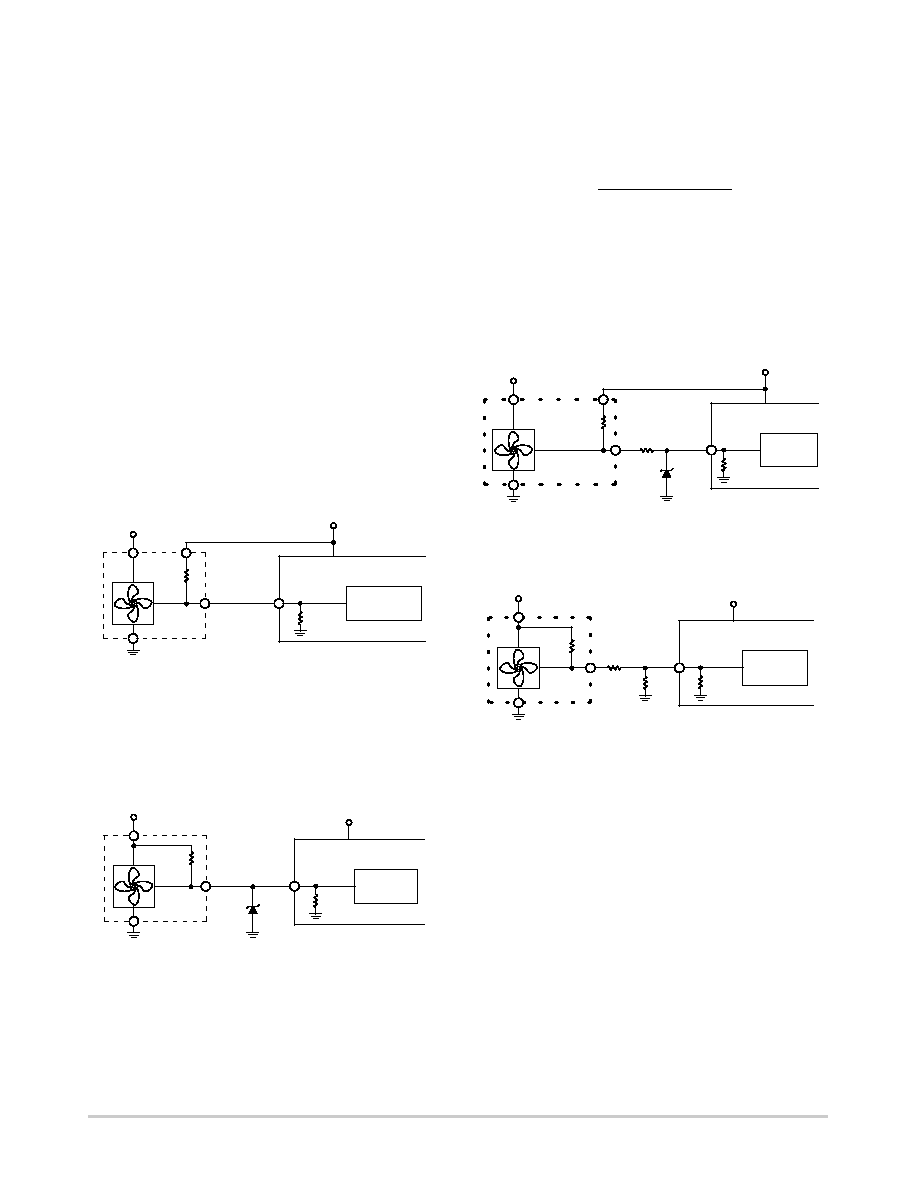
ADM1024
http://onsemi.com
17
voltage dividers and analog components, will provide best
performance but is not mandatory.
The power supply bypass, the parallel combination of
10
mF (electrolytic or tantalum) and 0.1 mF (ceramic) bypass
capacitors connected between Pin 9 and ground, should also
be located as close as possible to the ADM1024.
Fan Inputs
Pins 5 and 6 may be configured as analog inputs or fan
speed inputs by programming Bits 0 and 1 of the Channel
Mode Register. The power-on default for these bits is all
zeros, which makes Pins 5 and 6 fan inputs.
Signal conditioning in the ADM1024 accommodates the
slow rise and fall times typical of fan tachometer outputs.
The maximum input signal range is 0 to VCC. In the event
that these inputs are supplied from fan outputs that exceed
0 V to 6.5 V, either resistive attenuation of the fan signal or
diode clamping must be included to keep inputs within an
acceptable range.
Figure
25 to Figure
28 show circuits for most common fan
tachometer outputs.
If the fan tachometer output has a resistive pullup to VCC,
it can be directly connected to the fan input, as shown in
Figure 25. Fan with Tach Pullup to +VCC
160k
PULLUP
4.7k
TYP
12V
VCC
FAN SPEED
COUNTER
FAN1 OR
FAN2
TACH
OUTPUT
W
If the fan output has a resistive pullup to 12 V (or other
voltage greater than 6.5 V), the fan output can be clamped
with a Zener diode, as shown in Figure
26. The Zener
voltage should be chosen so it is greater than VIH but less
than 6.5 V, allowing for the voltage tolerance of the Zener.
A value of between 3.0 V and 5.0 V is suitable.
Figure 26. Fan with Tach. Pullup to Voltage >6.5 V
(e.g., 12 V) Clamped with Zener Diode
*CHOOSE ZD1 VOLTAGE APPROXIMATELY 0.8 y VCC.
12V
VCC
FAN SPEED
COUNTER
FAN1 OR
FAN2
TACH
OUTPUT
ZD1*
ZENER
160k
PULLUP
4.7k
TYP
W
If the fan has a strong pullup (less than 1 k
W) to 12 V, or
a totem-pole output, then a series resistor can be added to
limit the Zener current, as shown in Figure
27. Alternatively,
a resistive attenuator may be used, as shown in Figure
28.R1 and R2 should be chosen such that:
(eq. 7)
2.0 V t VPULLUP
R2
RPULLUP ) R1 ) R2
t
t 5.0 V
The fan inputs have an input resistance of nominally
160 k
W to ground, so this should be taken into account when
calculating resistor values.
With a pullup voltage of 12 V and pullup resistor less than
1 k
W, suitable values for R1 and R2 would be 100 kW and
47 k
W. This will give a high input voltage of 3.83 V.
Figure 27. Fan with Strong Tach Pullup to >VCC or
Totem Pole Output, Clamped with Zener and Resistor
*CHOOSE ZD1 VOLTAGE APPROXIMATELY 0.8 y VCC
PULLUP
TOTEMPOLE
12V
VCC
FAN SPEED
COUNTER
FAN1 OR
FAN2
TACH
OUTPUT
ZD1*
ZENER
160kW
TYP <1k OR
W
R1
10kW
Figure 28. Fan with Strong Tach Pullup to > VCC or
Totem Pole Output, Attenuated with R1/R2
*SEE TEXT.
12V
VCC
FAN SPEED
COUNTER
FAN1 OR
FAN2
TACH
OUTPUT
R1*
R2*
160k
<1k W
W
Fan Speed Measurement
The fan counter does not count the fan tachometer output
pulses directly because the fan speed may be less than
1000 rpm and it would take several seconds to accumulate
a reasonably large and accurate count. Instead, the period of
the fan revolution is measured by gating an on-chip
22.5 kHz oscillator into the input of an 8-bit counter for two
periods of the fan tachometer output, as shown in Figure
29;the accumulated count is actually proportional to the fan
tachometer period and inversely proportional to the fan
speed.