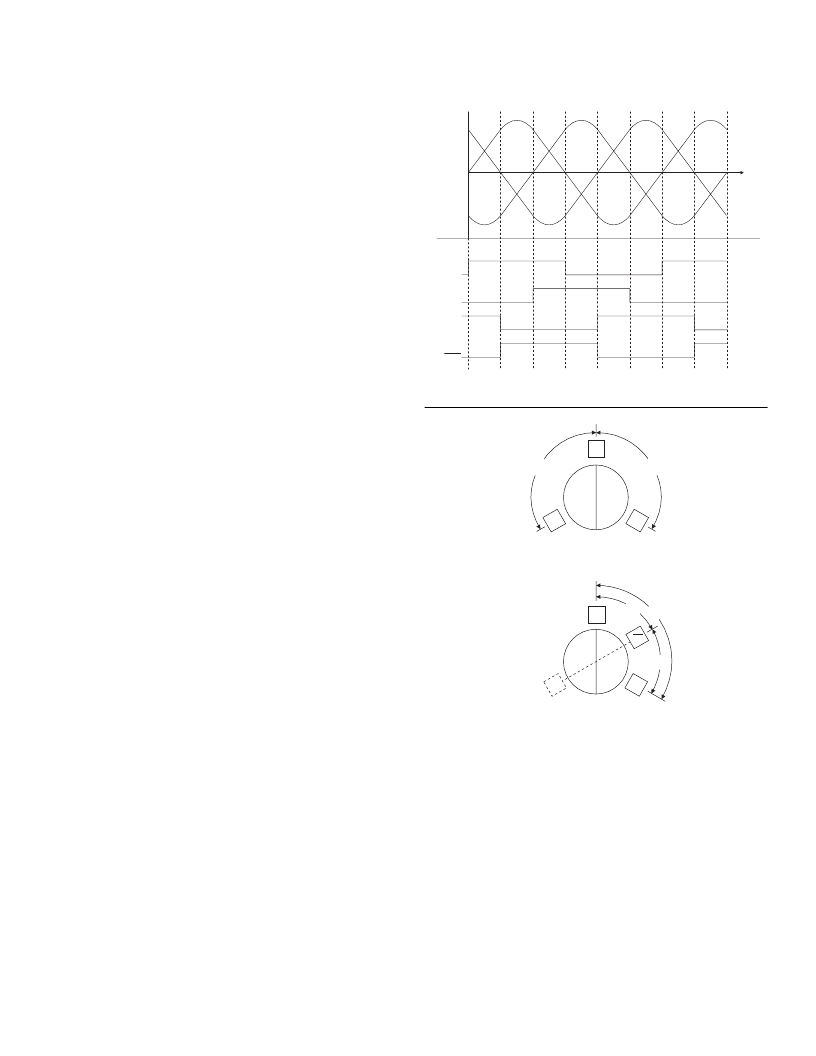
15
Data Device Corporation
www.ddc-web.com
PW-8X010P6/8X030P6/8X075P6
D-02/03-0
APPLICATIONS
POSITION OR VELOCITY CONTROL USING DSP
FIGURE 11 shows an example of position and/or velocity control
hook-up with inner torque loop using the Digital Signal
Processor (DSP) for motor control. Using software, the DSP can
be implemented with one of several motor control algorithms
such as FOC (Field Oriented Control) with SVM (Space Vector
Modulation).
TORQUE CONTROL USING UC-2625 MOTOR CON-
TROLLER
FIGURE 12 shows an example of torque control loop with regen-
erative clamp protection using a UC2625, two PW-84010P6,
PW-84030P6 or PW-84075P6 modules, and one PW-85010P6,
PW-85030P6 or PW-85075P6 module. The two PW-84010P6,
PW-84030P6 or PW-84075P6 modules ( bridge with current
sense) sense the current in motor phase B and C. V
IRSENSE
pins
on each of the PW-84010P6, PW-84030P6 or PW-84075P6
modules are connected to the decommuntation circuit (shown in
FIGURE 14) to produce bipolar output voltage that is compared
to the torque commanded input to produce an error signal. The
UC2625 uses this error signal to regulate the output current (or
torque) by controlling the duty cycle of the output transistors.The
gain of the current decommuntation circuit shown in FIGURE 14
has been selected to accommodate a ±10V command input volt-
age.
For the case when a resolver is available instead of Hall-effect
devices, the circuit shown in FIGURE 13 converts the resolver
(sin and cos) signals to Hall signals which can be used to com-
mutate the output transistors.
HALL SIGNAL COMMUTATION
The hall signals HAB, HBC, HCA are logic signals from the
motor Hall-effect sensors. The UC2625 uses a phasing conven-
tion referred to as 120 degree spacing; that is, the output of HAB
is in phase with motor back EMF voltage VAB, the output of HBC
is in phase with motor back EMF voltage VBC, and the output of
HCA is in phase with motor back EMF voltage VCA. Logic "1"
(or HIGH ) is defined by an input greater than 2.4Vdc or an open
circuit to the controller; Logic "0"(or LOW) is defined as any Hall
voltage input less than 0.8Vdc.
The UC2625 will operate with Hall phasing of 60° or 120° elec-
trical spacing. If 60° commutation is used, then the output of
HCA must be inverted as shown in FIGURES 9 and 10. In FIG-
URE 9 the Hall sensor outputs are shown with the corresponding
back EMF voltage they are in phase with.
HALL-EFFECT SENSOR PHASING vs.
MOTOR BACK EMF FOR CW ROTATION (120
°
Commutations)
300
°
0
°
60
°
120
°
180
°
V
AB
V
BC
ROTATING
CW
240
°
300
°
360
°
/0
°
60
°
V
CA
CW
HAB
HBC
HCA
HCA
with V
AB
with V
BC
with V
CA
with V
AC
(60)
FIGURE 9. HALL PHASING
S
HCA
HAB
120
°
N
HBC
120
°
N
HCA
120
°
REMOTE POSITION SENSOR (HALL) SPACING FOR
120 DEGREE COMMUTATION
60
°
60
°
REMOTE POSITION SENSOR (HALL) SPACING FOR
60 DEGREE COMMUTATION
S
HAB
HBC
HCA
FIGURE 10. HALL SENSOR SPACING