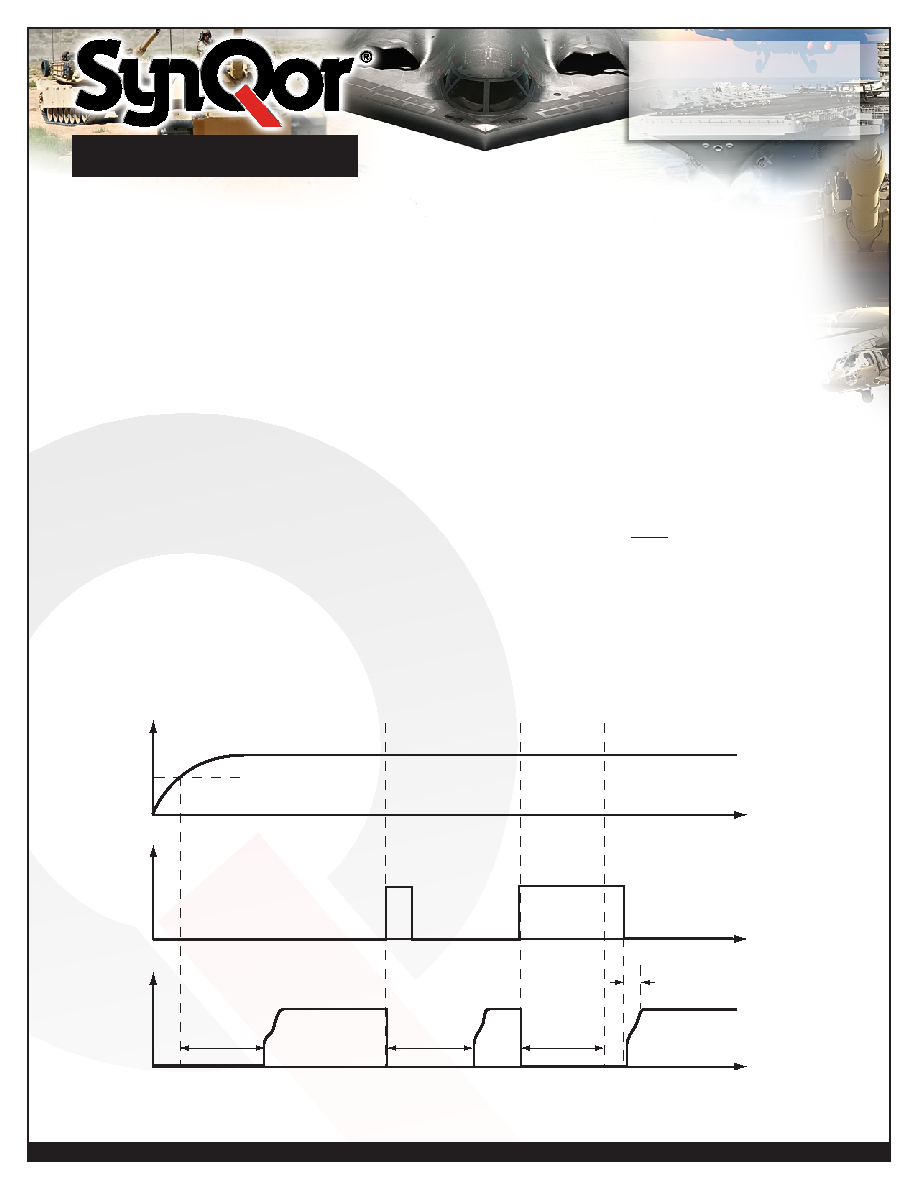
Technical Specification
Product # MCOTS-C-48-24-HP
Phone 1-888-567-9596
www.synqor.com
Doc.# 005-0005424 Rev. C
05/07/10
Page 11
MCOTS-C-48-24-HP
Output: 24V
Current: 10.5A
Figure F: Startup Inhibit Period (turn-on time not to scale)
Under-Voltage
Lockout Turn-
On Threshold
ON/OFF
(neg logic)
V
out
V
in
200ms
(typical start-up
inhibit period)
t
0
t
1
t
2
t
ON
OFF
10ms
(turn on time)
Startup Inhibit Period: The Startup Inhibit Period ensures
that the converter will remain off for approximately 200 ms
when it is shut down for any reason. When an output short is
present, this generates a 5 Hz “hiccup” mode, which prevents the
converter from overheating. In all, there are seven ways that the
converter can be shut down, initiating a Startup Inhibit Period:
Input Under-Voltage Lockout
Input Over-Voltage Lockout
Output Over-Voltage Protection
Over Temperature Shutdown
Current Limit
Short Circuit Protection
Turned off by the ON/OFF input
Figure F shows three turn-on scenarios, where a Startup Inhibit
Period is initiated at t
0, t1, and t2:
Before time t
0, when the input voltage is below the UVL threshold,
the unit is disabled by the Input Under-Voltage Lockout feature.
When the input voltage rises above the UVL threshold, the Input
Under-Voltage lockout is released, and a Startup Inhibit Period is
initiated. At the end of this delay, the ON/OFF pin is evaluated,
and since it is active, the unit turns on.
At time t
1, the unit is disabled by the ON/OFF pin, and it cannot
be enabled again until the Startup Inhibit Period has elapsed.
When the ON/OFF pin goes high after t
2,
the Startup Inhibit
Period has elapsed, and the output turns on within the typical
Turn-On Time.
Thermal Considerations: The maximum operating base-
plate temperature, T
B, is 100 C. Refer to the thermal derating
curve, Figure 5, to see the available output current at baseplate
temperatures below 100 C.
A power derating curve can be calculated for any heatsink that is
attached to the base-plate of the converter. It is only necessary
to determine the thermal resistance, RTH
BA, of the chosen heatsink
between the base-plate and the ambient air for a given airflow
rate. This information is usually available from the heatsink
vendor. The following formula can then be used to determine the
maximum power the converter can dissipate for a given thermal
condition:
P
max = TB - TA
diss
RTH
BA
This value of power dissipation can then be used in conjunction
with the data shown in Figure 3 to determine the maximum load
current (and power) that the converter can deliver in the given
thermal condition.