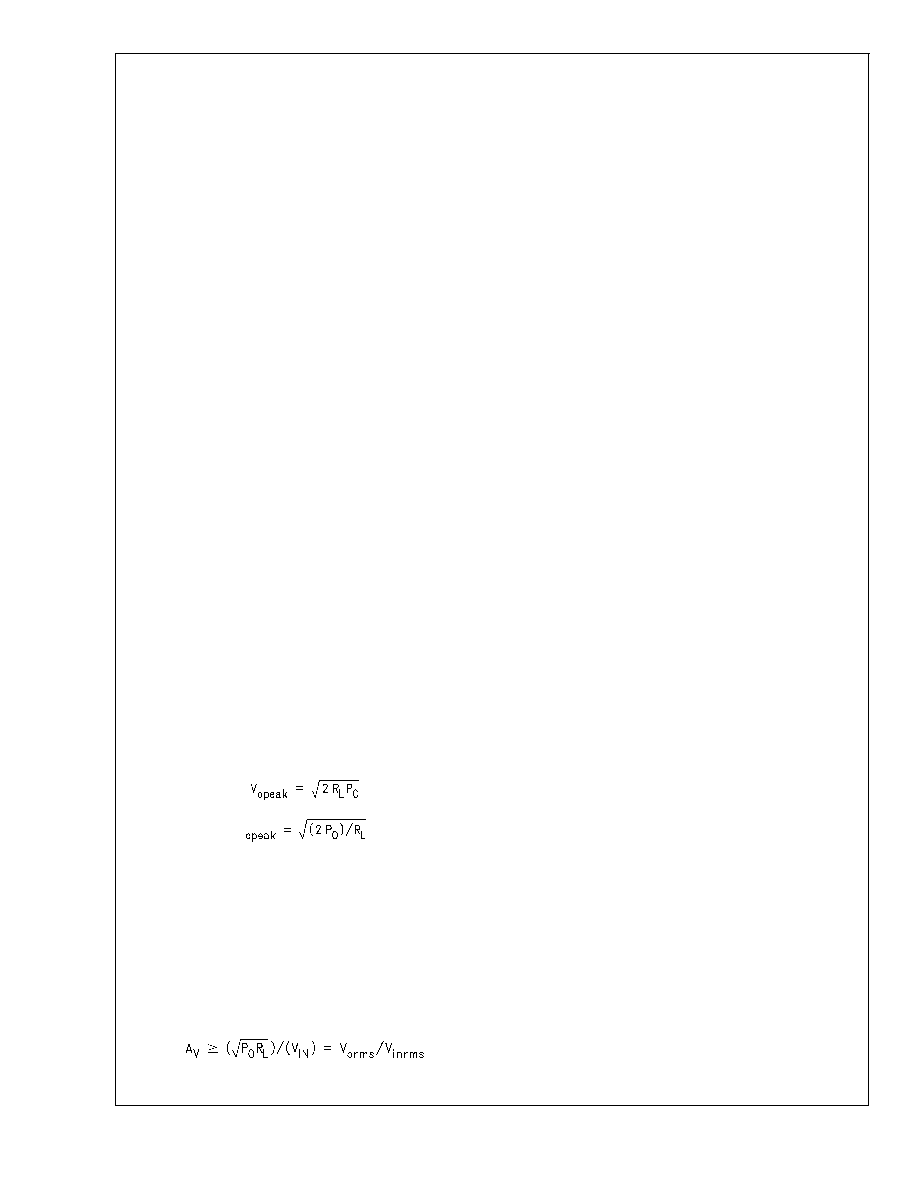
Application Information (Continued)
small capacitor, C
C, (on the order of 50 pF to 500 pF) across
the LM3886 input terminals. Refer to the External Compo-
nents Description section relating to component interaction
with C
f.
REACTIVE LOADING
It is hard for most power amplifiers to drive highly capacitive
loads very effectively and normally results in oscillations or
ringing on the square wave response. If the output of the
LM3886 is connected directly to a capacitor with no series
resistance, the square wave response will exhibit ringing if
the capacitance is greater than about 0.2 F. If highly capaci-
tive loads are expected due to long speaker cables, a
method commonly employed to protect amplifiers from low
impedances at high frequencies is to couple to the load
through a 10
resistor in parallel with a 0.7 H inductor. The
inductor-resistor combination as shown in the Typical Appli-
cation Circuit isolates the feedback amplifier from the load
by providing high output impedance at high frequencies thus
allowing the 10
resistor to decouple the capacitive load and
reduce the Q of the series resonant circuit. The LR combina-
tion also provides low output impedance at low frequencies
thus shorting out the 10
resistor and allowing the amplifier
to drive the series RC load (large capacitive load due to long
speaker cables) directly.
GENERALIZED AUDIO POWER AMPLIFIER DESIGN
The system designer usually knows some of the following
parameters when starting an audio amplifier design:
Desired Power Output
Input Level
Input Impedance
Load Impedance
Maximum Supply Voltage
Bandwidth
The power output and load impedance determine the power
supply requirements, however, depending upon the applica-
tion some system designers may be limited to certain maxi-
mum supply voltages. If the designer does have a power
supply limitation, he should choose a practical load imped-
ance which would allow the amplifier to provide the desired
output power, keeping in mind the current limiting capabili-
ties of the device. In any case, the output signal swing and
current are found from (where P
O is the average output
power):
(5)
(6)
To determine the maximum supply voltage the following pa-
rameters must be considered. Add the dropout voltage (4V
for LM3886) to the peak output swing, V
opeak, to get the sup-
ply rail value (i.e. ± (V
opeak + Vod) at a current of Iopeak). The
regulation of the supply determines the unloaded voltage,
usually about 15% higher. Supply voltage will also rise 10%
during high line conditions. Therefore, the maximum supply
voltage is obtained from the following equation:
Max. supplies ) ± (V
opeak + Vod)(1 + regulation)(1.1)(7)
The input sensitivity and the output power specs determine
the minimum required gain as depicted below:
(8)
Normally the gain is set between 20 and 200; for a 40W, 8
audio amplifier this results in a sensitivity of 894 mV and
89 mV, respectively. Although higher gain amplifiers provide
greater output power and dynamic headroom capabilities,
there are certain shortcomings that go along with the so
called “gain.” The input referred noise floor is increased and
hence the SNR is worse. With the increase in gain, there is
also a reduction of the power bandwidth which results in a
decrease in feedback thus not allowing the amplifier to re-
spond quickly enough to nonlinearities. This decreased abil-
ity to respond to nonlinearities increases the THD + N speci-
fication.
The desired input impedance is set by R
IN. Very high values
can cause board layout problems and DC offsets at the out-
put. The value for the feedback resistance, R
f1, should be
chosen to be a relatively large value (10 k
–100 k), and
the other feedback resistance, Ri, is calculated using stan-
dard op amp configuration gain equations. Most audio ampli-
fiers are designed from the non-inverting amplifier configura-
tion.
DESIGN A 40W/4
AUDIO AMPLIFIER
Given:
Power Output
40W
Load Impedance
4
Input Level
1V(max)
Input Impedance
100 k
Bandwidth
20 Hz–20 kHz ± 0.25 dB
Equations (5), (6) give:
40W/4
V
opeak = 17.9V
I
opeak = 4.5A
Therefore the supply required is: ±21.0V @ 4.5A
With 15% regulation and high line the final supply voltage is
±26.6V using Equation (7). At this point it is a good idea to
check the Power Output vs Supply Voltage to ensure that the
required output power is obtainable from the device while
maintaining low THD + N. It is also good to check the Power
Dissipation vs Supply Voltage to ensure that the device can
handle the internal power dissipation. At the same time de-
signing in a relatively practical sized heat sink with a low
thermal resistance is also important. Refer to Typical Per-
formance Characteristics graphs and the Thermal Con-
siderations section for more information.
The minimum gain from
Equation (8) is:
A
V ≥ 12.6
We select a gain of 13 (Non-Inverting Amplifier); resulting in
a sensitivity of 973 mV.
Letting R
IN equal 100 k gives the required input imped-
ance, however, this would eliminate the “volume control” un-
less an additional input impedance was placed in series with
the 10 k
potentiometer that is depicted in Figure 1. Adding
the additional 100 k
resistor would ensure the minumum
required input impedance.
For low DC offsets at the output we let R
f1 = 100 k. Solving
for Ri (Non-Inverting Amplifier) gives the following:
Ri=R
f1/(AV 1) = 100k/(13 1) = 8.3 k; use 8.2 k
The bandwidth requirement must be stated as a pole, i.e.,
the 3 dB frequency. Five times away from a pole gives
0.17 dB down, which is better than the required 0.25 dB.
Therefore:
f
L =20 Hz/5=4 Hz
f
H = 20 kHz x 5 = 100 kHz
At this point, it is a good idea to ensure that the
Gain-Bandwidth Product for the part will provide the de-
signed gain out to the upper 3 dB point of 100 kHz. This is
why the minimum GBWP of the LM3886 is important.
LM3886
www.national.com
16