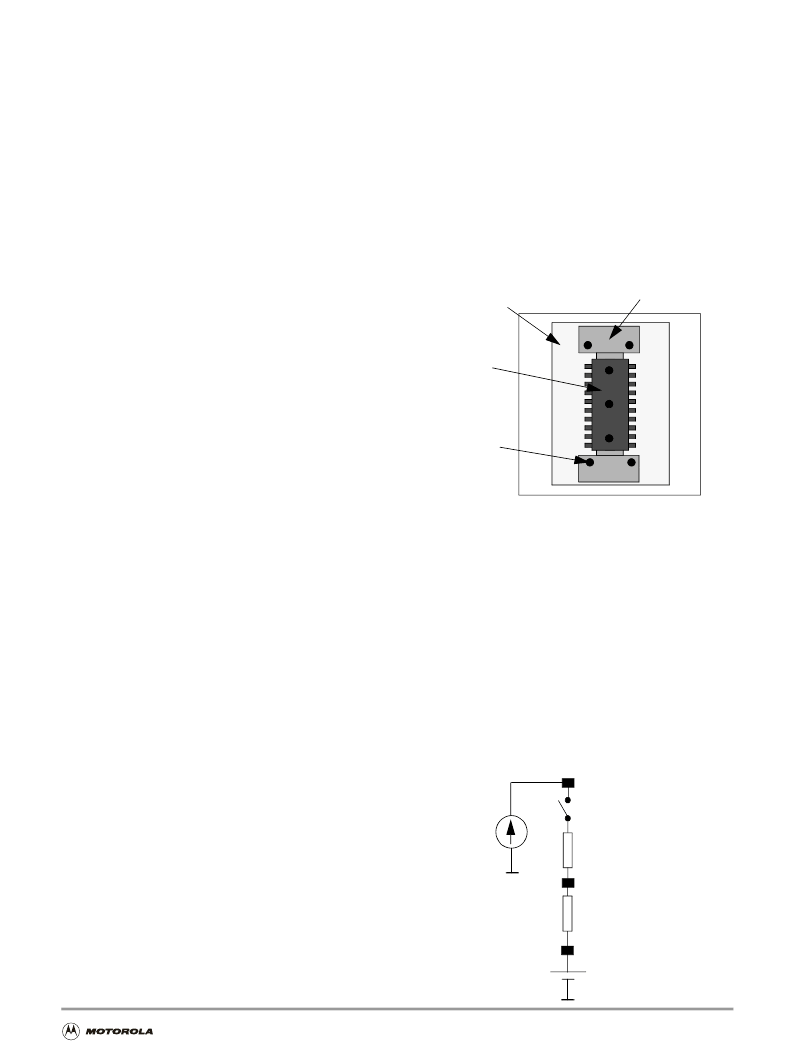
MC33486
DEVICE DESCRIPTION
Dual High Side Switch for H-Bridge Automotive Applications
7
Overtemperature Protection
The DHSB incorporates over-temperature protection. Over-
temperature detection occurs when an internal high side is in
the on state. When an over-temperature condition occurs,
both outputs are affected. Both outputs are turned off to
protect the DHSB from damage (Low sides ON). The
overtemperature protection circuitry incorporates hysteresis.
Overtemperature fault condition is reported on the status
output.
High side overcurrent protection
This device incorporates a current shutdown threshold of
35A typical. When this limit is reached due to an overload
condition or a short to ground, the faulty output is tri-stated. To
clear the fault the input (Inx) line needs to return low then on
the next high transition the output will be enabled.
This information is reported on the status output.
Low side block
The low side block has control circuitry for two external N-
Channel power MOSFET
’
s. The low side control circuitry is
PWM capable and protects the Low side MOSFETS in case of
overcurrent (short to Vbat). This information is reported on the
status output.
The low side Gate controls are clamped at14V maximum
to protect the gates of the Low Sides.
During normal operation, the outputs OUT1 and OUT2 are
driven by the high side. The low side Gate driver
’
s will only
turn on when the Drain voltage (same connection as OUT1 or
2) of the internal high sides is less than 2V, which prevent any
cross-conduction in the bridge.
Low Side Overcurrent Protection
Unlike the high side overcurrent circuitry, this overcurrent
protection does not measure the current , but measures the
effect of current on the low side through a condition : Vgs >
4.3V and Vds >2V. When this set of conditions occur for at
least 8us (blanking time), both outputs OUT1 and OUT2 are
tri-stated. The full bridge is tri-stated to prevent the motor for
running in case of short to Vbat.
As Vgs and Vds are measured in respect to the DHSB
’
s
ground pin, it is essential that the low side source are
connected to this same ground, in order to prevent false
overcurrent detection due to ground shifts.
Package
The high side block is assembled into a power surface
mount package. This package offers high thermal
performances, and high current capabilities. It offers 10 pins
on each package sides, and one additional connection which
is the package heat sink (called pin 21). The heat sink acts as
the device power Vbat connection.
Soldering Information
This device is packaged in a Surface Mount Power
package indended to be soldered directly on the Printed
Circuit Board.
This device was qualified according to JEDEC standards
JESD22-A113-B and J-STD-020A with the reflow conditions
applicable for packages with thickness above 2.5mm :
Convection 220
°
C +5/-0
°
C
VPR 215-219
°
C
IR / Convection 220
°
C +5/-0
°
C
The maximum peak temperature during the soldering process
should not exceed 220
°
C (+5
°
C/-0
°
C). The time at maximum
temperature should range from 10 to 40s max.
Thermal Management
The junction to case thermal resistance is 2
°
C/W
maximum. The junction to ambient thermal resistance is
dependant on the mounting technology, and if an additional
heat sink is used. One of the most commonly used mounting
technique consists of using the printed circuit board and the
copper lines as heat sink.
Figure 2 is an example of printed circuit board layout. It
has a total of 10cm
2
additional copper on two sides (2.5 cm
2
on the top side and 7.5 cm
2
on the down side).
Figure 3. .Printed Board Layout Example (not to scale)
With the above layout, thermal resistance junction to
ambient of 25
°
C/W can be achieved. This value being splitted
into :
. junction to case : Rthjc = 2
°
C/W
. case to ambient : Rthca = 23
°
C/W.
Lower value can be reached with the help of larger and
thicker copper metal, higher number of thermal via from top to
bottom side pcb and the use of additional thermal via from the
circuit board to the module case.
Thermal model
The junction to ambient thermal resistance of the circuit
mounted on a printed circuit board can be splitted into two
main parts: junction to case and case to ambient resistances.
A simplified steady state model is shown in figure 3 below.
Figure 4.
Simplified Thermal Model (Electrical
Equivalent)
Bottom side pcb
8 cm
2
Top side pcb
2 cm
2
HSOP20
external pcb (4x4 cm)
Thermal
via from
top to down
side pcb
Rthca
Rthjc
Junction Temp Node
(Volts represent Die
Surface Temperature)
Ambient Temp Node
Case Temp Node
Switch
Power (W)
(1.0A=1W of
Power Dissipation)
(1.0V=1
°
C Ambient Temperature)
(1.0
=1
°
C/W)
F
Freescale Semiconductor, Inc.
For More Information On This Product,
n
.