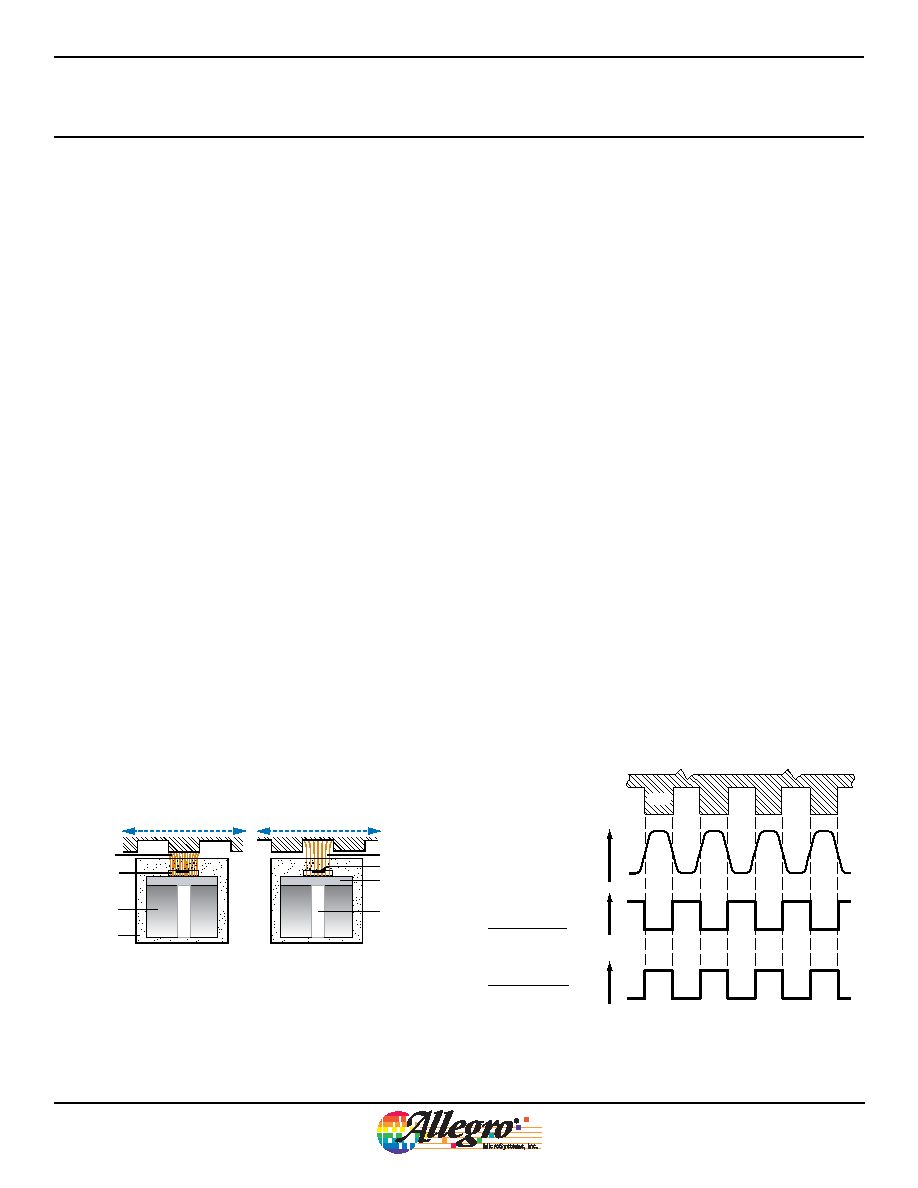
Self-Calibrating TPOS Speed Sensor
Optimized for Automotive Cam Sensing Applications
ATS675LSE
9
Allegro MicroSystems, Inc.
115 Northeast Cutoff
Worcester, Massachusetts 01615-0036 U.S.A.
1.508.853.5000; www.allegromicro.com
Functional Description
Internal Electronics
This device contains a self-calibrating Hall effect IC that provides
a Hall element, a temperature compensated amplifier, and offset
cancellation circuitry. The IC also contains a voltage regulator
that provides supply noise rejection over the operating voltage
range. The Hall transducers and the electronics are integrated
on the same silicon substrate by a proprietary BiCMOS process.
Changes in temperature do not greatly affect this device, due to
the stable amplifier design and the offset rejection circuitry.
Sensing Technology
The ATS675 gear tooth sensor contains a single-chip Hall effect
sensor IC, a 4-pin leadframe, and a specially designed rare-earth
magnet. The Hall IC supports a chopper stabilized Hall element
that measures the magnetic gradient created by the passing of a
ferrous object. This is illustrated in figure 7. The difference in
the magnetic gradients created by teeth and valleys allows the
devices to generate a digital output signal that is representative of
the target features.
Undervoltage Lockout
When the supply voltage falls below the undervoltage lockout
level, VCCUV, the device switches to the off-state. The device
remains in that state until the voltage level is restored to the VCC
operating range. Changes in the target magnetic profile have no
effect until voltage is restored. This prevents false signals caused
by undervoltage conditions from propagating to the output of the
sensor.
Power Supply Protection
The ATS675 contains an on-chip regulator and can operate over
a wide range of supply voltage levels. For applications using an
unregulated power supply, transient protection may be added
externally. For applications using a regulated supply line, EMI
and RFI protection may still be required. Contact Allegro for
information on EMC specification compliance.
Output
After proper power is applied to the device, it is then capable of
providing digital information that is representative of the profile
of a rotating gear, as illustrated in figure 8. No additional opti-
mization is needed and minimal processing circuitry is required.
This ease of use reduces design time and incremental assembly
costs for most applications.
Output Polarity
With the LT device option, the polarity of the output is low
when the Hall element is opposite a target tooth, and high when
opposite a target valley. The output polarity is opposite in the HT
option.. This is illustrated in figure 8.
TPOS (True Power-On State) Operation
Under specified operating conditions, the ATS675 is guaranteed
Figure 7. Application cross-section: (A) target tooth opposite device, and
(B) target valley opposite device
Target (Gear)
Sensor Device
High-B field
Back-Biasing
magnet
Plastic
Hall element
Leadframe
Hall IC
Low-B field
Pole piece
(Concentrator)
North Pole
South Pole
(A)
(B)
Target
Mechanical Profile
Target
Magnetic Profile
Sensor Output
Electrical Profiles
Switch State
LT device option
HT device option
Switch State
|B|
0
BIN
V+
VOUT
On
Off On Off On Off On Off
V+
VOUT
On Off On Off On Off
On
Off
Tooth Valley
Figure 8. Sensor output polarity and switch state (with device connected
as shown in figure 1): with LT option, output is low when a target tooth is
opposite the Hall element (device on), and high when a target valley is
opposite (device off)—polarity response inverts with the HT option.