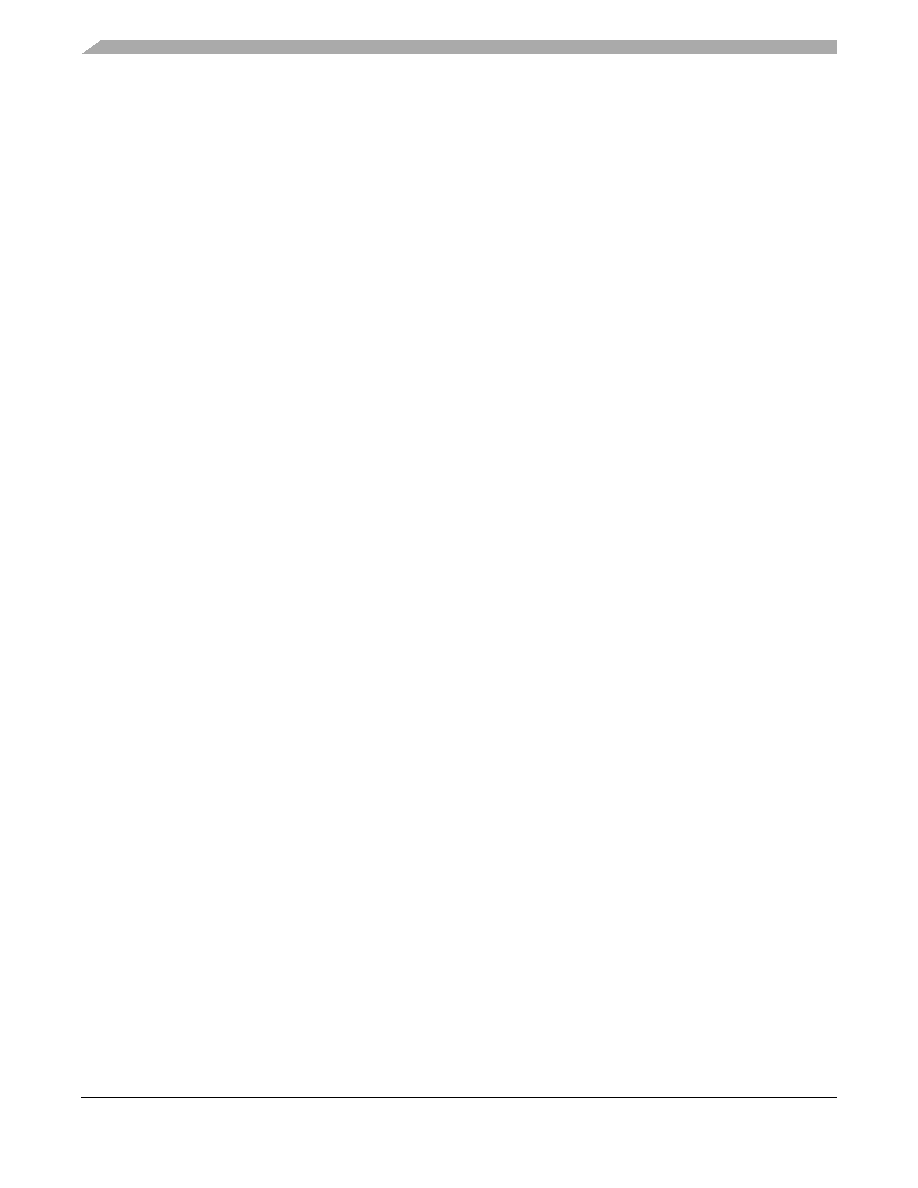
MPC5510 Microcontroller Family Data Sheet, Rev. 3
Electrical Characteristics
Freescale Semiconductor
22
the component is not a constant. It depends on the construction of the application board (number of planes), the effective size
of the board which cools the component, how well the component is thermally and electrically connected to the planes, and the
power being dissipated by adjacent components.
Connect all the ground and power balls to the respective planes with one via per ball. Using fewer vias to connect the package
to the planes reduces the thermal performance. Thinner planes also reduce the thermal performance. When the clearance
between through vias leave the planes virtually disconnected, the thermal performance is also greatly reduced.
As a general rule, the value obtained on a single layer board is appropriate for the tightly packed printed circuit board. The value
obtained on the board with the internal planes is usually appropriate if the application board has one oz (35 micron nominal
thickness) internal planes, the components are well separated, and the overall power dissipation on the board is less than 0.02
W/cm2.
The thermal performance of any component depends strongly on the power dissipation of surrounding components. In addition,
the ambient temperature varies widely within the application. For many natural convection and especially closed box
applications, the board temperature at the perimeter (edge) of the package is approximately the same as the local air temperature
near the device. Specifying the local ambient conditions explicitly as the board temperature provides a more precise description
of the local ambient conditions that determine the temperature of the device.
At a known board temperature, the junction temperature is estimated using the following equation:
TJ = TB + (RθJB × PD)
Eqn. 5
where:
TJ = junction temperature (
oC)
Eqn. 6
TB = board temperature at the package perimeter (
oC/W)
Eqn. 7
RθJB = junction to board thermal resistance (
oC/W) per JESD51-8
Eqn. 8
PD = power dissipation in the package (W)
Eqn. 9
When the heat loss from the package case to the air can be ignored, acceptable predictions of junction temperature can be made.
The application board should be similar to the thermal test condition, with the component soldered to a board with internal
planes.
Historically, the thermal resistance has frequently been expressed as the sum of a junction to case thermal resistance and a case
to ambient thermal resistance:
RθJA = RθJC + RθCA
Eqn. 10
where:
RθJA = junction to ambient thermal resistance (
oC/W)
Eqn. 11
RθJC = junction to case thermal resistance (
oC/W)
Eqn. 12
RθCA = case to ambient thermal resistance (
oC/W)
Eqn. 13
RθJC is device related and cannot be influenced by the user. The user controls the thermal environment to change the case to
ambient thermal resistance, RθCA. For instance, the user can change the air flow around the device, add a heat sink, change the
mounting arrangement on printed circuit board, or change the thermal dissipation on the printed circuit board surrounding the