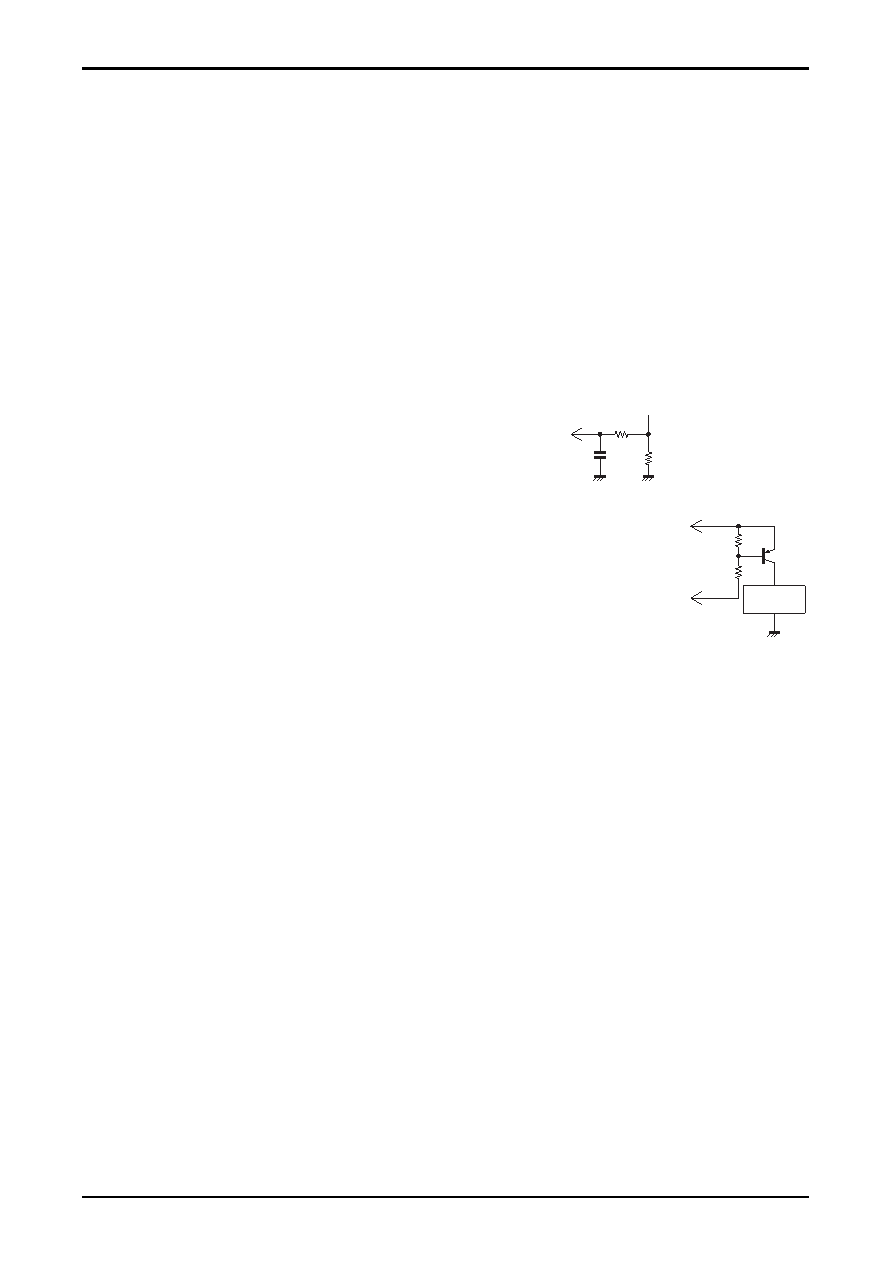
LB11823M
No.7106-11/18
LB11823M Function Description
1. Output drive circuit
This IC employs a direct PWM drive method to minimize the power loss at output. The output Tr is normally saturated
in the ON condition, adjusting the motor drive power by changing the output on-duty. Output PWM switching is made
on UH, VH, and WH output sides. Since UL - WL and UH - WH outputs are of the same output form, either lower
PWM or upper PWM can be selected by changing the external output Tr connection method.
Selection of diode to be connected to the non-PWM side output requires attention because there is a problem of reverse
recovery time. (Unless a diode with the short reverse recovery time is selected, the through current flows in an instant
when the PWM side Tr is turned ON.)
UL - WL and UH - WH outputs enter the high impedance condition at a time of stop or when the supply voltage is
extremely low (below the allowable operation voltage). Accordingly, an appropriate measure (pull-down resistor, etc.)
is necessary in the external circuit to prevent an incorrect action due to the leak current.
2. Current limiting circuit
The current limiting circuit performs limiting with the current determined from I = VRF/Rf (VRF = 0.5Vtyp, Rf :
current detector resistance) (that is, this circuit limits the peak current). Limiting operation includes decrease in the
output on-duty to suppress the current. The current limiting circuit incorporates a filter circuit to prevent an incorrect
action of current limiting operation due to detection of the reverse recovery current of output diode during PWM
operation. This internal filter circuit will be enough to prevent
trouble for normal application. In case of an incorrect action (diode
reverse recovery current flowing for 1
μs or more), add an external
filter circuit (R, C low pass filter, etc.).
3. Power save circuit
This IC enters the power save condition to decrease the current dissipation in the stop
mode. In this condition, the bias current of most of circuits is cut off. Even in the
power save condition, the 5V regulator output (VREG) is given. If the bias current of
Hall device is to be cut, 5V and Hall device may be connected via PNP Tr as a means
to meet such needs.
4. Compatibility with various power supplies
To operate this IC with external 5V power supply (4.5 - 5.5V), short-circuit VCC1 and VREG pin for connection to
power supply.
To operate this IC with external 12V power supply (8 - 13.5V), connect power supply to VCC1 (5V is generated at the
VREG pin to function as a power supply to the control circuit).
To operate this IC with external 15V power supply (13.5 - 19V), connect power supply to VCC3 and short-circuit
12REG and VCC1 pins (12V is generated at the 12REG pin to function as a power supply to VCC1).
Connect the VCC2 pin basically to the VREG pin. In an application in which the motor rotation speed is to be
determined by the external fixed voltage (resistor division, etc.), set VCC2 to 12V (by connecting to VCC1) to suppress
variation of the output duty. (Variation of IC is difficult to affect adversely because of increase in the PWM oscillation
amplitude and in the comparator dynamic range.)
5. PWM frequency
PWM frequency is determined from the capacity C (F) of capacitor connected to the PWM pin.
fPWM
≈ 1/(45000 × C)
Connection of a 1000pF capacitor causes oscillation of about 22kHz. Excessively low PWM frequency causes causes a
switching sound from the motor while excessively high PWM frequency causes increase in the power loss at the output.
About 15 - 50kHz is recommended. Capacitor GND should be arranged near the IC GND pin as much as possible to
protect from the effect of output noise.
To pin RF
Current detection resistance
To pin VREG
To pin S/S
Hall device