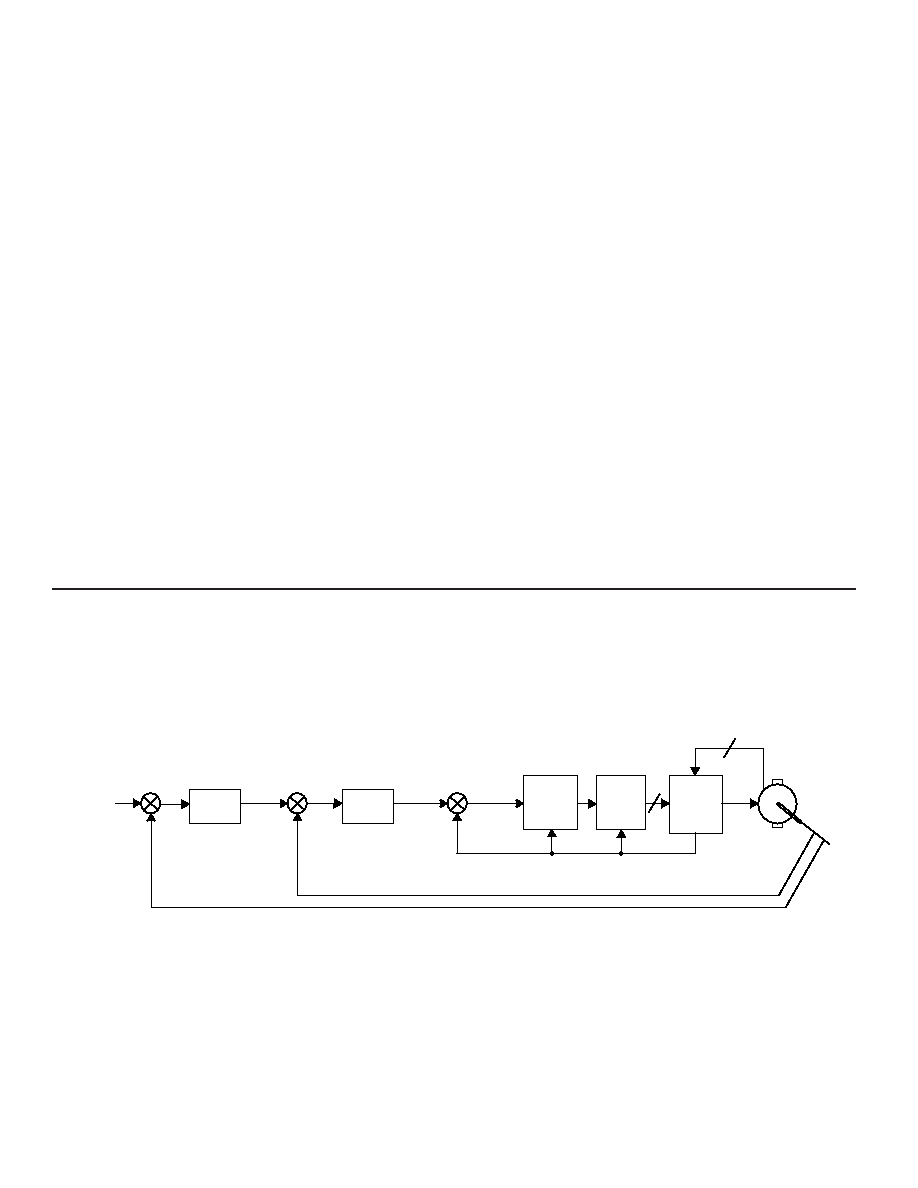
10
POSITION
COMMAND
POSITION
ERROR
POSITION
AMP
VELOCITY
COMMAND
VELOCITY
ERROR
VELOCITY
AMP
TORQUE
COMMAND
TORQUE
ERROR
CURRENT
ERROR
AMP
PWM
PW-82351
3-PHASE
DRIVE
HALL SIGNALS
3-PHASE
MOTOR
3
6
TORQUE LOOP
VELOCITY LOOP
POSITION LOOP
+
-
+
-
+
-
FIGURE 7. TYPICAL POSITION AND VELOCITY CONTROL LOOP
OVER VOLTAGE LOW, OV ADJ, OV FLAG OUT
The over voltage (OV) feature monitors the VCC supply voltage
to RTN to detect a bus pump-up condition and prevent it from
damaging the drive. When an over voltage condition (Vmax) is
detected, the OV switch is turned on allowing current to bleed
off the supply and the OV flag OUT is set high (logic 1).
An external bleed resistor is placed between VCC and the
OVER VOLTAGE LOW terminal. The OV switch will turn off and
the OV FLAG OUT will return low (logic 0) once the VCC volt-
age is below the Vmin trip point.
The PW-82351 is set internally for a trip voltage of 400 V. To
set a different trip voltage an external resistor is connected
from the OV ADJ terminal to either RTN or VCC (see FIGURES
9a and 9b). This resistor should be selected for the voltage
Vmax you want the OV switch to turn on.
ISOLATION BARRIER
The isolation barrier maintains electrical isolation between the
control side ground and power side return. All signals are iso-
lated and the power section is completely floating from the con-
trol section.
HEATSINK MOUNTING
The PW-82351 must be mounted on a heatsink to remove the
power dissipated inside the unit when driving the load. The
PW-82351 should have a thermally conductive interface, like a
thermal joint compound between the heatsink and motor drive
module. The base plate of the PW-82351 is not electrically
connected to the internal circuitry and does not require an iso-
lated thermal interface. The PW-82351 should be mounted
with #6 self-locking screws and torqued to specifications in
TABLE 2.
ASSEMBLY CLEANING INSTRUCTIONS
The PW-82351 is encapsulated with silicones and organic coat-
ings which cannot be exposed to solvents for extended periods of
time. Exposure to solvent vapors during vapor degreasing should
be limited to the minimum process times required for flux residue
removal. The maximum exposure to solvent vapors should be
limited to 10 minutes. The PW-82351 cannot be submerged in
solvent fluids. If cleaning of assembled modules in a fluid is antic-
ipated, DDC must be contacted before any modules are exposed
to the fluid in order to mantain the product warranty.