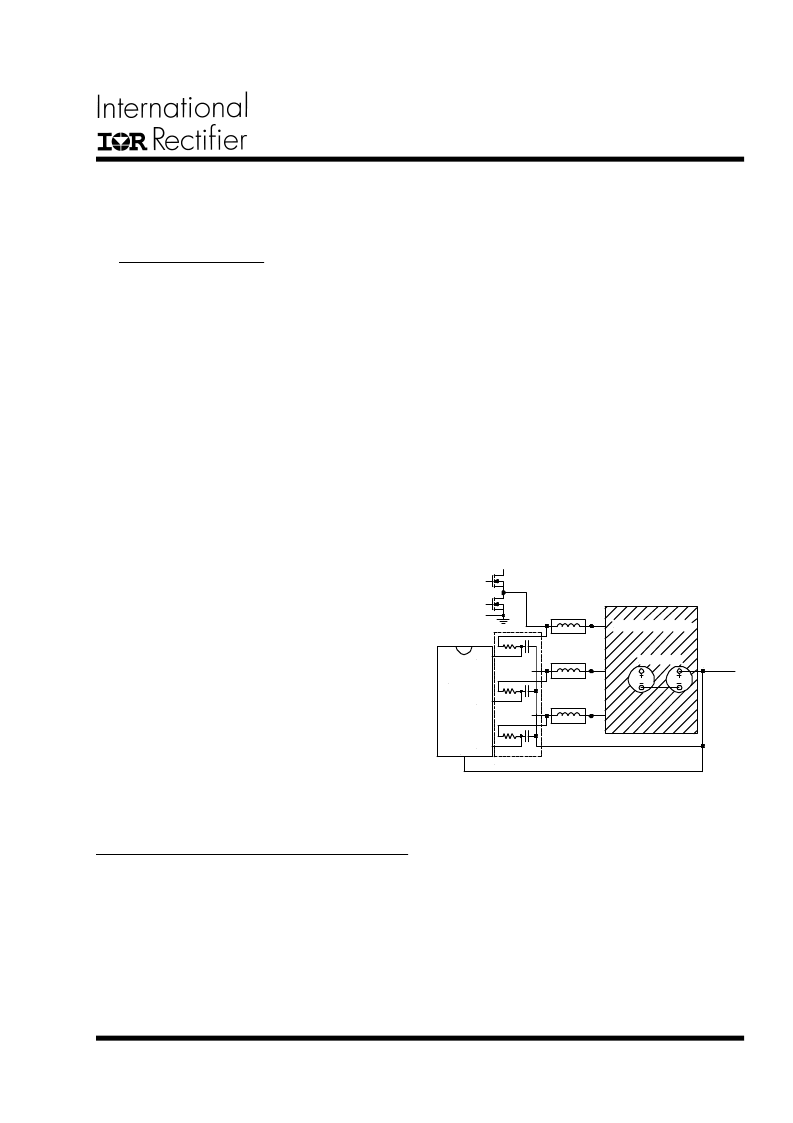
IRU3055
15
Rev. 1.4
08/13/02
www.irf.com
(4). Place the other 2-phase Q3, Q4 and Q5, Q6 follow-
ing the same rule.
(5) Place output inductor Lo1, Lo2, Lo3 and output ca-
pacitor C
OUT
. Make sure the output capacitors are evenly
distributed among 3-phases and close to the output slot.
(6) Place IC IRU3055 such that the driver pins, HDrv1,
HDrv2, Hdrv3 and LDrv1, LDrv2, LDrv3, have a relatively
short distance from the corresponding MOSFET gate. In
addition, make the 3-phase driving signal path as sym-
metrical as possible. If the length of the gate signal path
is more than 1cm long, a 2 to 10
gate resistor is rec-
ommended to be in series in the gate signal path.
(7) Place bypass capacitor close to Vcc pin, V
REF
pin
and V
CH12
,V
CH3
pins and also soft-start capacitor to SS
pin.
(8) Place a frequency selection resistor (Rt) close to Rt
pin.
(9) Connect output inductor current sensing network such
as R2, C8 close to IRU3055. One example of the layout
is shown as follows:
Figure 13 - An example of layout connection for
inductor current sensing.
Connect current sensing resistors Rs1,Rs2,Rs3 right
to the pads of output inductor Lo1,Lo2,Lo3. Connect the
other node of current sensing capacitors Cs1,Cs2,Cs3
together and directly connect to the output voltage ter-
minal, which is also the sensing point for output voltage
feedback sensing.
(10) Place feedback resistors (R
FB1
and R
FB2
) close to IC
and place compensator network close to Comp pin. Note
that the resistor R
FB1
and R
FB2
, can be used to set the
outputs slightly higher to account for the output drop at
the load due to the trace resistance.
In practice, the resistor Rc (R6 in Fig.3) can be tuned for
a better dynamic load response. Higher Rc will result in
a fast transient response. Cc (C12 in Fig.3) can be kept
unchanged. In Fig.3. R6=27K
.
(8) Input Capacitor Selection
From the Figure 12, according to the duty ratio, pick
up the normalized input RMS current. For this ex-
ample:
Select Panosonic capacitor. Four EEUFJ1C152U
with1500
μ
F give results to:
Layout Considerations
For any switching converter, the current transition from
one power device to another usually causes voltage
spikes across the power component due to parasitic
inductance and capacitance. These voltage spikes will
result in reduction of efficiency, increased voltage stress
of power components and radiated noise to circuit. A
good layout can minimize these effects.
There are several critical loops for IRU3055 controlled
multi-phase converter. The loop by synchronous
MOSFETs and input capacitor is the most critical loop
and it should be minimized as small as possible. Put a
small ceramic capacitor next to the drain of high side
switch and source of low side switch. Put the input ca-
pacitors to the high and low side switch as close as
possible. The second loop is the gate of MOSFETs and
the drivers from IRU3055. Because the IRU3055 includes
the MOSFETs drivers inside, the signal path between
driver to the gate of MOSFETs should be minimized.
The trace should handle 1A transient current ability.
The following is a guideline of how to place the critical
components and the connections between components
in order to minimize the switching noises.
Start the layout by first placing the power components:
(1) Place the high side MOSFET Q1 and low side
MOSFET Q2 as close to each other as possible so that
the source of Q1 and drain of Q2 has the most possible
shortest length.
(2) Place a capacitor (Electrolytic or ceramic or both)
close to the drain of Q1 and source of Q2.
(3). If needed, place a snubber RC circuit next to Q2.
I
RMS(IN)
/I
OUT
= 0.15
I
RMS(IN)
= 0.15
×
60A = 9A
4
×
2.5 = 10A RMS current.
CS1
CS2
CS3
IRU3055
Fb
V
OUT
Output Cap
Output copper plane
Close to IRU3055