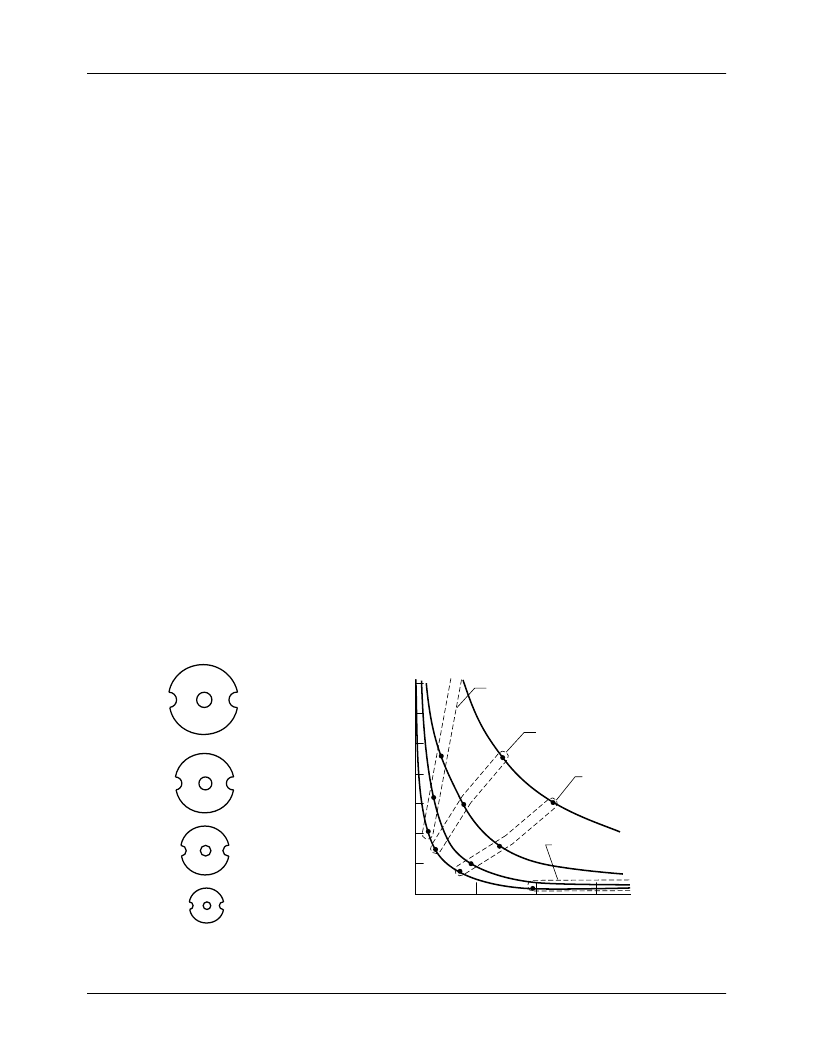
PRODUCT SPECIFICATION
RC4190
20
As the applied magnetizing force increases, at some point
the permeability will start decreasing, and therefore the
amount of magnetic flux will not increase any further, even
as the magnetizing force increases. The physical reality is
that, at the point where the permeability decreases, the mag-
netic field has realigned all of the magnetic domains in the
core material. Once all of the domains have been aligned the
core will then carry no more flux than just air; it becomes as
if there were no core at all. This phenomenon is called satu-
ration. Because the inductance value, L, is dependent on the
amount of flux, core saturation will cause the value of L to
decrease dramatically, in turn causing excessive and possibly
destructive inductor current.
Pot Cores for RC4190
Pot core inductors are best suited for the RC4190
micropower switching regulator for several reasons:
1.
They are available in a wide range of sizes. RC
4190
applications are usually low power with relatively low
peak currents (less than 500mA). A small inexpensive
pot core can be chosen to meet the circuit requirements.
2.
Pot cores are easily mounted.
They can be bolted
directly to the PC card adjacent to the regulator IC.
3.
Pot cores can be easily air-gapped
. The length of the
gap is simply adjusted using different washer thick-
nesses. Cores are also available with predetermined air
gaps.
4.
Electromagnetic interference (EMI) is kept to a
minimum.
The completely enclosed design of pot core
reduces stray electromagnetic radiation—an important
consideration of the regulator circuit is built on a PC
card with other circuitry.
Core Size
Question:
Is core size selected according to load power
Not quite. Core size is dependent on the amount of energy
stored, not on load power. Raising the operating frequency
allows smaller cores and windings. Reduction of the size of
the magnetics is the main reason switching regulator design
tends toward higher operating frequency. Designs with the
RC4190 should use 75kHz as a maximum running fre-
quency, because the turn off delay of the power transistor
and stray capacitive coupling begin to interfere. Most appli-
cations are in the 10 to 50kHz range, for efficiency and EMI
reasons.
The peak inductor current (I
MAX
) must reach a high enough
value to meet the load current drain. If the operating
frequency is increased, and simultaneously the inductor
value is decreased, then the core can be made smaller. For a
given core size and winding, an increase in air gap spacing
(an air gap is a break in the material in the magnetic path,
like a section broken off a doughnut) will cause the induc-
tance to decrease and I
MAX
(the usable peak current before
saturation) to increase.
The curves shown in Figure 26 are typical of the ferrite
manufacturer's power HF material, such as Siemens N27 or
Stackpole 24B, which are usually offered in standard
millimeter sizes including the sizes shown.
Use of the Design Aid Graph (Figure 27)
1.
From the application requirement, determine the induc-
tor value (L) and the required peak current (I
MAX
).
2.
Observe the curves of the design aid graph and deter-
mine the smallest core that meets both the L and I
requirements.
Figure 27. Inductor Design Aid
6
Air Gap = 0.012"
Air Gap = 0.006"
Air Gap = 0.02"
No Air Gap
#1
#2
#3
#4
1 mH
2 mH
3 mH
3A
2A
1A
0
I
M
Inductor Value (Henries)
*Includes safety margin (25%) to ensure nonsaturation
#1
#2
#3
#4
22X 13 mm
24 Gauge
70 Turns
DC
= 0.5
18X 11 mm
26 Gauge
70 Turns
DC
= 0.7
14X 8 mm
28 Gauge
60 Turns
DC
= 0.6
11X 7 mm
30 Gauge
50 Turns
DC
= 1