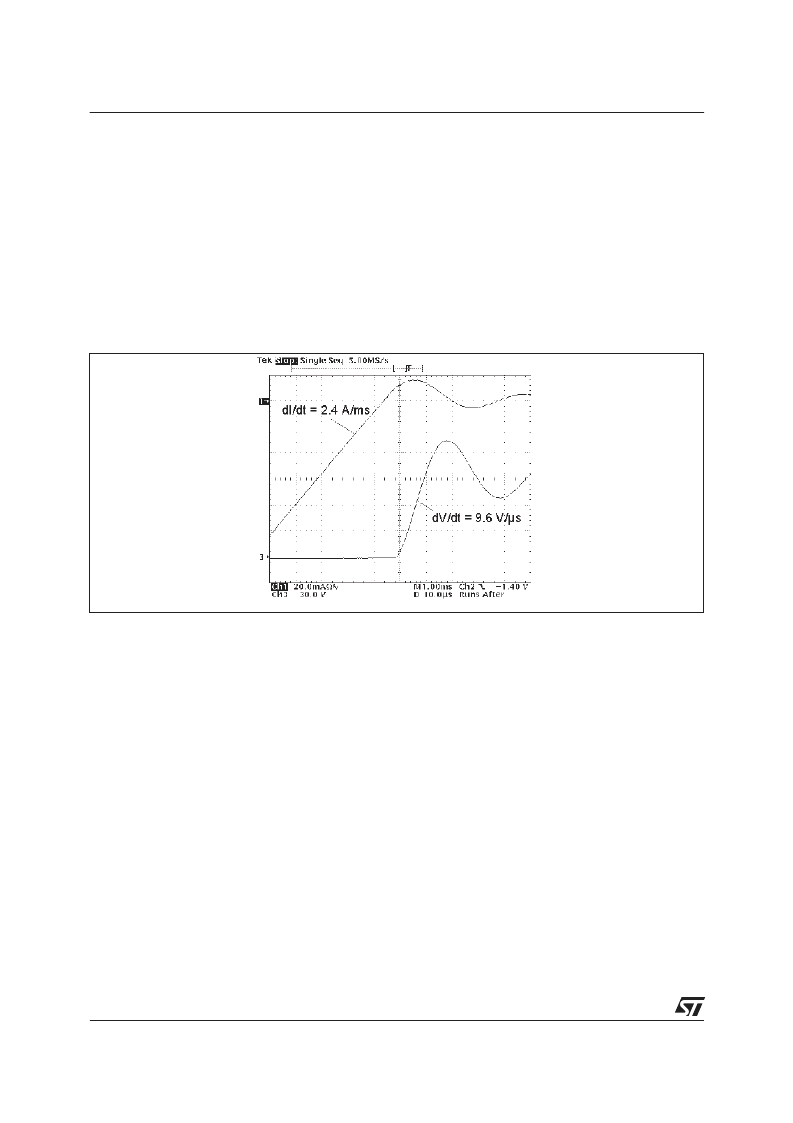
APPLICATION NOTE
4/10
When dealing with the current rating for AC semiconductor switches, the rate of decrease of the current
must also be checked. This constraint will depend on the chosen topology.
The worst case of turn-off stress appears with a compressor without any start capacitor. In this case, the
rise in voltage will not be slowed by the motor capacitor. The higher stress occurs for the “START” winding
(wherethe impedanceis lower than the “RUN”windingone) and when the rotor is stalled.These two condi-
tions yield a higher current and therefore, a higher rate of decrease for the ACST current.
Then, for a stalled 1/5 Horse power compressor, supplied with a 264 V RMS voltage, the dI/dtc and dV/dtc
equals respectively 2.4 A/ms and 9.6 V/μs through the START ACST (cf. Figure 5, measured with
THERM01EVALboard).ThisisfarbelowthemaximumwithstandingforACST6devices,whichis3.5A/ms
with a 15 V/μs rate.
Fig. 5: Turn-off constraint for the worst case scenario
With the two-triac topology, a spurious discharge of the start-capacitor can occur when the start-triac is ac-
cidentallyturnedon.ToreducethedI/dtstressthroughthesiliconswitch,asmallprotectiveinductorcanbe
added in series with this triac.
In order to optimize the solution cost, this inductor can be achieved in Printed Circuit Board (PCB). For ex-
ample, a double-sided inductor with 12 turns of 0.51 mm width track (cf. Figure 6), made on a 35 μm-FR4
PCB, yield to a 5 μH – 1.6 Ohm resistor.
An inductor as described in Figure 6, allows the dI/dt rate to be limited, in case of a spurious firing of the
START ACST when the RUN ACST is already on, below 60 A/μs (start capacitor is charged up to 510 V).
The semiconductor device operation is then well secured.
2.3 Protective inductor