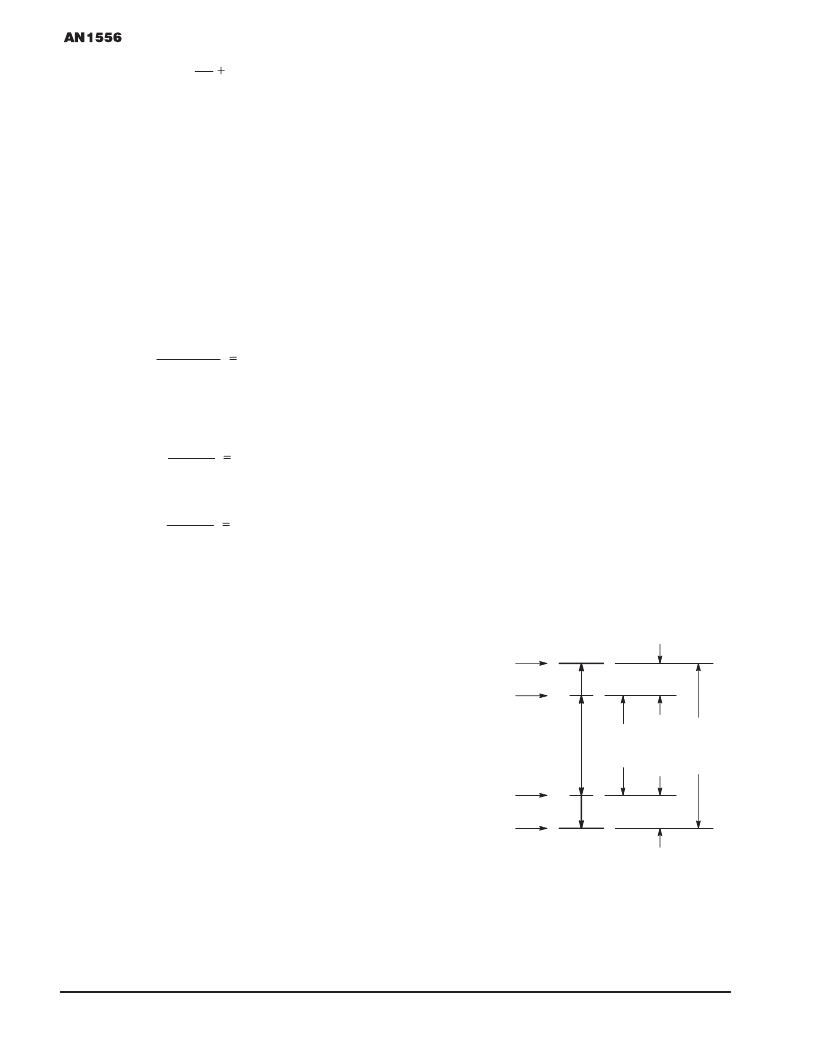
3–348
Motorola Sensor Device Data
For More Information On This Product,
Go to: www.freescale.com
Where the gain is
(
R4
differential output voltage is the quantity (S+ – S–), and the
positive dc voltage level shift, created by the voltage divider
comprised of RREF1 and RREF2, is VREF. In addition to using
the above resistor ratios to preserve the common mode
rejection, the effective resistance of the parallel combination
of RREF1 and RREF2 should be a low impedance to ground
relative to the resistance of R1.
R3
1
)
, the pressure sensor’s
RESOLUTION AND FACTORS THAT AFFECT IT
Performance of a pressure sensor system is directly related
to its resolution. Resolution is the smallest increment of
pressure that the system can resolve — e.g., a system that
measures pressure up to 10 kPa (full–scale) with a resolution
of 1% of full–scale can resolve pressure increments of
0.1 kPa. Similarly, the resolution (smallest increment of
voltage) of an 8–bit A/D converter with a 5 V window (a high
reference voltage of 5 V and a low reference voltage of 0 V) is
5 V
255 (8 bits)
19.6 mV
Many pressure sensor systems interface an A/D converter.
If the above system example requires 1% resolution when
interfaced to an A/D, the pressure sensor signal’s span must
be at least
19.6 mV
1%
1.96 V
If the system resolution required is 0.5%, the pressure
sensor signal’s span must be at least
19.6 mV
0.5%
3.92 V
From these examples, the greater the resolution required,
the greater the sensor’s amplified span must be to meet the
resolution requirement. Since a pressure sensor’s span
before amplification is only on the order of tens of millivolts, the
amplifier must be designed to provide the minimum span that
gives the desired resolution. If the amplifier has a fixed gain,
any device–to–device variation in the sensor’s unamplified
span will result in variation of the amplified span. If, for
example, the sensor’s span variation results in an amplified
span that is smaller than required, the resolution of the system
will not be as high as desired. Alternately, if the sensor’s span
variation results in an amplified span that is larger than
required, the resolution will be better than desired, BUT the
amplified span may also either saturate the amplifier near its
supply rails or extend outside the high and low reference
voltages of the A/D. Voltages above the high reference will be
digitally converted as 255 decimal (for 8–bit A/D), and voltages
below the low reference will be converted as 0. This creates
a non–linearity in the analog–to–digital conversion and in the
overall system transfer function.
As presented above, the variation of the sensor’s span
creates a dilemma: how does one design a fixed–gain
amplifier that gives the desired resolution, does not violate the
limits of the linear output ranges of the op–amps and A/D
converter, and also accommodates the complete distribution
of possible sensor spans The same question is presented to
the additional sources of variation: device–to–device variation
in the zero–pressure offset voltage and temperature effects on
both the sensor’s span and zero–pressure offset voltage. Also
any component tolerances for the voltage regulator and
resistors must be considered.
Designing the system when only one source of variation is
involved is not difficult; however, when all of these variations
are interacting, the solution becomes complicated. The rest of
this paper describes a design methodology that considers all
of the above variations and their interactions. Worst case limits
will be used in designing the fixed–value system.
RESOLUTION vs. HEADROOM
As stated previously, the amplified span of the sensor must
“fit” within the high and low references of an A/D to avoid any
nonlinearity errors. And the span must also be large enough
to provide the resolution required for the application. Any part
of the A/D’s “window” that is not used for the sensor’s dynamic
signal range is called headroom. Headroom may be thought
of as a cushion between the high and low reference voltages
and the sensor’s dynamic output range. This “cushion” is used
to allow the sensor’s dynamic range to move and/or vary within
the A/D’s window. A general description is shown in Figure 2.
The total amount of sensor output signal variation (due to
temperature effects, device–to–device variation, and interface
circuit component tolerances) cannot exceed the headroom
that is available for the requisite amount of system resolution.
A larger sensor span (more bits used for signal resolution)
means a smaller amount of headroom available to
accommodate sensor parameter and interface circuit
variations. This makes the tradeoff between resolution and
variation obvious. The more variation in the system, the more
headroom that is required to allow for the variation and,
consequently, less of the A/D window is available for the
sensor’s “true–signal” span. Less span results in poorer
resolution (less bits used for resolving sensor output signal).
A/D HIGH REFERENCE OR
HIGH SAT. LEVEL
OF AMPLIFIER
FULL–SCALE
OUTPUT VOLTAGE
ZERO PRESSURE
OFFSET VOLTAGE
A/D LOW REFERENCE OR
LOW SAT. LEVEL
OF AMPLIFIER
HEADROOM
HEADROOM
A/D’S OR
AMPLIFIER’S
DYNAMIC
RANGE
SENSOR’S
FULL–SCALE
VOLTAGE SPAN
Figure 2. Sensor’s Full–Scale Span vs. Headroom
F
Freescale Semiconductor, Inc.
n
.