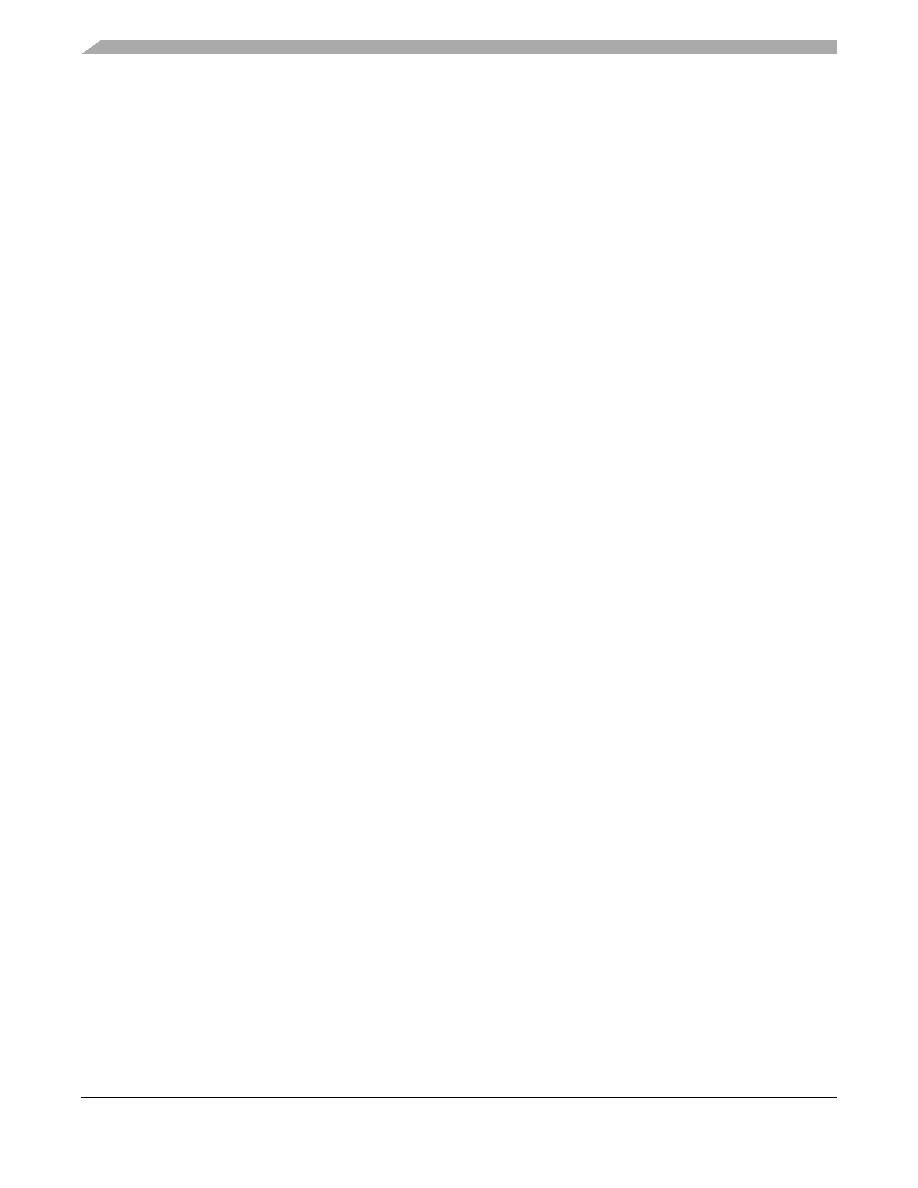
MPC8360E/MPC8358E PowerQUICC II Pro Processor Revision 2.x TBGA Silicon Hardware Specifications, Rev. 5
96
Freescale Semiconductor
System Clocking
22.3.1
Experimental Determination of the Junction Temperature with a
Heat Sink
When heat sink is used, the junction temperature is determined from a thermocouple inserted at the interface between the case
of the package and the interface material. A clearance slot or hole is normally required in the heat sink. Minimizing the size of
the clearance is important to minimize the change in thermal performance caused by removing part of the thermal interface to
the heat sink. Because of the experimental difficulties with this technique, many engineers measure the heat sink temperature
and then back calculate the case temperature using a separate measurement of the thermal resistance of the interface. From this
case temperature, the junction temperature is determined from the junction-to-case thermal resistance.
TJ = TC + (RθJC × PD)
where:
TJ = junction temperature (° C)
TC = case temperature of the package (° C)
RθJC = junction to case thermal resistance (° C/W)
PD = power dissipation (W)
23
System Design Information
This section provides electrical and thermal design recommendations for successful application of the MPC8360E/58E.
Additional information can be found in MPC8360E/MPC8358E PowerQUICC Design Checklist (AN3097).
23.1
System Clocking
The device includes two PLLs, as follows.
The platform PLL (AVDD1) generates the platform clock from the externally supplied CLKIN input. The frequency
ratio between the platform and CLKIN is selected using the platform PLL ratio configuration bits as described in
The e300 core PLL (AVDD2) generates the core clock as a slave to the platform clock. The frequency ratio between
the e300 core clock and the platform clock is selected using the e300 PLL ratio configuration bits as described in
23.2
PLL Power Supply Filtering
Each of the PLLs listed above is provided with power through independent power supply pins (AVDD1, AVDD2, respectively).
The AVDD level should always be equivalent to VDD, and preferably these voltages are derived directly from VDD through a
low frequency filter scheme such as the following.
There are a number of ways to reliably provide power to the PLLs, but the recommended solution is to provide five independent
filter circuits as illustrated in Figure 56, one to each of the five AVDD pins. By providing independent filters to each PLL, the opportunity to cause noise injection from one PLL to the other is reduced.
This circuit is intended to filter noise in the PLLs resonant frequency range from a 500 kHz to 10 MHz range. It should be built
with surface mount capacitors with minimum Effective Series Inductance (ESL). Consistent with the recommendations of Dr.
Howard Johnson in High Speed Digital Design: A Handbook of Black Magic (Prentice Hall, 1993), multiple small capacitors
of equal value are recommended over a single large value capacitor.
Each circuit should be placed as close as possible to the specific AVDD pin being supplied to minimize noise coupled from
nearby circuits. It should be possible to route directly from the capacitors to the AVDD pin, which is on the periphery of package,
without the inductance of vias.