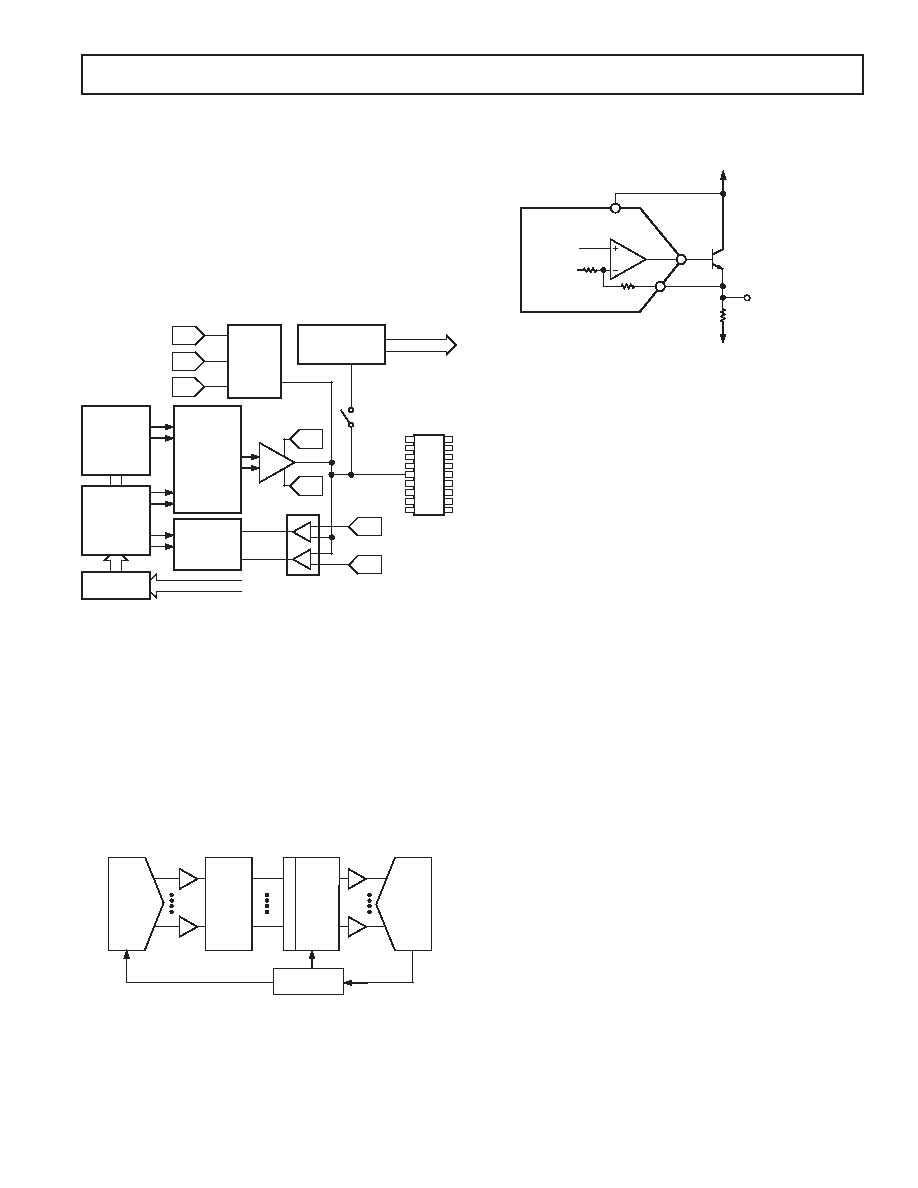
REV. B
AD5516
–13–
APPLICATION CIRCUITS
The AD5516 is suited for use in many applications, such as level
setting, optical, industrial systems, and automatic test applications.
In level setting and servo applications where a fine-tune adjust is
required, the Mode 2 function increases resolution. The following
figures show the AD5516 used in some potential applications.
AD5516 in a Typical ATE System
The AD5516 is ideally suited for the level setting function in
automatic test equipment. A number of DACs are required to
control pin drivers, comparators, active loads, parametric mea-
surement units, and signal timing. Figure 10 shows the AD5516
in such a system.
DAC
STORED
DATA AND
INHIBIT
PATTERN
PERIOD
GENERATION
AND
DELAY
TIMING
DACs
FORMATTER
COMPARE
REGISTER
SYSTEM BUS
DAC
ACTIVE
LOAD
PARAMETRIC
MEASUREMENT
UNIT
SYSTEM BUS
DAC
COMPARATOR
DUT
DRIVER
Figure 10. AD5516 in an ATE System
AD5516 in an Optical Network Control Loop
The AD5516 can be used in optical network control applica-
tions that require a large number of DACs to perform a control
and measurement function. In the example shown in Figure 11,
the outputs of the AD5516 are fed into amplifiers and used to
control actuators that determine the position of MEMS mirrors
in an optical switch. The exact position of each mirror is measured
and the readings are multiplexed into an 8-channel, 14-bit ADC
(AD7865). The increment and decrement modes of the DACs are
useful in this application as they allow 14-bit resolution.
The control loop is driven by an ADSP-2106x, a 32-bit
SHARC
DSP.
AD5516
0
15
MEMS
MIRROR
ARRAY
0
15
S
E
N
S
O
R
S
ADG609
2
0
7
AD7865
AD8644
2
ADSP-2106x
Figure 11. AD5516 in an Optical Control Loop
AD5516 in a High Current Circuit
Access to the feedback loop of the AD5516 amplifier provides
greater flexibility, e.g., it enables the user to configure the device
as a digitally programmable current source or increase the out-
put drive current. See Figure 12. Note that VDD must be chosen
so that the DAC output has enough headroom to drive the
BJT ~ 0.7 V above the maximum output voltage.
AD5516-1
VDD
VDAC
VOUT0
RFB0
R
Vx = – 2.5V TO +2.5V
VDD
VSS
X
Figure 12. AD5516 in a High Current Circuit
Note it is not intended that the RFB nodes be used to alter
amplifier gain or for force/sense in remote sense applications.
POWER SUPPLY DECOUPLING
In any circuit where accuracy is important, careful consideration
of the power supply and ground return layout helps to ensure the
rated performance. The printed circuit board on which the AD5516
is mounted should be designed so that the analog and digital
sections are separated and confined to certain areas of the board. If
the AD5516 is in a system where multiple devices require an
AGND-to-DGND connection, the connection should be made at
one point only. The star ground point should be established as
close as possible to the device. For supplies with multiple pins
(AVCC1, AVCC2), it is recommended to tie those pins together. The
AD5516 should have ample supply bypassing of 10
mF in parallel
with 0.1
mF on each supply located as closely to the package as
possible, ideally right up against the device. The 10
mF capacitors
are the tantalum bead type. The 0.1
mF capacitor should have low
effective series resistance (ESR) and effective series inductance
(ESI), like the common ceramic types that provide a low impedance
path to ground at high frequencies, to handle transient currents
due to internal logic switching.
The power supply lines of the AD5516 should use as large a trace
as possible to provide low impedance paths and reduce the effects
of glitches on the power supply line. Fast switching signals such
as clocks should be shielded with digital ground to avoid radiating
noise to other parts of the board, and should never be run near
the reference inputs. A ground line routed between the DIN and
SCLK lines will help reduce crosstalk between them (not required
on a multilayer board as there will be a separate ground plane, but
separating the lines will help). It is essential to minimize noise
on REFIN.
Avoid crossover of digital and analog signals. Traces on opposite
sides of the board should run at right angles to each other. This
reduces the effects of feedthrough through the board. A micro-
strip technique is by far the best, but not always possible with a
double-sided board. In this technique, the component side of
the board is dedicated to ground plane while signal traces are
placed on the solder side.
As is the case for all thin packages, care must be taken to avoid
flexing the package and to avoid a point load on the surface of
the package during the assembly process.