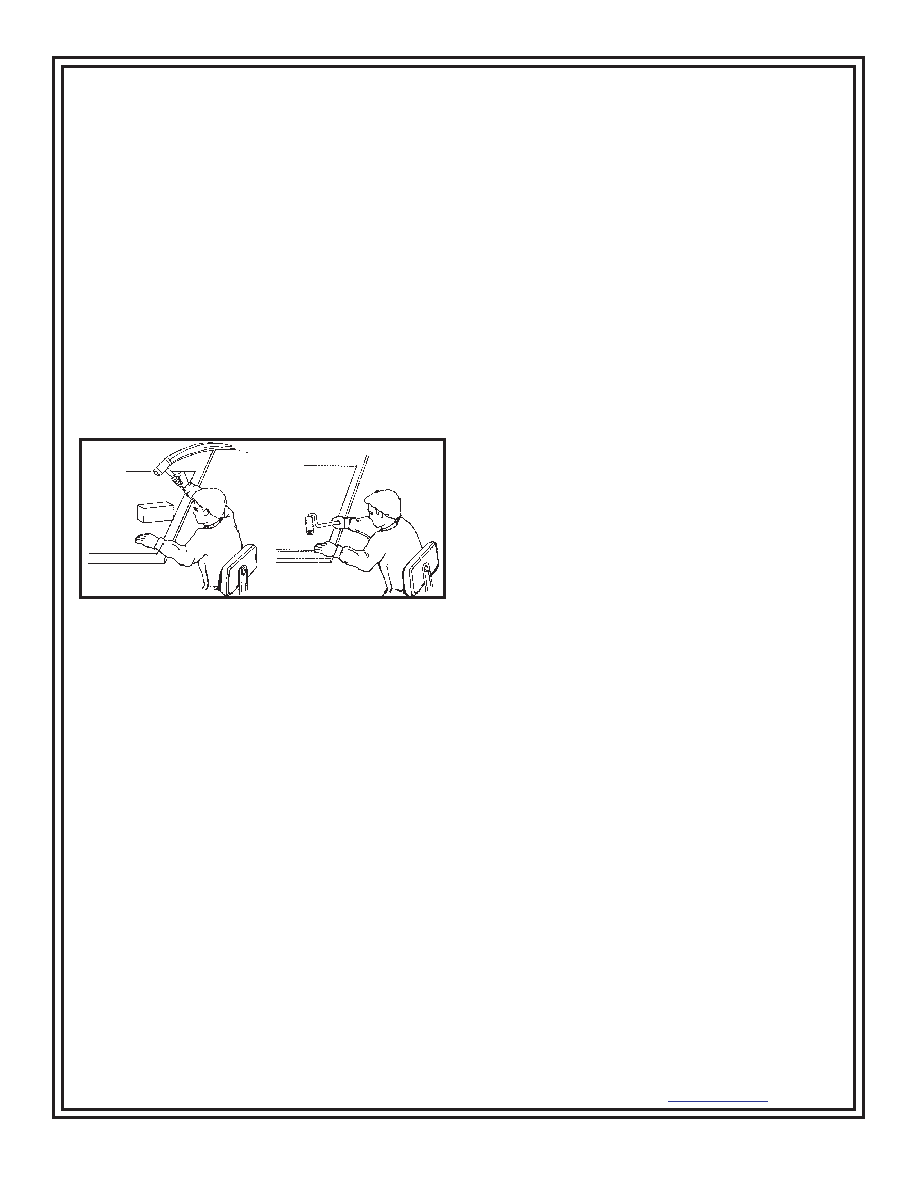
TB-2091 Page 2 of 8
5. Slowly remove strips of wood taking care to keep the
Micastat
in position. The Micastat should fall into
position.
6. Push the laminate down with even hand pressure.
7. If the Micastat
falls out of position, squirt solvent (Desco
recommends the use of ST102 solvent from Pionite)
between the two surfaces and gently lift the Micastat
sheet up. Wait a minimum of 4 hours before reapplying
another coat of adhesive, solvent must evaporate totally.
Apply another coat of adhesive to both surfaces and
reposition.
8. When Micastat
is in the correct position, seal the bond
with a rubber “J” roller or a carpeted block and rubber
mallet. Use either roller or block and mallet in a pattern
that forces any air bubbles out from underneath
laminate. If Micastat
sheet is oversized, sheet can now
be trimmed with a router. After trimming, edges should
be filed for a smooth splinter free edge.
Figure 4. Wooden block and rubber mallet and “J” roller
technique.
Once installed, Micastat
must be grounded to ensure
proper charge dissipation. Refer to general grounding
guidelines on this page.
Postforming Application
When the universal grade Micastat
is exposed to a
temperature of 325 degrees Fahrenheit it will soften
momentarily, allowing a straight line bend to be made. This
bend should be made quickly and uniformly and have a
radius equal to or greater than 5/8". The chemical change
that takes place in this process cannot be reversed;
Micastat
cannot be reheated. Proper postforming
machinery and close attention to details such as time and
temperature are essential for best results. Preinstallation
storage conditions are critical to postforming performance.
For detailed postforming information please refer to
NEMA publication LD 3-1995 or follow these general
directions.
1. Micastat
should be conditioned at 70°F to 75°F and 45-
50 percent relative humidity for 48 hours prior to
postforming. Recommended postforming machinery
includes Midwest Automation and Evans Rototorque.
2. The radiused edge of substrate must be smooth,
rounded, and free of irregularities and loose particles.
3. Lead-in cracks may be minimized by ensuring a smooth
cut on the edge of the laminate.
4. Always bond Micastat to a suitable substrate such as
medium to high density fiberboard, or particleboard. It
should not be glued directly to plaster walls, gypsum
wallboard, concrete, or metals.
5. Recommended adhesives include solvent or water-
based contact cement, white glue (PVA), epoxy, and hot
melt glue. Consult your adhesive supplier for specific
application requirements.
6. The use of a backing sheet is recommended to minimize
warpage. The thickness of the backing sheet should be
relatively equal to the thickness of the decorative
laminate on the face of the assembly.
7. The decorative surface to be formed should be heated to
a temperature of 325°F to 375°F (165°C to 190°C).
8. Heat the Micastat
“wings” only, to 325°F to 375°F
(165°C to 190°C) with a Chomelux heater held 2" to 2.5"
from the surface. Tempilaq
liquid temperature indicator
or equivalent should be used to determine the
temperature.
9. The desired heat-up rate of 325°F (165°C) should be
one second for every 0.001" of thickness (i.e., 30
seconds for .028", 38 seconds for .038".
10. Forming should be accomplished within 5 seconds of
achieving proper surface temperature.
11. Heat up rates of laminate are affected by thickness,
color, and finish. Temperatures should be verified by
temperature-indicating wax (Tempilaq
).
12. Let the Micastat
laminate cool for five to ten minutes
under pressure.
Fabrication Tips
1. All saw blades and router bits used for cutting should be
carbide tipped. Feed rate should be slow and tool speed
should be high. To minimize the development of surface
scratches caused by router bits, lubricating the laminate
edge with a wax stick is recommended prior to tooling.
DESCO WEST - 3651 Walnut Avenue, Chino, CA 91710 (909) 627-8178 Fax (909) 627-7449
2009 DESCO INDUSTRIES, INC.
Employee Owned