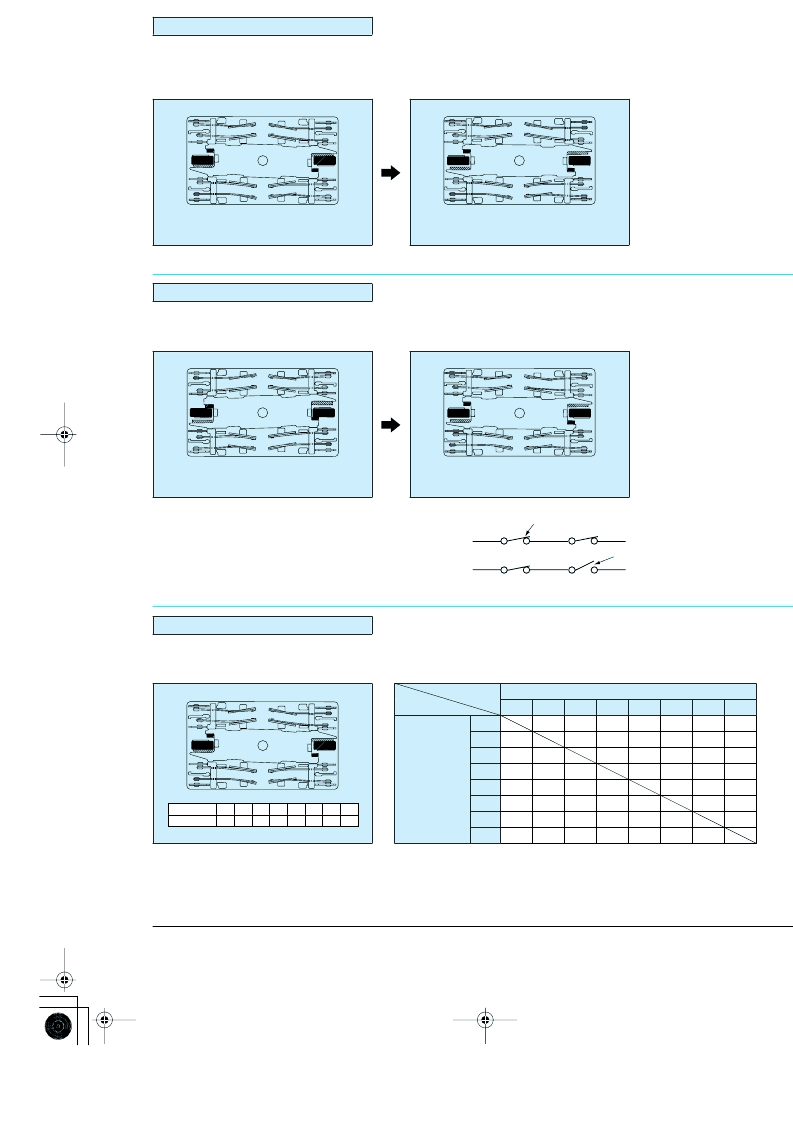
SF relays work to maintain a normal operating state even when the contact welding occur by overloading or short-circuit
If the internal contacts (No. 2, 3, 6, and 7) weld of 4a4b type, the armature becomes non-operational and the contact gaps of each of
the four form
“
a
”
contacts are maintained at greater than 0.5 mm
.020 inch
. Reliable isolation is thus ensured. The 2a2b type operates
in the same way.
Internal Contacts Weld
If the No. 2 contact welds.
Each of the four form
“
a
”
contacts (No. 1, 3, 5,
and 7) maintains a gap of greater than 0.5 mm
.020 inch
.
No.1
No.2
No.3
No.4
No.8
No.7
No.6
No.5
Non-energized
No.1
No.2
No.3
No.4
No.8
No.7
No.6
No.5
Energized (when no. 2 contact is welded)
If the external contacts (No. 1, 4, 5, and 8) weld of 4a4b type, gaps of greater than 0.5 mm
.020 inch
are maintained between adjacent
contacts and the other contacts return by an non-energized.
External Contacts Weld
If the No. 1 contact welds.
The adjacent No. 2 contact maintains a gap of
greater than 0.5 mm
.020 inch
. The other
contacts, because the coil is not energized,
return to their normal return state; each of
form
“
a
”
contacts (No. 3, 5, and 7) maintains a
contact gap of greater than 0.5 mm
each of the form
“
b
”
contacts (No. 4, 6, and 8)
return to a closed state.
;
If external connections are made in series.
Even if one of the contacts welds, the other contacts
operate independently and the contact gaps are
maintained at greater than 0.5 mm
.020 inch
.
No.1
No.2
No.3
No.4
No.8
No.7
No.6
No.5
Energized
No.1
No.2
No.3
No.4
No.8
No.7
No.6
No.5
Non-energized (when no. 1 contact is welded)
Energized
Contact gap
min 0.5 mm
.020 inch
Weld
Non-energized
The table below shows the state of the other contacts. In case of form
“
a
”
contact weld the coil applied voltage is 0 V.
In case of form
“
b
”
contact weld the coil applied voltage is nominal.
Contact Operation Table
No.1
No.2
No.3
No.4
No.8
No.7
No.6
No.5
Contact No.
Terminal No.
No.1 No.2 No.3 No.4
20
–
19 12
–
11 8
–
7 16
–
15
No.5 No.6 No.7 No.8
13
–
14 5
–
6
9
–
10 17
–
18
Note: Contact gaps are shown at the initial state.
If the contact transfer is caused by load switching, it is necessary to check the actual loading.
Contact No.
State of other contacts
3
4
>0.5
≠
>0.5
>0.5
>0.5
>0.5
≠
>0.5
>0.5
≠
>0.5
>0.5: contact gap
is kept at min. 0.5
mm
.020 inch
≠
: contact closed
Empty cells: either
closed or open
Contact No.
1
2
5
6
≠
7
8
≠
Welded
contact
No.
1
2
3
4
5
6
7
8
>0.5
>0.5
>0.5
>0.5
>0.5
>0.5
>0.5
>0.5
≠
>0.5
>0.5
>0.5
>0.5
>0.5
≠
≠
≠
≠
>0.5
>0.5
>0.5
>0.5
>0.5
>0.5
>0.5
>0.5
>0.5
>0.5
≠
≠
>0.5