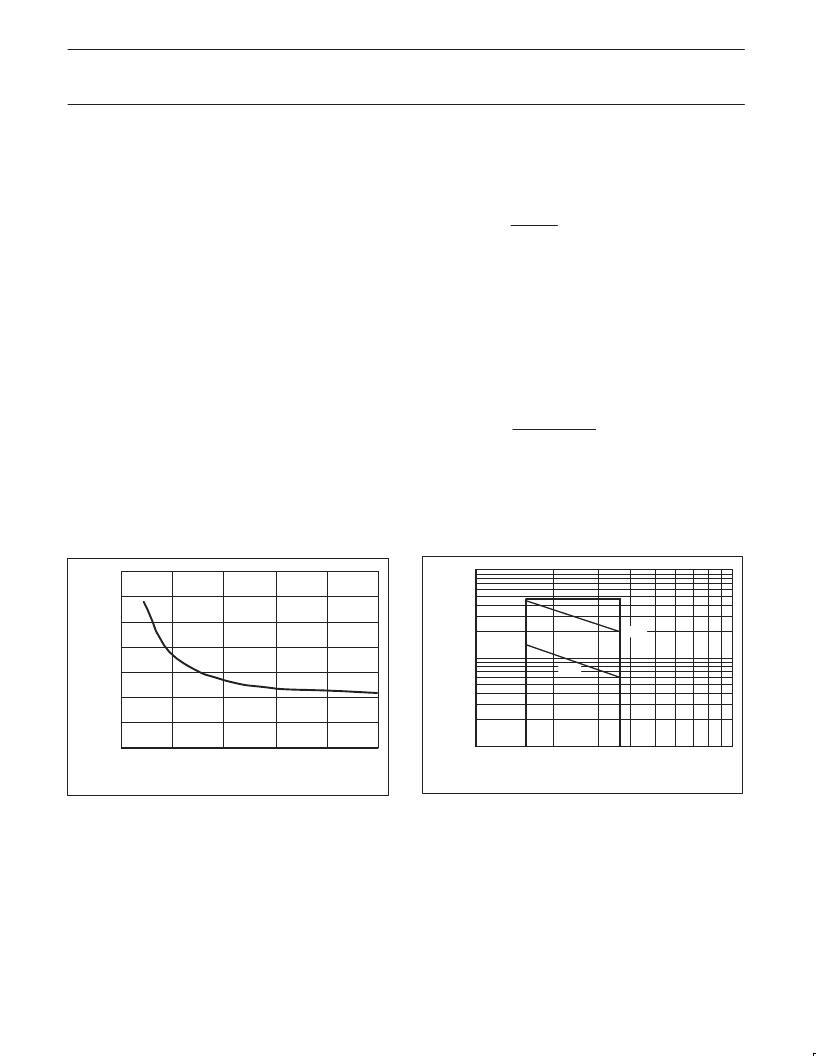
Philips Semiconductors
Product data
NE57814
DDR memory termination regulator with
standby mode and enhanced efficiency
2003 Apr 03
12
THERMAL DESIGN
Designing the thermal system for the NE57814 is important for its
reliable operation. The NE57814 will be operating at an average
power level less than the maximum rating of the part. In a typical
DDR terminator system the average power dissipation is between
0.8 and 1.5 watts. It is important to make sure that this average
power dissipation is less than the power capability of the package.
The terminator heatsink must be designed to accommodate the
average power as a steady state condition and be able to withstand
momentary periods of increased dissipation, say from 1–2 seconds.
For the single-supply application, the power dissipated by the
terminator can be calculated:
P
D
I
DD
V
TT
Watts
Eqn. (1)
The thermal resistance of a surface mount package is given as
R
th(j-a)
(thermal resistance from the junction to air). JESD51-7
specifies a 4-layer PCB (2oz/1oz/1oz/2oz copper) that is 4 inches on
each side. This is probably the best (or lowest thermal resistance)
one will see in any application. Most applications cannot afford the
PCB area to create this situation, but the thermal performance of a
multi-layer PCB will still provide a significant heat sinking effect. The
actual thermal resistance will be higher than the 38.5
°
C/W given for
the 4-layer JEDEC PCB.
Figure 14 shows what thermal resistance one can expect for heat
sinking PCB areas less than the JEDEC specification. The
resistance can be decreased by using a double-sided PCB with
some plated through holes (vias) to help transfer the heat to the
bottom side. The thermal resistance decreases by about 3–4
°
C/W
for a double-sided board with vias.
T
°
SL01888
LENGTH OF SIDE OF 2 oz. COPPER AREA (mm)
0
20
40
60
80
100
55
50
45
40
35
30
25
60
Figure 14. Thermal resistance versus PCB area.
After the power is estimated, the minimum PCB area can be
determined by calculating the worst-case thermal resistance and
referring to Figure 8 to determine the PCB area. This is done by:
R
thj-a)(min)
T
j
T
amb
P
Eqn. (2)
Where:
T
j
is the maximum desired junction temperature.
T
amb
is the highest expected local ambient temperature.
P is the estimated average power
The junction temperature should be kept below the
over-temperature cutoff threshold temperature (+140
°
C ) in normal
operation.
Using the power dissipation formula above, the highest ambient
temperature, 1.5 watts power dissipation (used only as an example)
and a junction temperature of +125
°
C, calculate the maximum
thermal resistance as follows:
R
thj–a)(min)
140
O
C
70
O
C
1.5W
47
O
C W
Eqn. (3)
Looking at Figure 15, a minimum PCB island area of 225 mm
2
(15 mm length and width) is required at this power dissipation. Of
course, increasing this area will allow the NE57814 to operate at
cooler temperatures, enhancing the long-term reliability and allowing
the terminator to better handle any transient output current
demands.
I
D
SL01873
V
DD
(V)
1
2
3
4
5
6
1
0.1
10
DC
0.5 s
7
8
9 10
Figure 15. Safe operating area of the NE57814.