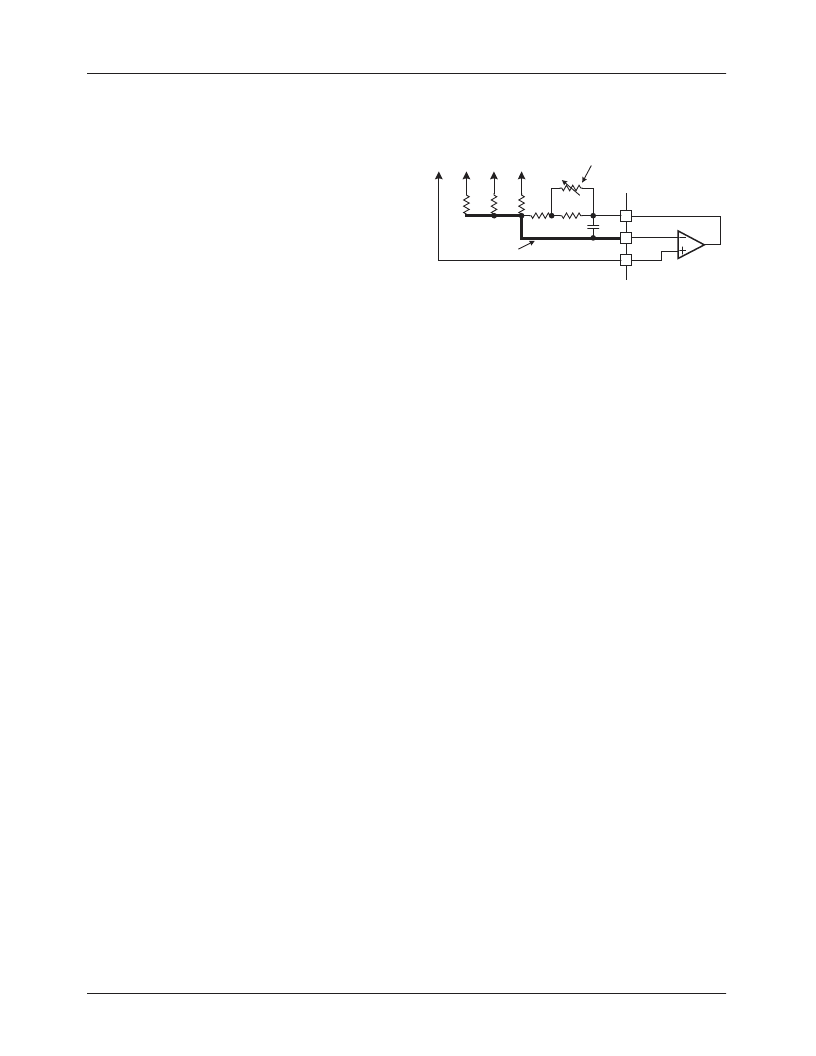
FAN53180
PRODUCT SPECIFICATION
18
REV. 1.0.0 6/10/03
Sumida Electric Company
(510) 668-0660
www.sumida.com
Vishay Intertechnology
(402) 563-6866
www.vishay.com
Output Droop Resistance
The design requires that the regulator output voltage
measured at the CPU pins drops when the output current
increases. The specified voltage drop corresponds to a DC
output resistance (R
O
).
The output current is measured by summing together the
voltage across each inductor and then passing the signal
through a low-pass filter. This summer-filter is the CS
amplifier configured with resistors R
PH(X)
(summers), and
R
CS
and C
CS
(filter). The output resistance of the regulator is
set by the following equations, where R
L
is the DCR of the
output inductors:
One has the flexibility of choosing either R
CS
or R
PH(X)
. It is
best to select R
CS
equal to 100k
, and then solve for R
PH(X)
by rearranging Equation 6.
Next, use Equation 7 to solve for C
CS
:
It is best to have a dual location for C
CS
in the layout so stan-
dard values can be used in parallel to get as close to the value
desired. For this example, choosing C
CS
to be 4.7nF is a
good choice. For best accuracy, C
CS
should be a 5% or 10%
NPO capacitor. A close standard 1% value for R
PH(X)
is
100k
.
Inductor DCR Temperature Correction
With the inductor’s DCR being used as the sense element,
and copper wire being the source of the DCR, one needs to
compensate for temperature changes of the inductor’s wind-
ing. Fortunately, copper has a well-known temperature co-
efficient (TC) of 0.39%/°C.
If R
CS
is designed to have an opposite and equal percentage
change in resistance to that of the wire, it will cancel the
temperature variation of the inductor's DCR. Due to the non-
linear nature of NTC thermistors, resistors R
CS1
and R
CS2
are needed (see Figure 5) to linearize the NTC and produce
the desired temperature tracking.
Figure 5. Temperature Compensation Circuit
The following procedure and expressions will yield values to
use for R
CS1
, R
CS2
, and R
TH
(the thermistor value at 25°C)
for a given R
CS
value.
1.
Select an NTC to be used based on type and value. Since
we do not have a value yet, start with a thermistor with a
value close to R
CS
. The NTC should also have an initial
tolerance of better than 5%.
2.
Based on the type of NTC, find its relative resistance
value at two temperatures. The temperatures to use that
work well are 50°C and 90°C. We will call these resis-
tance values A (A is R
TH(50°C)
/R
TH(25°C)
) and B (B is
R
TH(90°C)
/R
TH(25°C)
). Note that the NTC’s relative value
is always 1 at 25°C.
3.
Next, find the relative value of R
CS
required for each of
these temperatures. This is based on the percentage
change needed, which we will initially make 0.39%/°C.
We will call these r
1
and r
2
where:
TC = 0.0039
T
1
= 50°C
T
2
= 90°C
4.
Compute the relative values for R
CS1
, R
CS2
, and R
TH
using:
R
O
R
PH X
------------------
R
L
×
=
(6)
C
CS
L
CS
------------------------
=
(7)
R
PH X
R
L
R
O
-------
R
CS
×
=
R
PH X
------------------
100k
×
123k
=
=
C
CS
------------------------------------------
4.06nF
=
=
18
17
16
CSREF
CSSUM
CSCOMP
CSA
C
CS
1.8nF
R
CS1
R
CS2
R
TH
R
PH1
R
PH3
R
PH2
Keep this path as
short as possible
and well away from
Switch Node lines
Place as close as
possible to nearest
inductor or low-side
MOSFET
To Switch Nodes
To V
OUT
sense
r
1
1
–
)
+
)
----------------------------------------------------
=
r
2
2
)
)
------+
=
r
CS2
A
B
–
(
-----------------------------------------–
)
r
×
r
A
1
1
B
–
(
)
–
–
r
2
A
B
–
)
)
r
1
×
–
×
×
B
–
A
×
=
r
CS1
)
CS2
-----–
CS2
1
-----–
–
----------------------–
=
(8)
r
TH
CS2
---–
CS1
-----------
–
---------------------------------------
=