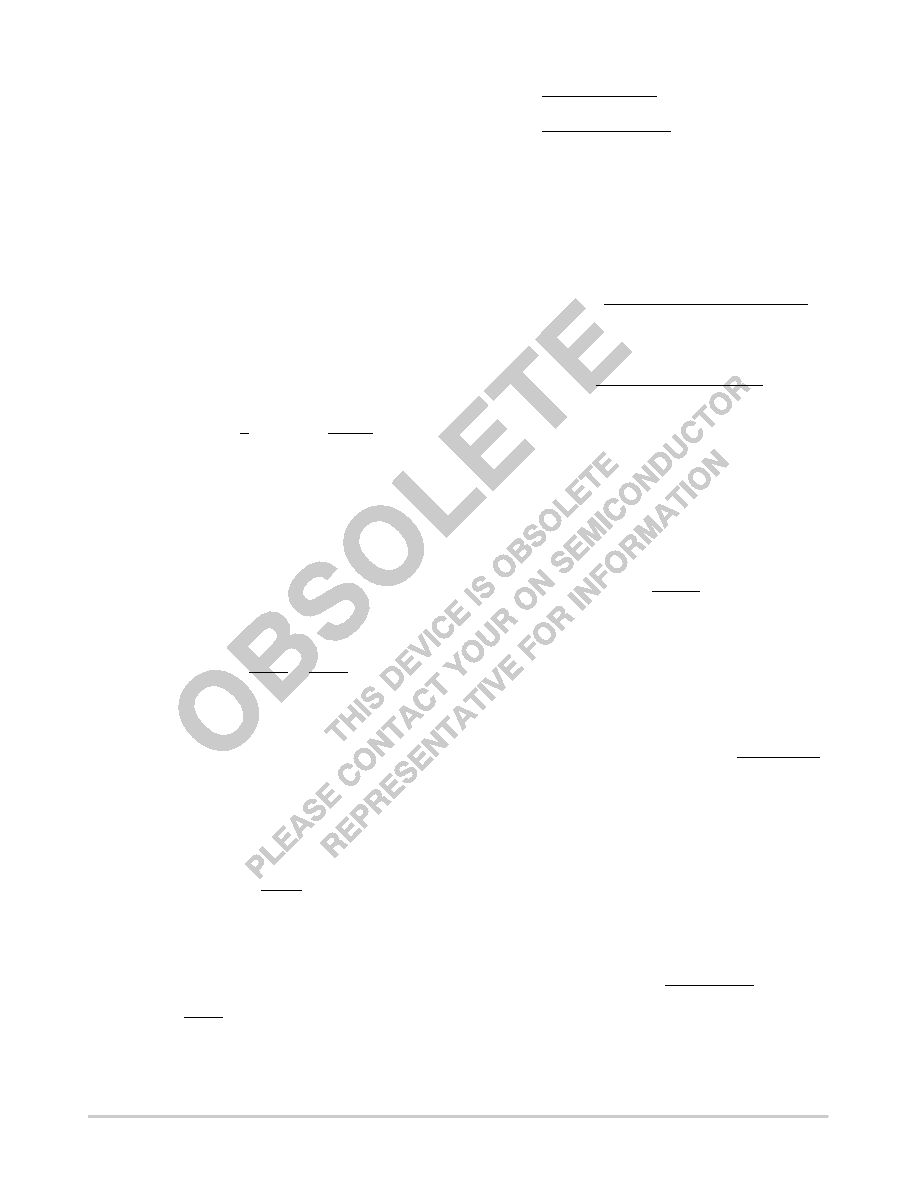
CS5165
http://onsemi.com
18
nominal output voltage before a load turnon. The total
voltage drop due to a load step is ΔV40 mV and the
deviation from the nominal output voltage is 40 mV smaller
than it would be if there was no droop resistor. Similarly at
full load the regulator output is prepositioned at 16 mV
below the nominal voltage before a load turnoff. The total
voltage increase due to a load turnoff is ΔV16 mV and the
deviation from the nominal output voltage is 16 mV smaller
than it would be if there was no droop resistor. This is
because the output capacitors are precharged to value that
is either 40 mV above the nominal output voltage before a
load turnon or, 16 mV below the nominal output voltage
before a load turnoff (see Figure
15).
Obviously, the larger the voltage drop across the droop
resistor ( the larger the resistance), the worse the DC and
load regulation, but the better the AC transient response.
Design Rules for Using a Droop Resistor
The basic equation for laying an embedded resistor is:
RAR + ò
L
A
or R + ò
L
(W
t)
where:
A = W × t = crosssectional area
ρ = the copper resistivity (μΩ mil)
L = length (mils)
W = width (mils)
t = thickness (mils)
For most PCBs the copper thickness, t, is 35 μm (1.37
mils) for one ounce copper. ρ = 717.86 μΩmil
For a Pentium II load of 14.2 A the resistance needed to
create a 56 mV drop at full load is:
Response Droop + 56 mV
IOUT
+ 56 mV
14.2 A +
3.9 mW
The resistivity of the copper will drift with the
temperature according to the following guidelines:
DR + 12% @ TA +) 50°C
DR + 34% @ TA +) 100°C
Droop Resistor Width Calculations
The droop resistor must have the ability to handle the load
current and therefore requires a minimum width which is
calculated as follows (assume one ounce copper thickness):
W +
ILOAD
0.05
where:
W = minimum width (in mils) required for proper power
dissipation, and ILOAD Load Current Amps.
The PentiumII maximum load current is 14.2 A.
Therefore:
W + 14.2 A
0.05 +
284 mils + 0.7213 cm
Droop Resistor Length Calculation
L +
RDROOP
W
t
ò
+ 0.0039
284
1.37
717.86
+ 2113 mil + 5.36 cm
Output Inductor
The inductor should be selected based on its inductance,
current capability, and DC resistance. Increasing the
inductor value will decrease output voltage ripple, but
degrade transient response.
Inductor Ripple Current
Ripple Current +
[(VIN * VOUT)
VOUT]
(Switching Frequency
L
VIN)
Example: VIN = +5.0 V, VOUT = +2.8 V, ILOAD = 14.2 A,
L = 1.2 μH, Freq = 200 kHz
Ripple Current +
[(5.0 V * 2.8 V)
2.8 V]
[200 kHz
1.2 mH
5.0 V] +
5.1 A
Output Ripple Voltage
VRIPPLE + Inductor Ripple Current
Output Capacitor ESR
Example:
VIN = +5.0 V, VOUT = +2.8 V, ILOAD = 14.2 A, L = 1.2 μH,
Switching Frequency = 200 kHz
Output Ripple Voltage = 5.1 A × Output Capacitor ESR
(from manufacturer’s specs)
ESR of Output Capacitors to limit Output Voltage Spikes
ESR + D
VOUT
DIOUT
This applies for current spikes that are faster than
regulator response time. Printed Circuit Board resistance
will add to the ESR of the output capacitors.
In order to limit spikes to 100 mV for a 14.2 A Load Step,
ESR = 0.1/14.2 = 0.007 Ω
Inductor Peak Current
Peak Current + Maximum Load Current )
Ripple Current
2
Example: VIN = +5.0 V, VOUT = +2.8 V, ILOAD = 14.2 A,
L = 1.2 μH, Freq = 200 kHz
Peak Current + 14.2 A ) (5.1 2) + 16.75 A
A key consideration is that the inductor must be able to
deliver the Peak Current at the switching frequency without
saturating.
Response Time to Load Increase
(limited by Inductor value unless Maximum OnTime is
exceeded)
Response Time +
L
DIOUT
(VIN * VOUT)
Example: VIN = +5.0 V, VOUT = +2.8 V, L = 1.2 μH, 14.2 A
change in Load Current