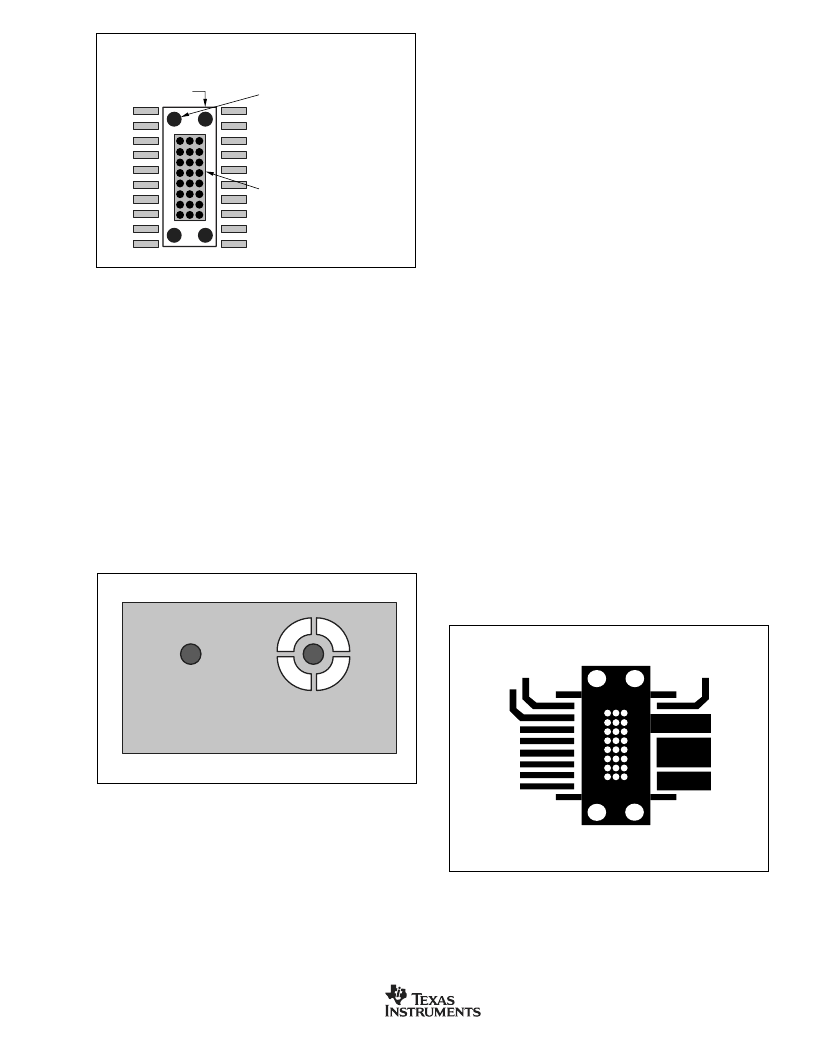
OPA569
SBOS264
19
www.ti.com
5. Connect all holes, including those within the thermal pad
area and outside the pad area, to the internal ground
plane or other internal copper plane for single supply
applications, and V
–
for split-supply applications.
6. When laying out these holes to the ground plane, do not
use the typical web or spoke via connection methodology,
as shown in Figure 17. Web connections have a high
thermal resistance connection that is useful for slowing
the heat transfer during soldering operations. This makes
soldering the vias that have ground plane connections
easier. However, in this application, low thermal resis-
tance is desired for the most efficient heat transfer.
Therefore, the holes under the PowerPAD package should
make their connection to the internal ground plane with a
complete connection around the entire circumference of
the plated-through hole.
FIGURE 16. 20-Pin DWP PowerPAD PCB Etch and Via Pattern.
Web or Spoke Via
NOT RECOMMENDED
Solid Via
RECOMMENDED
FIGURE 17. Via Connection.
Thermal Land
299 mils x 510 mils
Minimum Area (7.59mm x 12.95mm)
(Copper)
OPTIONAL:
Additional 4 vias outside of
thermal pad area but under
the package
(Via diameter = 25 mils)
REQUIRED:
Thermal pad area: 140 mils x 176 mils
(3.56mm x 4.47mm) with 24 vias
(Via diameter = 13 mils)
9. With these preparatory steps in place, the PowerPAD IC
is simply placed in position and run through the solder
reflow operation as any standard surface-mount compo-
nent. This results in a part that is properly installed.
For detailed information on the PowerPAD package including
thermal modeling considerations and repair procedures,
please see Technical Brief SLMA002,
“
PowerPAD Thermally
Enhanced Package,
”
located at www.ti.com.
LAYOUT GUIDELINES
The OPA569 is a power amplifier that requires proper layout
for best performance. Figure 18 shows an example of proper
layout.
Keep power-supply leads as short as possible. This will keep
inductance low and resistive losses at a minimum. A mini-
mum of 18 gauge wire thickness is recommended for power-
supply leads. The wire length should be less than 8 inches.
Proper power-supply bypassing with low ESR capacitors is
essential to achieve good performance. A parallel combina-
tion of small (around 100nF) ceramic and bigger (47
μ
F)
tantalum bypass capacitors will provide low impedance over
a wide frequency range. Bypass capacitors should be placed
as close as practical to the power-supply pins of the OPA569.
PCB traces conducting high currents, such as from output to
load or from the power-supply connector to the power-supply
pins of the OPA569 should be kept as wide and short as
possible.
The twenty-four holes in the landing pattern for the OPA569
are for the thermal vias that connect the PowerPAD of the
OPA569 to the heatsink area on the PCB. The additional four
larger vias further enhance the heat conduction into the
heatsink area. All traces conducting high currents are very
wide for lowest inductance and minimal resistive losses. Note
that the negative supply (
–
V) pin on the OPA569 can be
connected through the PowerPAD to allow for maximum
trace width for high current paths.
7. The top-side solder mask should leave the terminals of the
pad connections and the thermal pad area exposed. The
thermal pad area should leave the 13 mil holes exposed.
The larger holes outside the thermal pad area should be
covered with solder mask.
8. Apply solder paste to the exposed thermal pad area and
all of the package terminals.
V
–
Parellel
Out 1
Current
Limit Set
Current Limit Flag
–
In
+In
Thermal Flag
Enable
Parallel Out 2
I
MONITOR
V
–
V
OUT
V+
Pin 1
NOTE: Avoid routing Current
Limit Set and Current Limit
Flag traces closely in parallel.
FIGURE 18. 20-Pin DWP PowerPAD PCB Etch and Via
Pattern.