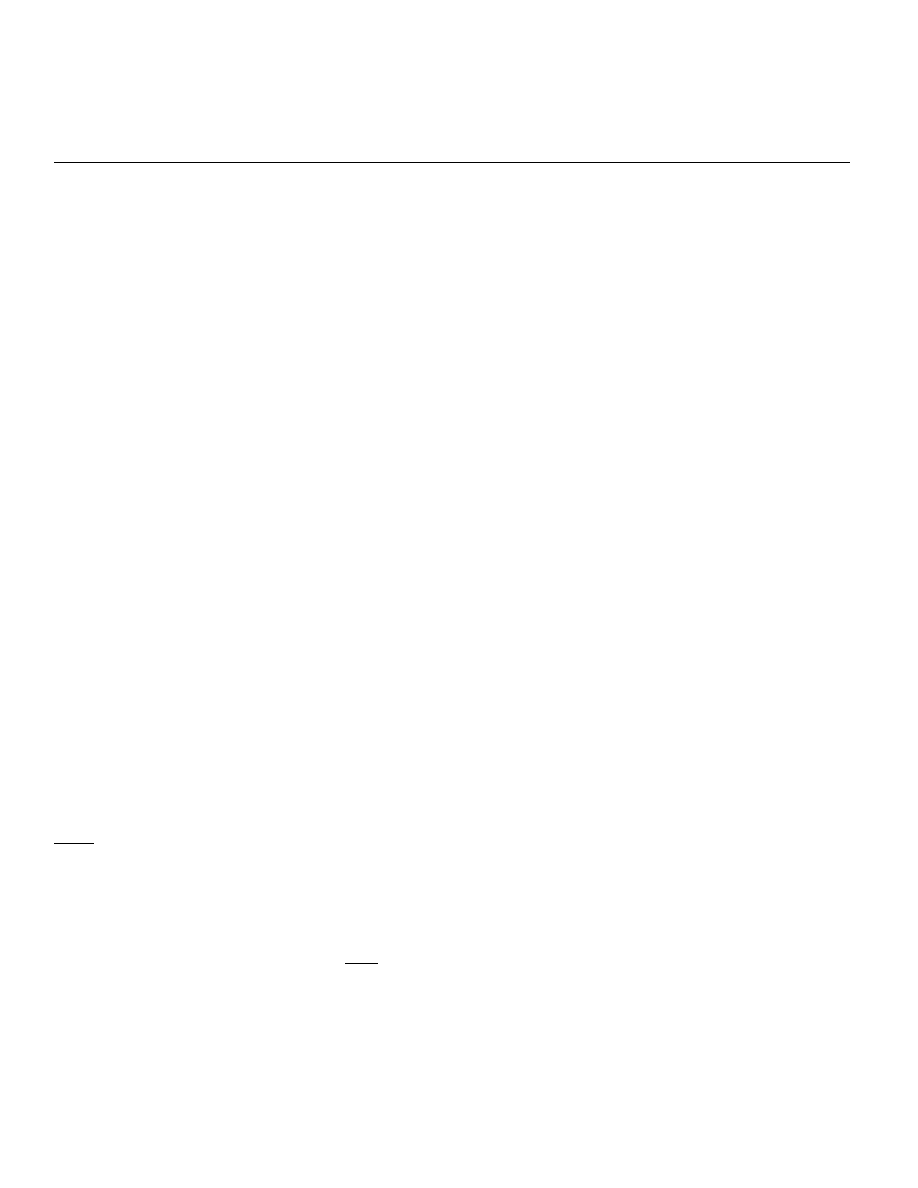
4
TC643-1 9/29/97
TC643
INTEGRATED FAN / MOTOR DRIVER
2001 Microchip Technology Inc.
DS21445A
DETAILED DESCRIPTION
The TC643 is the first IC which integrates all the power
and analog signal-processing circuitry for fan management
into a single, easy-to-use device. Only three logic signals
interface the TC643 to its host. A number of value-added
features can now be implemented by the system designer
with minimal impact on cost, space, and design time. The
advantages of a fan management system built around the
TC643 may include:
(1) High Integration: higher reliability, lower cost, less
design effort.
(2) PWM Speed Control: better efficiency, reduced
operating temperatures, wide speed-control range,
less acoustic noise, longer fan life, speed control
of low-voltage fans without stalling.
(3) Fan Feedback and Diagnostics: system-level fault-
tolerance, device-level fault protection, intelligent
fault prediction, real-time fan performance charac-
terization and trending.
Power Driver
The DRV input is a standard CMOS/TTL compatible
logic input. The on-chip NPN power transistor is switched
on when this input is high. The output features a high
efficiency NPN power transistor ( low VCE(SAT) ) for cooler
operation. This permits driving even large motors with a DIP
or SOIC packaged device. Normally, this input is driven with
a digital PWM waveform to control fan speed. The FAN
terminal will stand off 15V. The ground return for the power
driver, GNDFAN, is separate from the IC’s power supply
return, GND, and the motor’s power supply can be indepen-
dent of the IC’s. See the
Electrical Characteristics section
for more details.
ILMT
The motor current through the TC643, IFAN, is internally
limited to a preset value, ILIMIT. If IFAN exceeds ILIMIT, this
open collector output will go low. IFAN will be clamped at
ILIMIT. This serves as an indication of a stalled or shorted
motor, or other fault. Typically this output is connected to an
interrupt input of the host microcontroller. ILMT may go
active momentarily during motor start-up. The digital control
circuitry should ignore this indication until the motor has time
to start. See the
Electrical Characteristics and Applications
sections for more details.
RPM
During normal fan operation, commutation occurs as
each pole of the fan is energized. This causes brief interrup-
tions in the fan current (See Figure 1). The TC643 detects
these perturbations in fan current by monitoring the current
through the on-chip drive transistor. Internal signal condi-
tioning circuitry derives a pulse-train representing the fan-
pole crossings. RPM outputs a high-going pulse each time
a fan pole-crossing is detected. See the
Electrical Charac-
teristics section for detailed timing information. The host
microcontroller or digital control logic can derive the motor
rpm by timing the period of the waveform present on RPM.
If commutation occurs while the power driver is off, a pulse
will not be detected. A careful study of the motor rpm range
and PWM frequency of interest is called for when designing
with the TC643. See the
Applications section for more
details.
CEXT
A 0.002
F (typical) capacitor between this pin and
ground serves as part of the signal conditioning circuitry
which derives the RPM output. It is effectively part of a
differentiator designed to sense the commutation of the fan.
These commutation pulses are translated to logic-level and
squared-up to produce the RPM signal. The characteristics
of this capacitor are not particularly critical. A 0.002
F, 5.0V
ceramic type is suggested.
APPLICATIONS INFORMATION
Designing with the TC643 involves a number of issues.
This section provides simple methodologies and guidelines
to deal with each one. With reasonable care and thoughtful-
ness, it is a straightforward procedure to design a complete
fan management system that is efficient, reliable, and “fea-
ture-rich”.
Applying the TC643 generally involves . . .
(1) Matching a fan (or motor) with the desired perfor -
mance to the TC643.
(2) Selecting a PWM frequency and duty-cycle range
and considering its impact on RPM determination.
(3) Architecting the microcontroller hardware and soft-
ware (or other control scheme) to drive the TC643
and take full advantage of its fan management
capabilities.