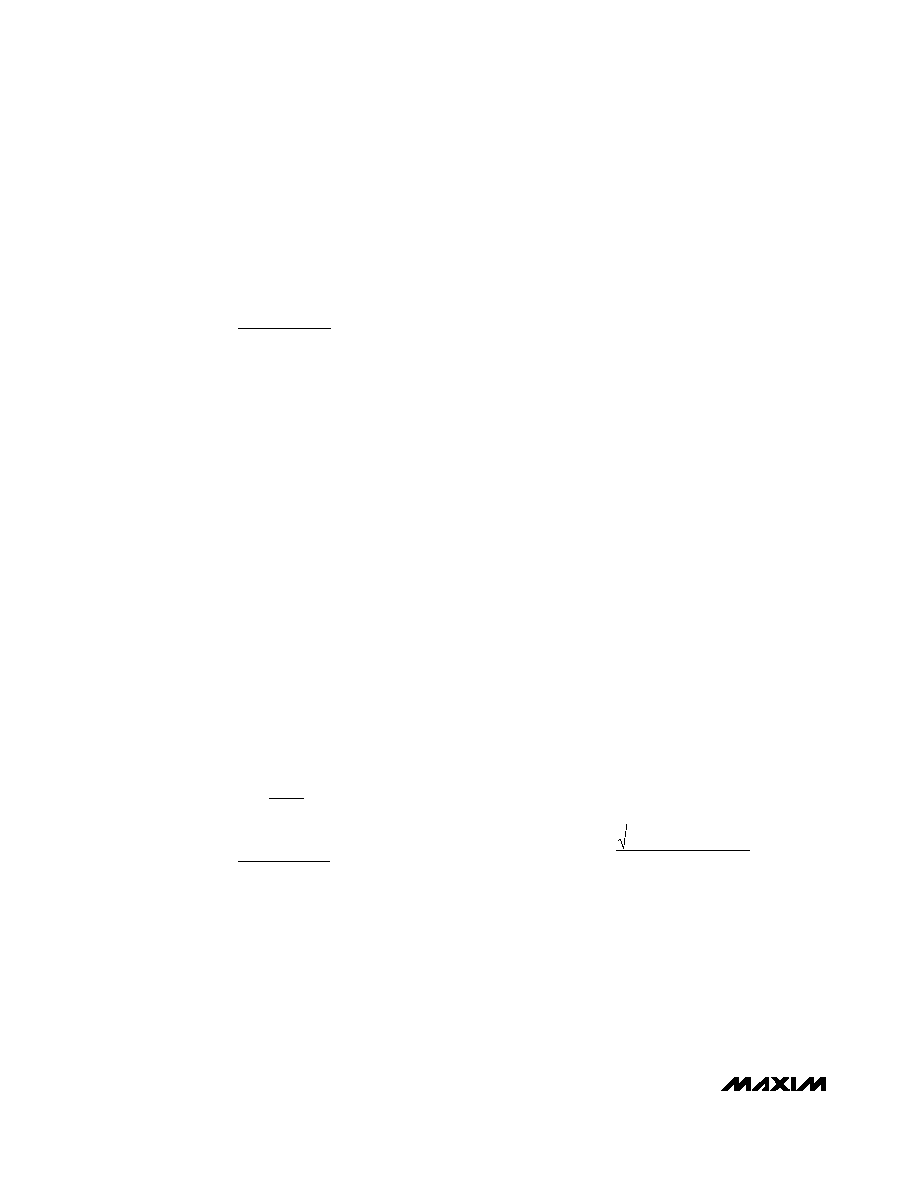
MAX1549
In applications without large and fast load transients, the
output capacitor’s size often depends on how much ESR
is needed to maintain an acceptable level of output volt-
age ripple. The output voltage ripple of a step-down con-
troller equals the total inductor ripple current multiplied by
the output capacitor’s ESR. Therefore, the maximum ESR
required to meet the ripple specifications is:
The actual capacitance value required relates to the
size needed to achieve low ESR, as well as to the
chemistry of the capacitor technology. Thus, the
capacitor is usually selected by ESR and voltage rating
rather than by capacitance value (this is true of tanta-
lums, OS-CONs, polymers, and other electrolytics).
When using low-capacity filter capacitors, such as
ceramic capacitors, size is usually determined by the
capacity needed to prevent VSAG and VSOAR from
causing problems during load transients. Generally,
once enough capacitance is added to meet the over-
shoot requirement, undershoot at the rising load edge
is no longer a problem (see the VSAG and VSOAR equa-
tions in the Transient Response section). However, low-
capacity filter capacitors typically have high ESR zeros
that can affect the overall stability (see the Output-
Capacitor Stability Considerations section).
Output-Capacitor Stability Considerations
The MAX1549 controllers rely on the output voltage ripple,
which can be defined as the inductor current ripple times
the output capacitor’s ESR, to generate the current-mode
control signal required for stable operation. Therefore, the
controller’s stability is determined by the value of the ESR
zero relative to the switching frequency. The boundary of
instability is given by the following equation:
where:
For a typical 300kHz application, the ESR zero frequency
must be well below 95kHz, preferably below 50kHz.
Tantalum and OS-CON capacitors in widespread use at
the time of publication have typical ESR zero frequencies
of 25kHz. In the design example used for inductor selec-
tion, the ESR needed to support 25mVP-P ripple is 25mV /
1.5A = 16.7m
. One 220F/4V Sanyo polymer (TPE)
capacitor provides 15m
(max) ESR. This results in a
zero at 48kHz, well within the bounds of stability.
Do not put high-value ceramic capacitors directly
across the feedback sense point without taking precau-
tions to ensure stability. Large ceramic capacitors can
have a high-ESR zero frequency and cause erratic,
unstable operation. However, it is easy to add enough
series resistance by placing the capacitors a couple
inches downstream from the feedback sense point,
which should be as close as possible to the inductor.
Unstable operation manifests itself in two related but
distinctly different ways: duty-cycle variation and fast-
feedback loop instability. Duty-cycle variation occurs
due to noise on the output or because the ESR is so
low that there is not enough voltage ramp in the output-
voltage signal. This “fools” the error comparator into
extending the on-time, forcing the next cycle to termi-
nate its on-time early. Duty-cycle variation is more
annoying than harmful, resulting in nothing worse than
increased output ripple. However, it can indicate the
possible presence of loop instability due to insufficient
ESR. Loop instability can result in oscillations at the out-
put after line or load steps. Such perturbations are usu-
ally damped, but can cause the output voltage to rise
above or fall below the tolerance limits.
The easiest method for checking stability is to apply a
very fast zero-to-max load transient and carefully
observe the output-voltage-ripple envelope for over-
shoot and ringing. It can help to simultaneously monitor
the inductor current with an AC current probe. Do not
allow more than one cycle of ringing after the initial
step-response under/overshoot.
Input Capacitor Selection
The input capacitor must meet the RMS ripple current
requirement (IRMS) imposed by the switching currents.
For a single step-down converter, the RMS input ripple
current is defined by the output load current (IOUT),
input voltage, and output voltage, with the worst-case
condition occurring at VIN = 2VOUT:
For a dual 180
° interleaved controller, the out-of-phase
operation reduces the RMS input ripple current, effec-
tively lowering the input capacitance requirements.
II
VV
V
RMS
OUT
IN
OUT
IN
=
()
-
f
RC
ESR
ESR OUT
=
1
2
π
f
ESR
OSC
≤
π
R
V
I
LIR
ESR
RIPPLE
LOAD MAX
()
≤
Dual, Interleaved, Fixed-Frequency Step-Down
Controller with a Dynamically Adjustable Output
28
______________________________________________________________________________________