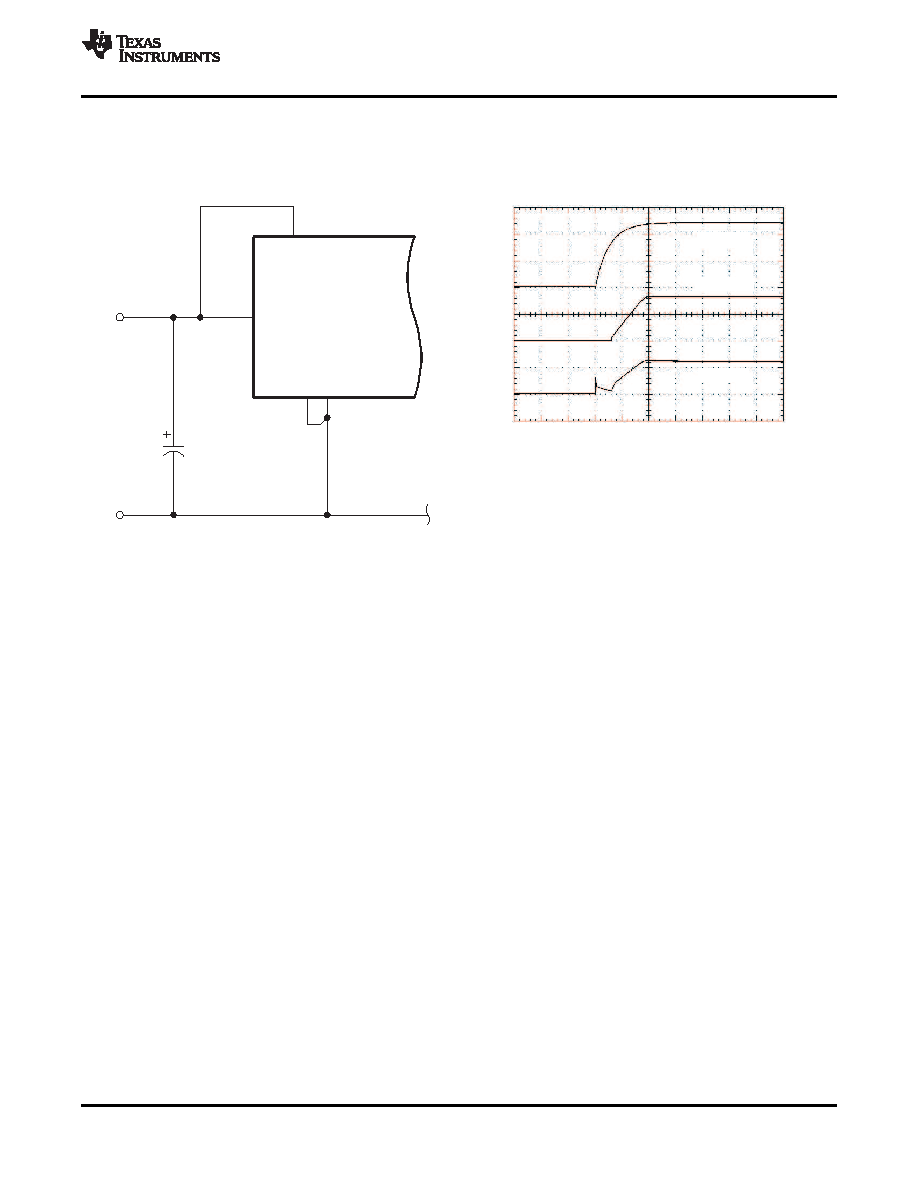
Soft-Start Power Up
t Time 10ms/div
VO (2V/div)
V (5V/div)
I
II (5 A/div)
14
Track
GND
2, 6
3,4
7,8
VI
CI
PTH08T210W
Remote Sense
www.ti.com ................................................................................................................................................... SLTS262I – OCTOBER 2005 – REVISED MARCH 2009
The Auto-Track feature allows the power-up of multiple PTH/PTV modules to be directly controlled from the
Track pin. However in a stand-alone configuration, or when the Auto-Track feature is not being used, the Track
pin should be directly connected to the input voltage, VI. (see Figure 20) Figure 20. Power-Up Application Circuit
Figure 21. Power-Up Waveform
When the Track pin is connected to the input voltage the Auto-Track function is permanently disengaged. This
allows the module to power up entirely under the control of its internal soft-start circuitry. When power up is
under soft-start control, the output voltage rises to the set-point at a quicker and more linear rate. From the
moment a valid input voltage is applied, the soft-start control introduces a short time delay (typically 8 ms–15 ms)
before allowing the output voltage to rise. The output then progressively rises to the module’s setpoint voltage.
Figure 21 shows the soft-start power-up characteristic of the PTH08T210W operating from a 12-V input bus and
configured for a 3.3-V output. The waveforms were measured with a 20-A constant current load and the
Auto-Track feature disabled. The initial rise in input current when the input voltage first starts to rise is the charge
current drawn by the input capacitors. Power-up is complete within 25 ms.
Products with this feature incorporate one or two remote sense pins. Remote sensing improves the load
regulation performance of the module by allowing it to compensate for any IR voltage drop between its output
and the load. An IR drop is caused by the high output current flowing through the small amount of pin and trace
resistance.
To use this feature simply connect the Sense pins to the corresponding output voltage node, close to the load
circuit. If a sense pin is left open-circuit, an internal low-value resistor (15-
or less) connected between the pin
and the output node, ensures the output remains in regulation.
With the sense pin connected, the difference between the voltage measured directly between the VO and GND
pins, and that measured at the Sense pins, is the amount of IR drop being compensated by the regulator. This
should be limited to a maximum of 0.3 V.
The remote sense feature is not designed to compensate for the forward drop of nonlinear or frequency
dependent components that may be placed in series with the converter output. Examples include OR-ing
diodes, filter inductors, ferrite beads, and fuses. When these components are enclosed by the remote sense
connection they are effectively placed inside the regulation control loop, which can adversely affect the
stability of the regulator.
Copyright 2005–2009, Texas Instruments Incorporated
21