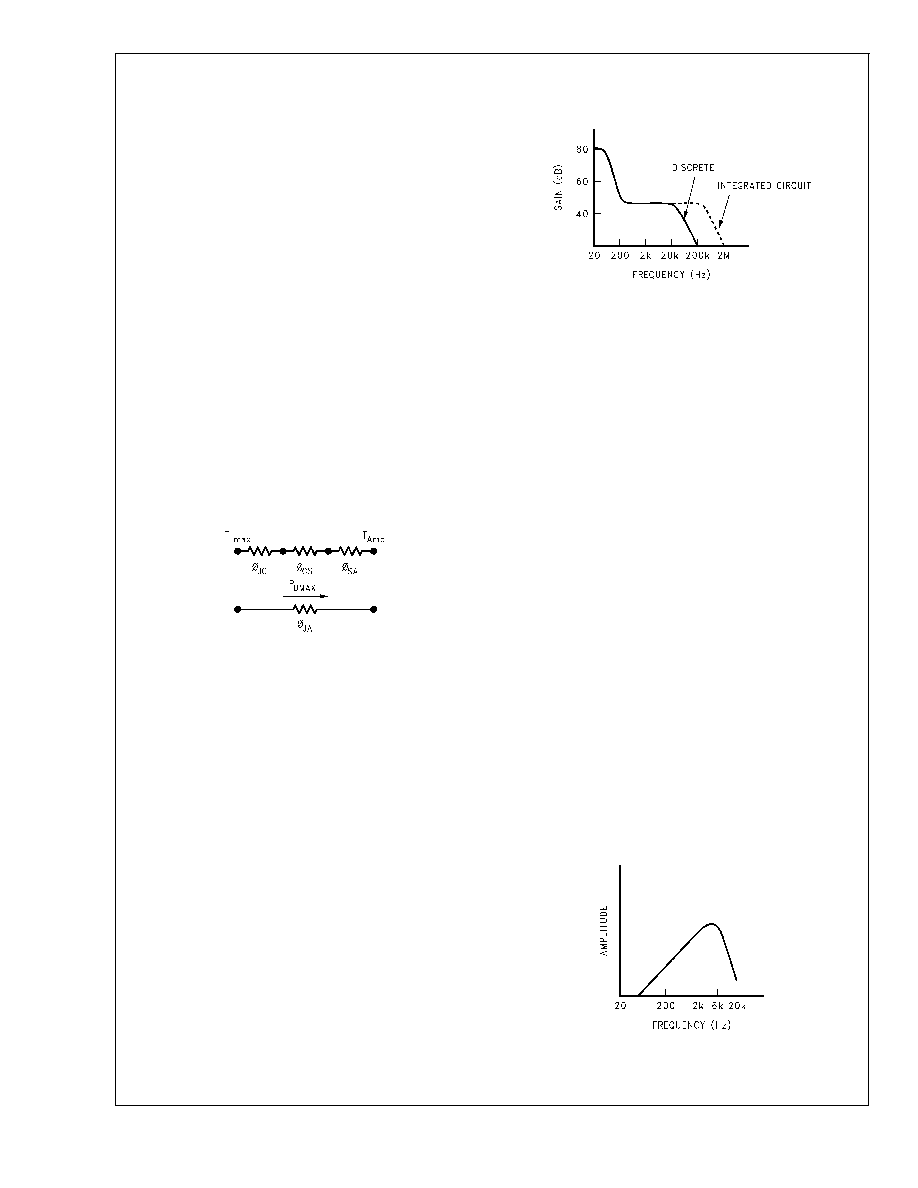
Application Information (Continued)
P
DAVE =VCC VOpk/πRL VOpk
2/2R
L
(3)
where V
CC is the total supply voltage.
Determining the Correct Heat Sink
Once the maximum IC power dissipation is known for a
given supply voltage, rated load, and the desired rated out-
put power the maximum thermal resistance (in C/W) of a
heat sink can be calculated. This calculation is made using
Equation (4) and is based on the fact that thermal heat flow
parameters are analogous to electrical current flow proper-
ties.
It is also known that typically the thermal resistance,
θ
JC
(junction to case), of the LM3886 is 1C/W and that using
Thermalloy Thermacote thermal compound provides a ther-
mal resistance,
θ
CS (case to heat sink), of about 0.2C/W as
explained in the Heat Sinking section.
Referring to the figure below, it is seen that the thermal resis-
tance from the die (junction) to the outside air (ambient) is a
combination of three thermal resistances, two of which are
known,
θ
JC and θCS. Since convection heat flow (power dis-
sipation) is analogous to current flow, thermal resistance is
analogous to electrical resistance, and temperature drops
are analogous to voltage drops, the power dissipation out of
the LM3886 is equal to the following:
P
DMAX =(TJmax TAmb)/θJA
where
θ
JA = θJC + θCS + θSA
But since we know P
DMAX, θJC, and θSC for the application
and we are looking for
θ
SA, we have the following:
θ
SA = [(TJmax TAmb)PDMAX (θJC + θCS)]/PDMAX
(4)
Again it must be noted that the value of
θ
SA is dependent
upon the system designer’s amplifier application and its cor-
responding parameters as described previously. If the ambi-
ent temperature that the audio amplifier is to be working un-
der is higher than the normal 25C, then the thermal
resistance for the heat sink, given all other things are equal,
will need to be smaller.
Equations (1), (4) are the only equations needed in the de-
termination of the maximum heat sink thermal resistance.
This is of course given that the system designer knows the
required supply voltages to drive his rated load at a particular
power output level and the parameters provided by the semi-
conductor manufacturer. These parameters are the junction
to case thermal resistance,
θ
JC,TJmax = 150C, and the rec-
ommended Thermalloy Thermacote thermal compound re-
sistance,
θ
CS.
SIGNAL-TO-NOISE RATIO
In the measurement of the signal-to-noise ratio, misinterpre-
tations of the numbers actually measured are common. One
amplifier may sound much quieter than another, but due to
improper testing techniques, they appear equal in measure-
ments. This is often the case when comparing integrated cir-
cuit designs to discrete amplifier designs. Discrete transistor
amps often “run out of gain” at high frequencies and there-
fore have small bandwidths to noise as indicated below.
Integrated circuits have additional open loop gain allowing
additional feedback loop gain in order to lower harmonic dis-
tortion and improve frequency response. It is this additional
bandwidth that can lead to erroneous signal-to-noise mea-
surements if not considered during the measurement pro-
cess. In the typical example above, the difference in band-
width appears small on a log scale but the factor of 10 in
bandwidth, (200 kHz to 2 MHz) can result in a 10 dB theoreti-
cal difference in the signal-to-noise ratio (white noise is pro-
portional to the square root of the bandwidth in a system).
In comparing audio amplifiers it is necessary to measure the
magnitude of noise in the audible bandwidth by using a
“weighting” filter (Note 18). A “weighting” filter alters the fre-
quency response in order to compensate for the average hu-
man ear’s sensitivity to the frequency spectra. The weighting
filters at the same time provide the bandwidth limiting as dis-
cussed in the previous paragraph.
Note 18: CCIR/ARM:
A Practical Noise Measurement Method; by Ray
Dolby, David Robinson and Kenneth Gundry, AES Preprint No. 1353 (F-3).
In addition to noise filtering, differing meter types give differ-
ent noise readings. Meter responses include:
1.
RMS reading,
2.
average responding,
3.
peak reading, and
4.
quasi peak reading.
Although theoretical noise analysis is derived using true
RMS based calculations, most actual measurements are
taken with ARM (Average Responding Meter) test equip-
ment.
Typical signal-to-noise figures are listed for an A-weighted fil-
ter which is commonly used in the measurement of noise.
The shape of all weighting filters is similar, with the peak of
the curve usually occurring in the 3 kHz–7 kHz region as
shown below.
DS011833-12
DS011833-13
DS011833-14
LM3886
www.national.com
14