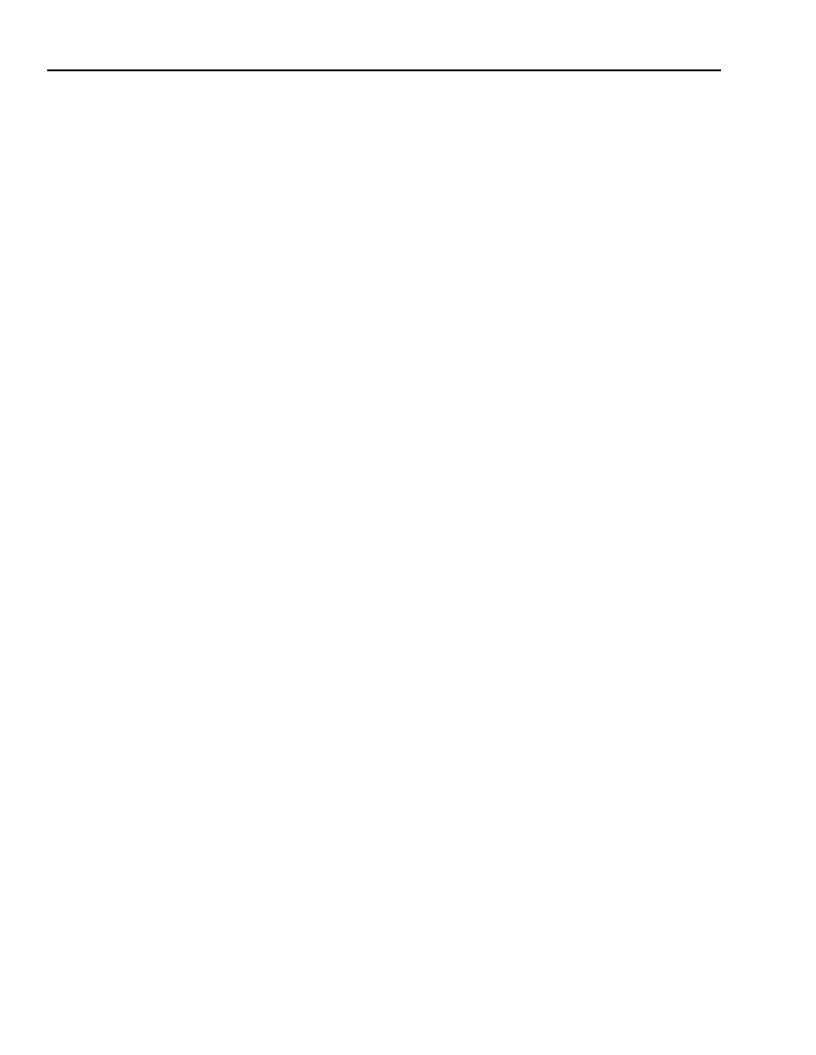
Data Sheet
September 2001
Short-Loop Sine Wave Ringing SLIC
L9215A/G
24
Agere Systems Inc.
Applications
Power Control
Under normal device operating conditions, power dissi-
pation on the device must be controlled to prevent the
device temperature from rising above the thermal shut-
down and causing the device to shut down. Power dis-
sipation is highest with higher battery voltages, higher
current limit, and under shorter dc loop conditions.
Additionally, higher ambient temperature will also
reduce thermal margin.
To support required power ringing voltages, this device
is meant to operate with a high-voltage primary battery
(–65 V to –75 V typically). Thus, power control is nor-
mally achieved by use of the battery switch and an aux-
iliary lower absolute voltage battery. Operating
temperature range, maximum current limit, maximum
battery voltage, minimum dc loop length and protection
resistors values, airflow, and number of PC board lay-
ers will influence the overall thermal performance. The
following example illustrates typical thermal design
considerations.
The thermal resistance of the 32-pin PLCC package is
typically 50.5
°
C/W, which is representative of the natu-
ral airflow as seen in a typical switch cabinet with a
two-layer board.
The L9215 will enter thermal shutdown at a minimum
temperature of 150
°
C. The thermal design should
ensure that the SLIC does not reach this temperature
under normal operating conditions.
For this example, assume a maximum ambient operat-
ing temperature of 85
°
C, a maximum current limit of
30 mA, a maximum battery of –70 V, and an auxiliary
battery of –21 V. Assume a (worst-case) minimum dc
loop of 20
of wire resistance, 30
protection resis-
tors, and 200
for the handset. Additionally, include
the effects of parameter tolerance.
1. T
TSD
– T
AMBIENT(max)
= allowed thermal rise.
150 °C – 85 °C = 65 °C.
2. Allowed thermal rise = package thermal
impedance
SLIC power dissipation.
65 °C = 50.5 °C/W
SLIC power dissipation
SLIC power dissipation (P
D
) = 1.29 W.
Thus, if the total power dissipated in the SLIC is less
than 1.29 W, it will not enter the thermal shutdown
state. Total SLIC power is calculated as:
Total P
D
= maximum battery
maximum current
limit + SLIC quiescent power.
For the L9215, the worst-case SLIC on-hook active
power is 76.4 mW. Thus,
Total off-hook power = (I
LOOP
)(current-limit
tolerance)*(V
BATAPPLIED
) + SLIC on-hook power
Total off-hook power = (0.030 A)(1.08) * (21) +
76.4 mW
Total off-hook power = 756.8 mW
The power dissipated in the SLIC is the total power dis-
sipation less the power that is dissipated in the loop.
SLIC P
D
= total power – loop power
Loop off-hook power = (I
LOOP
* 1.08)
2
(R
LOOP(dc)
min + 2R
HANDSET
)
Loop off-hook power = (0.030 A)(1.08)
2
(20
+
60
+ 200
)
Loop off-hook power = 293.9 mW
SLIC off-hook power = Total off-hook power – loop
off-hook power
SLIC off-hook power = 756.8 mW – 293.9 mW
SLIC off-hook power = 462.9 mW < 1.29 W
Thus, under the worst-case normal operating condi-
tions of this example, the thermal design, using the
auxiliary, is adequate to ensure the device is not driven
into thermal shutdown under worst-case operating con-
ditions.
dc Loop Current Limit
In the active modes, dc current limit is programmable
via an applied voltage source at the device’s V
PROG
control input. The voltage source may be an external
voltage source or derived via a resistor divider network
from the V
REF
SLIC output or an external voltage
source. A programmable external voltage source may
be used to provide software control of the loop current
limit. The loop current limit (I
LIM
) is related to the V
PROG
voltage at the onset of current limit by:
I
LIM
(mA) = 67 (mA/V) * V
PROG
(V)
Note that there is a 12.5 k
slope to the I/V character-
istic in the current-limit region; thus, once in current
limit, the actual loop current will increase slightly, as
loop length decreases.