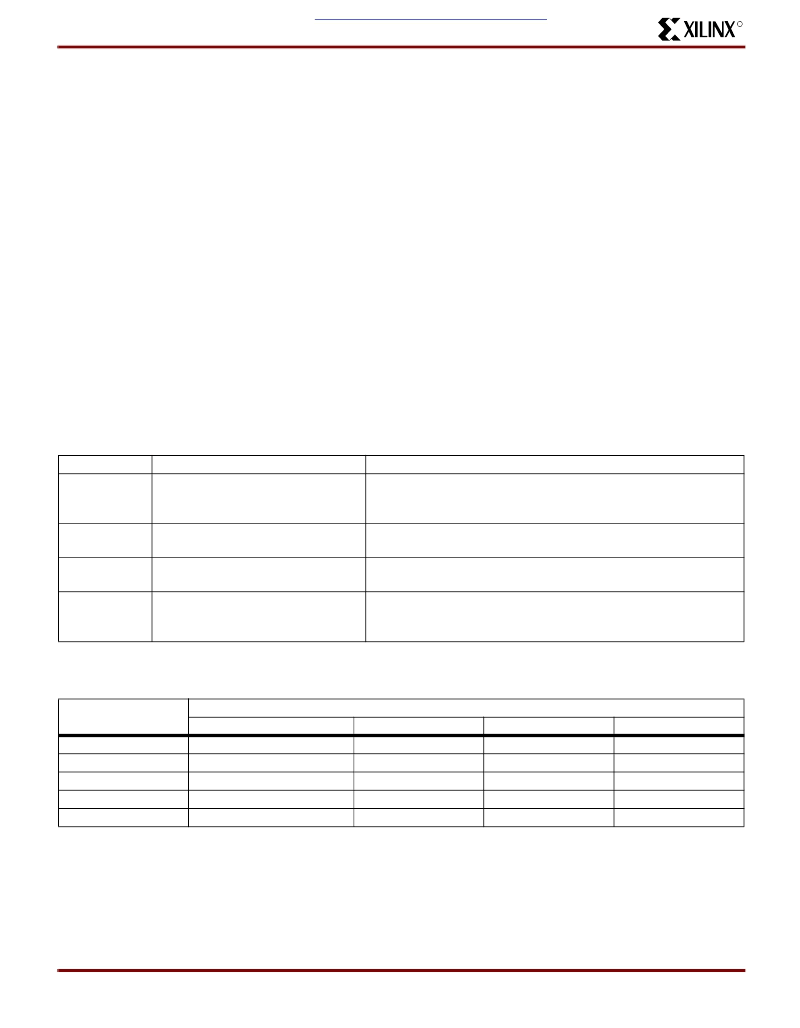
R
XCR3128: 128 Macrocell CPLD
7
www.xilinx.com
1-800-255-7778
DS034 (v1.3) October 9, 2000
This product has been discontinued. Please see
for details.XCR3128, the TAP Port includes four of the five pins (refer
to
Table 2
) described in the JTAG specification: TCK, TMS,
TDI, and TDO. The fifth signal defined by the JTAG specifi-
cation is TRST* (Test Reset). TRST* is considered an
optional signal, since it is not actually required to perform
BST or ISP. The Xilinx XCR3128 saves an I/O pin for gen-
eral purpose use by not implementing the optional TRST*
signal in the JTAG interface. Instead, the Xilinx XCR3128
supports the test reset functionality through the use of its
power up reset circuit, which is included in all Xilinx CPLDs.
The pins associated with the power up reset circuit should
connect to an external pull-up resistor to keep the JTAG
signals from floating when they are not being used.
In the Xilinx XCR3128, the four mandatory JTAG pins each
require a unique, dedicated pin on the device. However, if
JTAG and ISP are not desired in the end-application, these
pins may instead be used as additional general I/O pins.
The decision as to whether these pins are used for
JTAG/ISP or as general I/O is made when the JEDEC file is
generated. If the use of JTAG/ISP is selected, the dedi-
cated pins are not available for general purpose use. How-
ever, unlike competing CPLD
’
s, the Xilinx XCR3128 does
allow the macrocell logic associated with these dedicated
pins to be used as buried logic even when JTAG/ISP is
selected.
Table 3
defines the dedicated pins used by the
four mandatory JTAG signals for each of the XCR3128
package types.
The JTAG specifications defines two sets of commands to
support boundary-scan testing: high-level commands and
low-level commands. High-level commands are executed
via board test software on an a user test station such as
automated test equipment, a PC, or an engineering work-
station (EWS). Each high-level command comprises a
sequence of low level commands. These low-level com-
mands are executed within the component under test, and
therefore must be implemented as part of the TAP Control-
ler design. The set of low-level boundary-scan commands
implemented in the Xilinx XCR3128 is defined in
Table 4
.
By supporting this set of low-level commands, the
XCR3128 allows execution of all high-level boundary-scan
commands.
Table 2: JTAG Pin Description
PIN
TCK
NAME
DESCRIPTION
Test Clock Output
Clock pin to shift the serial data and instructions in and out of the
TDI and TDO pins, respectively. TCK is also used to clock the TAP
Controller state machine.
Serial input pin selects the JTAG instruction mode. TMS should be
driven high during user mode operation.
Serial input pin for instructions and test data. Data is shifted in on
the rising edge of TCK.
Serial output pin for instructions and test data. Data is shifted out on
the falling edge of TCK. The signal is tri-stated if data is not being
shifted out of the device.
TMS
Test Mode Select
TDI
Test Data Input
TDO
Test Data Output
Table 3: XCR3128 JTAG Pinout by Package Type
Device
XCR3128
84-pin PLCC
100-pin PQFP
100-pin VQFP
128-pin TQFP
160-pin PQFP
(Pin Number / Macrocell #)
TMS
23 / 48 (C15)
17 / 48 (C15)
15 / 48 (C15)
21 / 48 (C15)
22 / 48 (C15)
TCK
TDI
TDO
62 / 96 (F15)
64 / 96 (F15)
62 / 96 (F15)
82 / 96 (F15)
99 / 96 (F15)
14 / 32 (B15)
6 / 32 (B15)
4 / 32 (B15)
8 / 32 (B15)
9 / 32 (B15)
71 / 112 (G15)
75 / 112 (G15)
73 / 112 (G15)
95 / 112 (G15)
112/ 112 (G15)