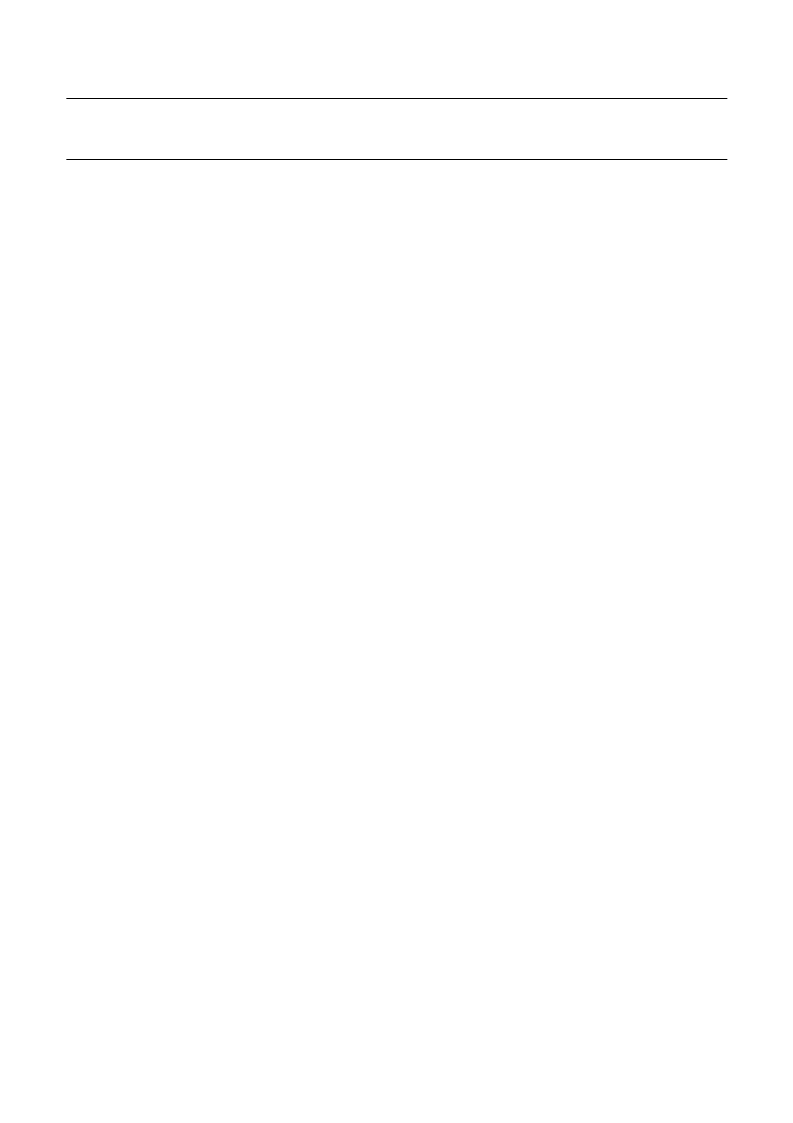
2003 Jun 03
40
Philips Semiconductors
Preliminary specification
High speed advanced analog DVD signal
processor and laser supply
TZA1035HL
11.3
Energy saving
Bit PWRON can be used to bring the TZA1035HL into
STANDBY mode reducing the supply current to
approximately 0.5 mA.
11.4
Initial DC and gain setting strategy
11.4.1
E
LECTRICAL OFFSET FROM PICK
-
UP
It is useful to compensate for electrical offset, especially
with pick-ups that give a low output signal. It is possible to
compensate for each individual servo channel. Due to
internal circuitry, the TZA1035HL servo channels can
handle only signals positive with respect to the reference
input OPUREF. Therefore the potentially negative offset
from the pick-up must first be cancelled. The LF
OFFS
DAC
can be programmed to do this, and will apply this to all six
channels at the same time. The LF
OFFS
DAC can be set
to 0, 5, 10 or 15 mV.
As a second step, the offset between each channel can be
compensated by connecting the DACs to each individual
DAC (C
OFFSA
to C
OFFSD
, R
OFFSE
and R
OFFSF
). These
DACs can be programmed between 0 and 20 mV with
approximately 1.25 mVresolution.WheretheLF
OFFS
DAC
increases the outputs signal level, the individual DACs
decrease the output signal. In this way the output signal
can be set very close to zero. The range of DACs, LF
OFFS
,
C
OFFS
and R
OFFS
can be tripled with control
bit SERVOOS.
The output current of servo channel A is calculated by:
In case the laser is switched off, the term (V
A
V
OPUREF
)
represents the electrical offset from the pick-up.
The procedure to cancel the offset is:
1.
Activate the pick-up and switch off the laser.
2.
Set LF
OFFS
to its maximum value.
3.
Measure the output currents off all relevant servo
outputs.
4.
Ifall outputsrepresent asignal >5 mV equivalent input
voltage, decrease V
LFOFFS
then repeat step 3; if all
outputs represent a signal <5 mV equivalent input
voltage, go to step 5.
5.
Measure each output and increase C
OFFS
until the
output current is close enough to zero.
This procedure needs only to be done once, or after a
longer time when temperature may have changed the
pick-up offset.
The test pin OCENTRAL can be useful to follow this
procedure. This pin can be programmed to output a copy
of the signal OA to OD (see register 12).
11.4.2
G
AIN SETTING SERVO
The servo gain has to be chosen dependant on the
reflectivity of the disc. So this needs to be done each time
when a new disc is inserted in the mechanism. A trial and
error procedure should find the optimal setting. Gain can
be set in 3 dB steps.
11.4.3
DC
LEVEL IN
RF
PATH
Once the gains in the servo path have been set, the
average DC level at the inputs can be calculated from the
value of the servo output signals:
Where I
Ox
is the average value of the output currents at
pins OA to OD.
This value is a good estimate to use initially to set the
RF DC compensation, V
RFOFFS
. The range and resolution
of the RF
OFFS
DACs are scaled with the programmed gain
of G
1
.
In cases where a DC coupling between TZA1035HL and
the decoder is made, a fine tuning of the RF DC
compensation can be done during play. The zero-crossing
level of the data-eye pattern can be used to judge the
correct DC compensation level.
11.4.4
G
AIN SETTING
RF
PATH
The choice of RF gain is determined by the modulation of
the disc, therefore the modulation needs to be checked
each time a new disc is inserted in the mechanism. A trial
and error procedure should be sufficient to find the
optimum setting. For optimum use of the dynamic range:
Use G
3
for fine tuning and AGC, so initially this should
be set in the range 0 to 6 dB to leave an additional gain
of 6 dB free to use during disc defects
Use G
1
and G
2
to set the gain, increase G
1
first,
when G
1
has reached its maximum then G
2
should be
increased
G
2
shows better noise performance in 12 and 24 dB
settings than in 6 and 18 dB setting
A similar procedure can be followed for RFSUM.
I
OA
V
V
–
(
)
V
14 k
COFFSA
----------------------------------------------------------------------------V
]
A
LFC
×
=
V
I
I
V
LFOFFS
A
LFC
V
COFFSx
+
(
)
–
-----------------------------------14 k
=