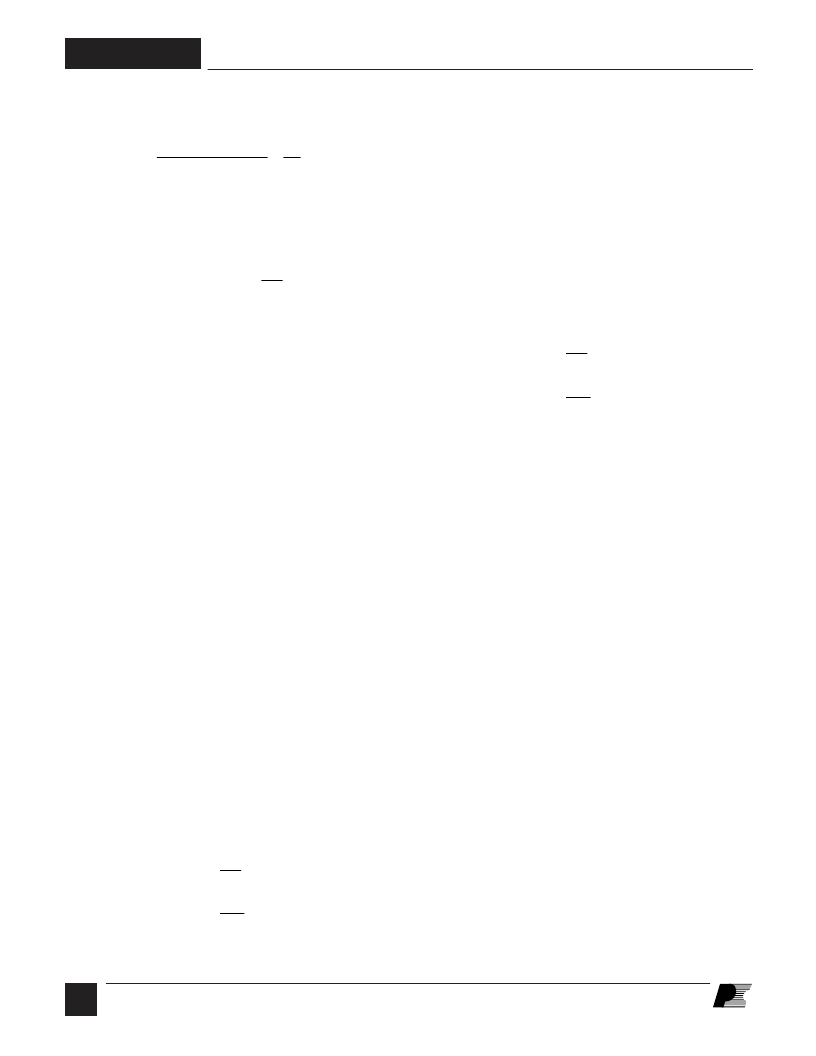
AN-35
6
B
4/03
The secondary diode peak voltage was measured as 0.7 V, the
secondary winding resistance as 0.15
and the cable resistance
as 0.23
. Therefore V
SEC
is defined as:
Voltage V
SEC
allows the exact V
OR
to be calculated:
Resistor R
FB
, a 1%, 0.25 W resistor, converts clamp voltage to
LinkSwitch
bias and control current.
Feedback voltage V
is calculated from V
OR
and the error due
to leakage inductance, V
LEAK
.
The value for V
varies depending on the value of leakage
inductance, the size of the clamp capacitor and the type of clamp
diode selected. For a leakage inductance of 50
μ
H, a value of
5 V is a good initial estimate.
Once a prototype has been constructed, the value of V
FB
can be
found directly, by measuring the voltage across C
at the
power supply peak output power point, using a battery powered
digital voltmeter. These have sufficient common mode rejection
to be unaffected by the switching waveform and provide
accurate results. The voltage measured is V
. By subtracting
V
the value for V
can be determined, useful as an estimate
in future designs. For the design in Figure 3, V
FB
was measured
as 56.7 V, giving V
LEAK
as 5.6 V.
An initial value for R
is calculated from the feedback voltage
V
, the CONTROL pin voltage V
and current I
at the
CC/CV transition point, specified in the
LinkSwitch
data sheet.
cross sectional area A
e
(cm
2
), primary inductance L
(
μ
H), core
effective path length L
e
(cm) and relative permeability
μ
r
:
The gapped effective inductance A
(nH/t
2
), required by the
transformer manufacturer, is calculated from the primary
inductance L
P
(
μ
H) and the number of primary turns N
P
:
Clamp, Bias, Bypass and Feedback
An RCD clamp, formed by R
, C
, and D
(Figure 1), safely limits transformer primary voltage, due to
transformer leakage inductance, to below the
LinkSwitch
internal
MOSFET breakdown voltage BV
each time
LinkSwitch
turns off. Leading-edge voltage spikes (caused by transformer
leakage inductance) are filtered by R
and C
, such that
C
CLAMP
effectively charges to the transformer reflected voltage.
Feedback is derived from the reflected voltage, that approximates
closely the transformer secondary winding output voltage
(V
in Figure 1) multiplied by the transformer turns ratio. Due
to effects of leakage inductance (causing peak charging),
calculated V
may be slightly different from actual voltage
measured across C
. Since
LinkSwitch
is in the upper rail,
reflected voltage information is now relative to the
LinkSwitch
SOURCE pin and independent of the input voltage.
Reflected voltage is directly converted by R
to
LinkSwitch
CONTROL pin current for duty cycle control and bias. The
CONTROL pin capacitor C
provides bypass filtering, control
loop compensation, and the energy storage required during
start-up and auto-restart.
Feedback Resistor (R
FB
)
Clamp and feedback circuit design begins by first considering
reflected voltage. Using the schematic in Figure 3 as an
example. With primary turns N
= 116 and secondary turns
N
= 15 the peak secondary current can be calculated from
Equation 20, where I
PRI(PEAK)
is equal to the
LinkSwitch
typical current limit I
LIM(TYP)
(20)
(22)
A
L
N
LG
P
2
P
=
×
1000
(18)
(19)
L
N
100
A
L
L
μ
g
P
e
P
e
r
=
×
×
×
×
×
0 4
.
10
2
π
(21)
(23)
V
N
N
116
15
51 1
V
V
V
OR
P
S
SEC
=
×
=
×
=
6 61
.
.
V
V
V
FB
OR
LEAK
=
+
I
N
N
116
15
1 96
I
A
SEC PEAK
(
P
S
PRI PEAK
(
)
)
.
.
=
×
=
×
=
0 254
V
V
V
V
(
(
(0 5
1 96
V
V
I
I
R
V
R
V
A
V
A
V
SEC
O
RCABLE
×
DOUT
)
RSEC
O
O
CABLE
DOUT
)
SEC PEAK
(
SEC
=
=
.
5 5
+
+
+
+
+
+
+
+
×
.
0 15
=
.
6 61
×
+
)
×
=
)
.
.
)
0 23
0 7