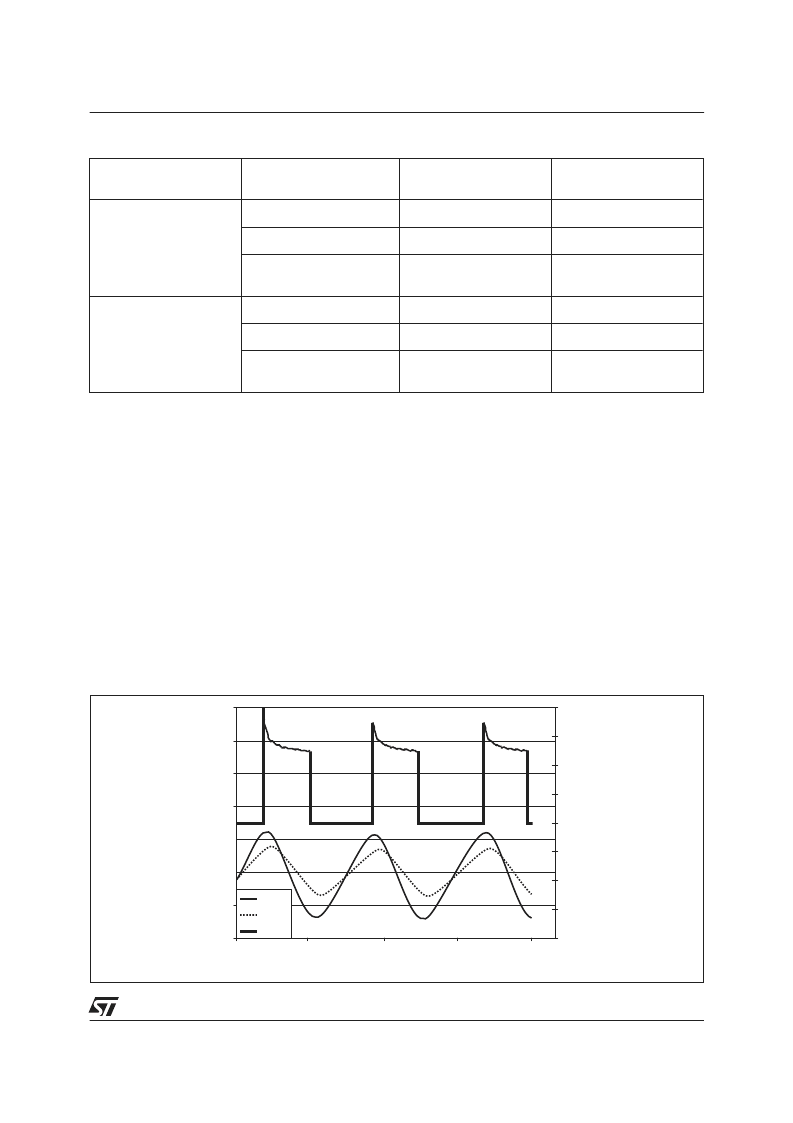
APPLICATION NOTE
9/10
Case 1
(Hyst. Thres. = 5.3°C)
Case 2
(Hyst. Threh. = 4.2°C)
MEASURE
Compressor ON time
12' 50''
9' 10''
Compressor OFF time
16' 20''
15' 10''
Average power during
ON time
136 W
138 W
CALCULATION
Cycle period
29' 10''
24' 20''
Duty cycle
0.44
0.38
Average power
consumption
60 W
52 W
Table 1: Power consumption versus Hysteresis threshold
So, it is shown that reducing the temperature ripple improves the appliance efficiency. This is can be ex-
plained by the fact that the useful energy is not wasted in vain.
The Case 2 control law enables to save 8 W, just by reducing the threshold level by a little bit more than 1 °C.
For electromechanically controlled refrigerators, where the temperature ripple is in the range of 10-20 °C, a
decrease down to a few degree Celsius, will enable to save up to 20 % of energy consumption. This means
a 18 W saving for a 140 W compressor (90 W average power with a 2/3 duty cycle).
Reducing the temperature ripple changes the compressor behavior. The motor running cycle frequency is
increasing. In our example, this frequency increases by around 20 % (2.06 cycles per hour with Case 1, and
2.46 cycles per hour with Case 2). This is not a problem for electronic switches where the cycle length of life
isfarfromthepoorcapabilityofelectromechanicalswitches.Forthemotorpointofview,thehighernumber
of cycles should not reduce its reliability as:
I
Its temperature ripple is decreased thanks to a higher cycle frequency
I
The start winding conduction length is reduced thanks to an electronic control instead of a thermal-active
solution (PTC)
I
An overcurrent protection is ensured by the MCU, that reduces the motor stress.
-24
0:00:00
-22
-20
-18
-16
-14
-12
-10
0:20:00
0:40:00
1:00:00
1:20:00
Time
T
0
50
100
150
200
P
Evap.
Cab.
Power
Fig. 11 Temperature control (Case 1)