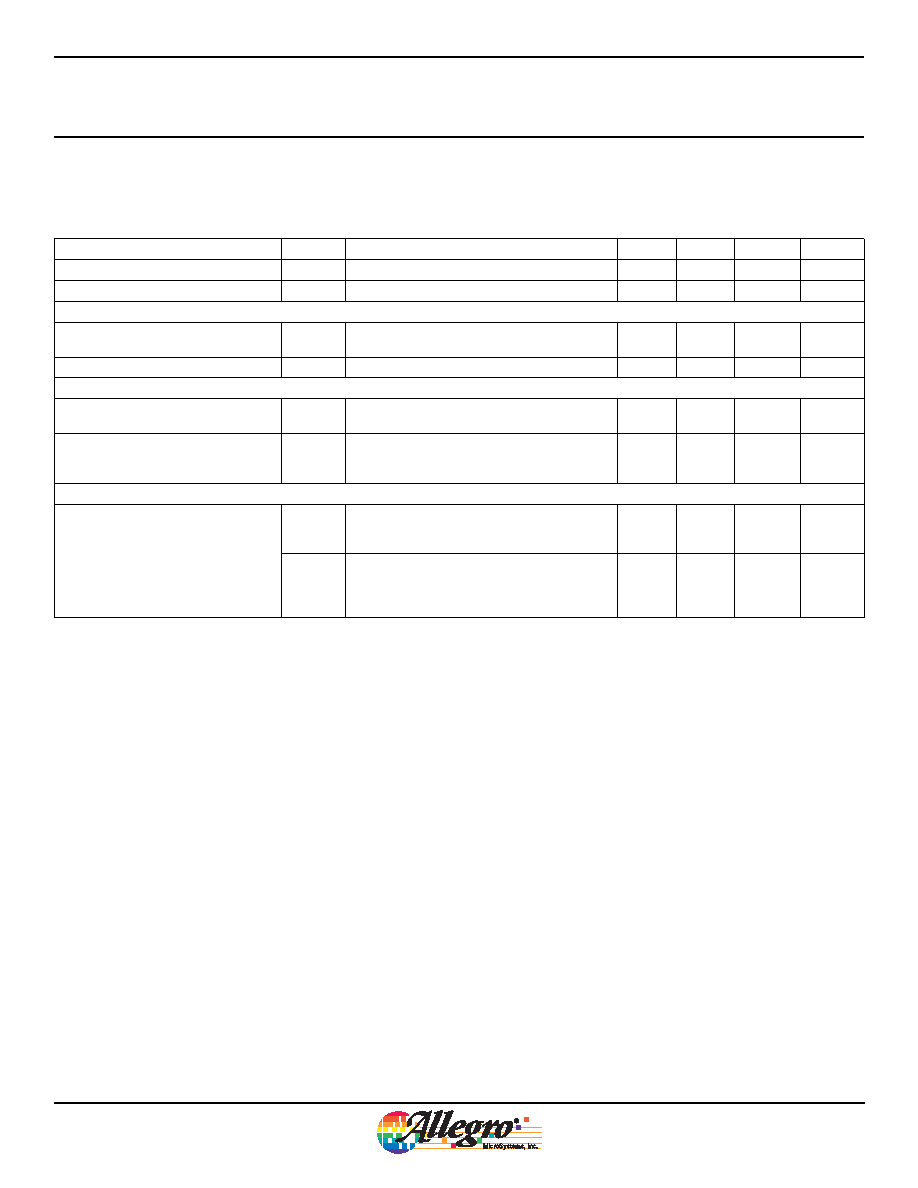
Self-Calibrating TPOS Speed Sensor
Optimized for Automotive Cam Sensing Applications
ATS675LSE
5
Allegro MicroSystems, Inc.
115 Northeast Cutoff
Worcester, Massachusetts 01615-0036 U.S.A.
1.508.853.5000; www.allegromicro.com
Tooth Speed
fSIG
Tooth signal frequency, sinusoidal input signal
0
–
8000
Hz
Analog Signal Bandwidth
BW
Equivalent to –3 dB cutoff frequency
–
20
–
kHz
Switchpoint Characteristics
Switchpoint
BST
% of peak-to-peak, referenced to tooth signal
(see figure 4)
–30
–
%
Internal Hysteresis12
BHYS
% of peak-to-peak signal
–
10
–
%
Calibration
Initial Calibration13
CALI
Quantity of mechanical falling edges during
which device is in full TPOS Mode
–
4
Edges
TPO to Running Mode Adjustment
CALTPORM
Quantity of target teeth after CALI over which
TPOS to Running Mode threshold adjustment
occurs
1
–
16
Teeth
Signal Characteristics
Maximum Allowable Signal Reduction14
Breduce(G)
Reduction in VPROC amplitude from VPROC(high)
to lowest peak VPROC(reduce), all specifications
within range (see figure 5)
–
15
%pk-pk
Breduce(NG)
Reduction in VPROC amplitude from VPROC(high)
to lowest peak VPROC(reduce); output switches,
other specifications may be out of range (see
figure 5)
–
25
%pk-pk
1Typical values are at TA = 25°C and VCC = 12 V. Performance may vary for individual units, within the specified maximum and minimum limits.
2Maximum voltage must be adjusted for power dissipation and junction temperature; see Power Derating section.
3Maximum current limit is equal to ICC(max) + 3 mA.
4Negative current is defined as conventional current coming out of (sourced from) the specified device terminal.
5Power-On Time is the duration from when VCC rises above VCC(min) until a valid output state is realized.
6Output Delay Time is the duration from when a crossing of the magnetic signal switchpoint, BST, occurs to when the electrical output signal, VOUT ,
reaches 90% of VOUT(high).
7Characterization data shows 12 V fall time to be 1.5 times longer than 5 V fall time. See figure 2.
8The Operational Air Gap Range is the range of installation air gaps within which the TPOS (True Power-On State) function is guaranteed to correctly
detect a tooth when powered-on opposite a tooth and correctly detecting a valley when powered-on opposite a valley, using reference target 8X.
9The Extended Air Gap Range is a range of installation air gaps, larger than AGTPOS, within which the device will accurately detect target features in
Running Mode, but TPOS functionality is NOT guaranteed, possibly resulting in undetected target features during Initial Calibration. Relative Timing
Accuracy (ErrREL) not guaranteed in Extended Air Gap Range.
10The term mechanical edge refers to a target feature, such as the side of a gear tooth, passing opposite the device. A rising edge is a transition from a
valley to a tooth, and a falling edge is a transition from a tooth to a valley. See figure 7.
11Relative Timing Accuracy refers to the difference in accuracy, relative to a 0.5 mm air gap, through the entire Operational Air Gap Range. See figure 7.
12Refer to Functional Description section for a description of Internal Hysteresis.
13Signal frequency, fSIG < 200 Hz.
14Running Mode; 4X target used. The Operational Signal Amplitude, VPROC, is the internal signal generated by the Hall detection circuitry and
normalized by Automatic Gain Calibration.
OPERATING CHARACTERISTICS (continued) Valid using reference target 8X, T
A, TJ, and VCC within specification, unless otherwise noted
Characteristics
Symbol
Test Conditions
Min.
Typ.1
Max.
Unit