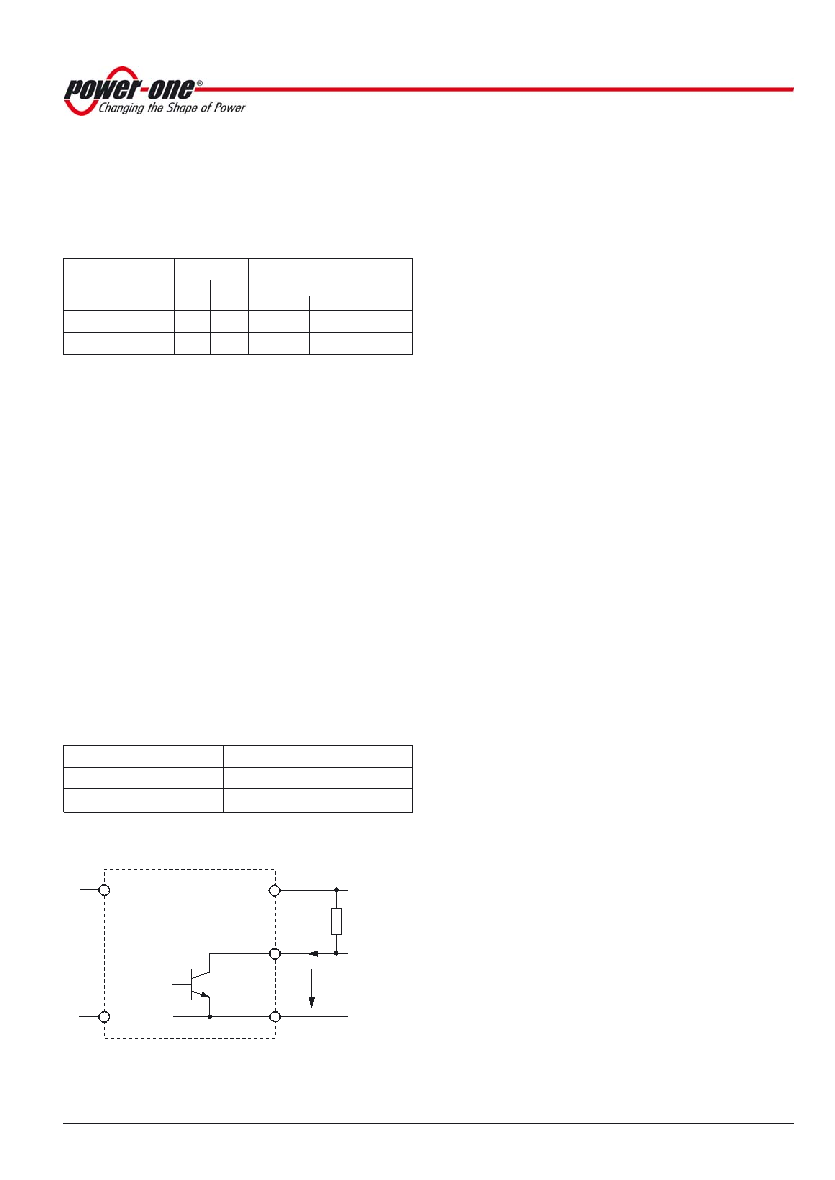
BCD20001-G Rev AB
Page 26 of 28
www.power-one.com
K Series with PFC Data Sheet
150 – 280 Watt AC-DC Converters
Fig. 41
Output configuration of options V2 and V3
Vo1+
Vo1–
V
VV
IV
Rp
Input
11009
After the ACFAIL signal has gone low, the VME standard
requires a hold-up time th of at least 4 ms before the 5.1 V
output drops at full load to 4.875 V. This hold-up time th is
provided by the capacitance supporting the boost voltage
Vb. See: Hold-up Time.
Table 23: Undervoltage monitor functions
V output
Monitoring
Minimum adjustment
(VME compatible)
Vb
Vo1
range of threshold level
Vtb
Vto
V2
yes
no
355 VDC 1–
V3
yes
355 VDC 1 0.95
– 0.985 Vo12
1
Option V monitors the boost regulator output voltage. The
trigger level is adjusted in the factory to 355 VDC.
2
Fixed value between 95% and 98.5% of Vo1
Option V operates independently of the built-in input
undervoltage lockout circuit. A logic "low" signal is
generated at pin 20 as soon as one of the monitored
voltages drops below the preselected threshold level Vt.
The return for this signal is Vo–. The V output recovers,
when the monitored voltage(s) exceed(s) Vt + Vh. The
threshold level Vtb is adjusted in the factory to 355 VDC.
The threshold level Vto is adjusted in the factory to a
customer-specified value.
V-output (V2, V3):
Connector pin V is internally connected to the open collec-
tor of an NPN transistor. The emitter is connected to the
negative potential of the main output. VV
≤ 0.6 V (logic low)
corresponds to a monitored voltage level (Vi and/or Vo)
<Vt.
The current IV through the open collector should not ex-
ceed 50 mA. The NPN output is not protected against ex-
ternal overvoltages. VV should not exceed 60 V.
Table 24: Status of V output
Vb, Vo status
V output, VV
Vb or Vo
< Vt
low, L, VV
≤ 0.6 V at IV = 50 mA
Vb and Vo1
> Vt + Vh
high, H, IV
≤ 25 A at VV = 5.1 V
K Connector H15S4
Models with 5.1 V output are fitted with a connector H15S4
(rather than H15S2). This option should be used for new
designs and provides compatibility to LK1001 models.
B1 Cooling Plate (see: Mechanical Data)
Where a cooling surface is available, we recommend the
use of a cooling plate (option B1) instead of the standard
heat sink. The mounting system should ensure sufficient
cooling capacity to guarantee that the maximum case tem-
perature TC max is not exceeded. The cooling capacity is
calculated by:
(100% –
η
)
PLoss = –––––––––– Vo Io
η
Efficiency
η see: Model Selection
Elongated case for 220 mm rack depth need: Option B2.