it uses one quad op amp and several
resistors to amplify and level shift the sensor’s output. Most of
the amplification is done in U1A which is configured as a
differential amplifier. It is isolated from the sensor’s positive
output by U1B. The purpose of U1B is to prevent feedback
current that flows through R5 and R6 from flowing into the
sensor. At zero pressure the voltage from pin 2 to pin 4 on the
sensor is 0 V. For example, let’s say that the common mode
voltage on these pins is 4.0 V. The zero pressure output
voltage at pin 1 of U1A is then 4.0 V, since any other voltage
would be coupled back to pin 2 via R6 and create a non–zero
bias across U1A’s differential inputs. This 4.0 V zero pressure
DC output voltage is then level translated to the desired zero
pressure offset voltage (VOFFSET) by U1C and U1D.
F
Freescale Semiconductor, Inc.
n
.