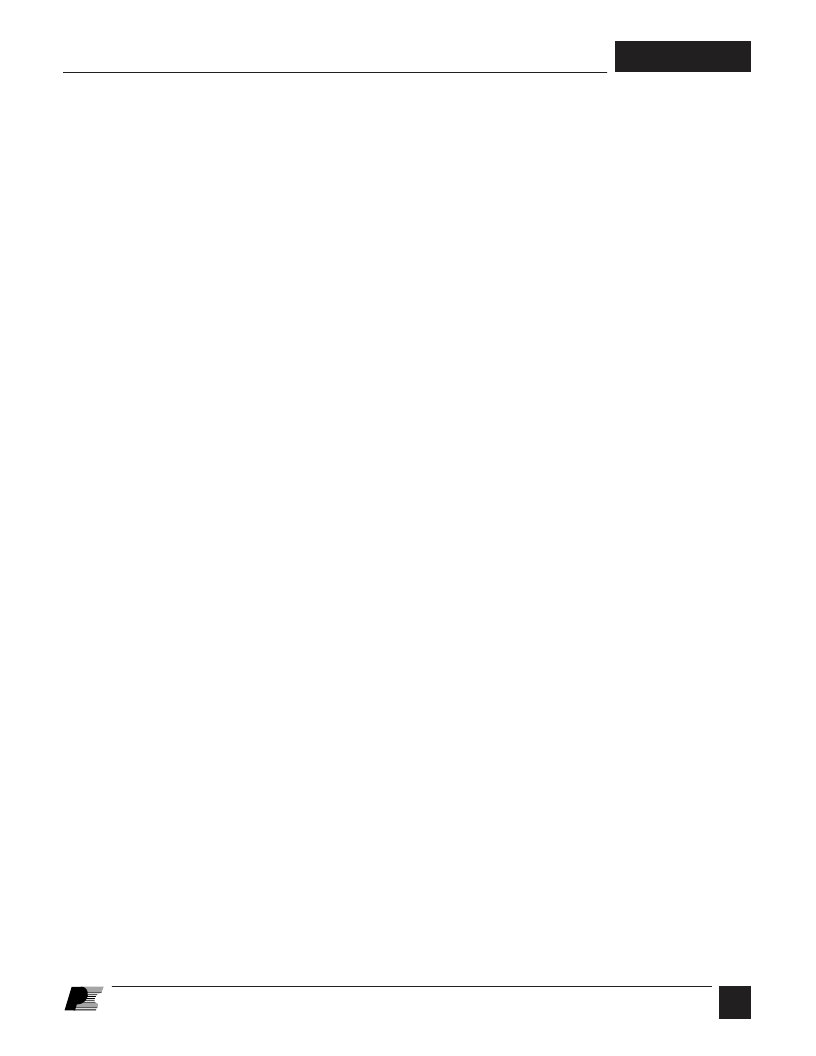
11
TNY264/266-268
C
4/03
2. A secondary output of 5 V with a Schottky rectifier diode.
3. Assumed efficiency of 77% (TNY267 & TNY268), 75%
(TNY266) and 73% (TNY264).
4. The parts are board mounted with SOURCE pins soldered
to sufficient area of copper to keep the die temperature at or
below 100
°
C.
In addition to the thermal environment (sealed enclosure,
ventilated, open frame, etc.), the maximum power capability of
TinySwitch-II
in a given application depends on transformer
core size and design (continuous or discontinuous), efficiency,
minimum specified input voltage, input storage capacitance,
output voltage, output diode forward drop, etc., and can be
different from the values shown in Table 1.
Audible Noise
The
TinySwitch-II
practically eliminates any transformer audio
noise using simple ordinary varnished transformer construction.
No gluing of the cores is needed. The audio noise reduction is
accomplished by the
TinySwitch-II
controller reducing the
current limit in discrete steps as the load is reduced. This
minimizes the flux density in the transformer when switching
at audio frequencies.
Worst Case EMI & Efficiency Measurement
Since identical
TinySwitch-II
supplies may operate at several
different frequencies under the same load and line conditions,
care must be taken to ensure that measurements are made under
worst case conditions. When measuring efficiency or EMI
verify that the
TinySwitch-II
is operating at maximum frequency
and that measurements are made at both low and high line input
voltages to ensure the worst case result is obtained.
Layout
Single Point Grounding
Use a single point ground connection at the SOURCE pin for
the BYPASS pin capacitor and the Input Filter Capacitor
(see Figure 17).
Primary Loop Area
The area of the primary loop that connects the input filter
capacitor, transformer primary and
TinySwitch-II
together
should be kept as small as possible.
Primary Clamp Circuit
A clamp is used to limit peak voltage on the DRAIN pin at turn-
off. This can be achieved by using an RCD clamp (as shown in
Figure 14). A Zener and diode clamp (200 V) across the
primary or a single 550 V Zener clamp from DRAIN to SOURCE
can also be used. In all cases care should be taken to minimize
the circuit path from the clamp components to the transformer
and
TinySwitch-II
.
Thermal Considerations
Copper underneath the
TinySwitch-II
acts not only as a single
point ground, but also as a heatsink. The hatched areas shown
in Figure 17 should be maximized for good heat sinking of
TinySwitch-II
and
the same applies to the output diode.
EN/UV pin
If a line under-voltage detect resistor is used then the resistor
should be mounted as close as possible to the EN/UV pin to
minimize noise pick up.
The voltage rating of a resistor should be considered for the
under-voltage detect (Figure 15: R2, R3) resistors. For 1/4 W
resistors, the voltage rating is typically 200 V continuous,
whereas for 1/2 W resistors the rating is typically 400 V
continuous.
Y-Capacitor
The placement of the Y-capacitor should be directly from the
primary bulk capacitor positive rail to the common/return
terminal on the secondary side. Such placement will maximize
the EMI benefit of the Y-capacitor and avoid problems in
common-mode surge testing.
Optocoupler
It is important to maintain the minimum circuit path from the
optocoupler transistor to the
TinySwitch-II
EN/UV and
SOURCE pins to minimize noise coupling.
The EN/UV pin connection to the optocoupler should be kept
to an absolute minimum (less than 12.7 mm or 0.5 in.), and
this connection should be kept away from the DRAIN pin
(minimum of 5.1 mm or 0.2 in.).
Output Diode
For best performance, the area of the loop connecting the
secondary winding, the Output Diode and the Output Filter
Capacitor, should be minimized. See Figure 17 for optimized
layout. In addition, sufficient copper area should be provided
at the anode and cathode terminals of the diode for adequate
heatsinking.
Input and Output Filter Capacitors
There are constrictions in the traces connected to the input and
output filter capacitors. These constrictions are present for two
reasons. The first is to force all the high frequency currents to
flow through the capacitor (if the trace were wide then it could
flow around the capacitor). Secondly, the constrictions minimize
the heat transferred from the
TinySwitch-II
to the input filter
capacitor and from the secondary diode to the output filter
capacitor. The common/return (the negative output terminal in
Figure 17) terminal of the output filter capacitor should be
connected with a short, low impedance path to the secondary
winding. In addition, the common/return output connection