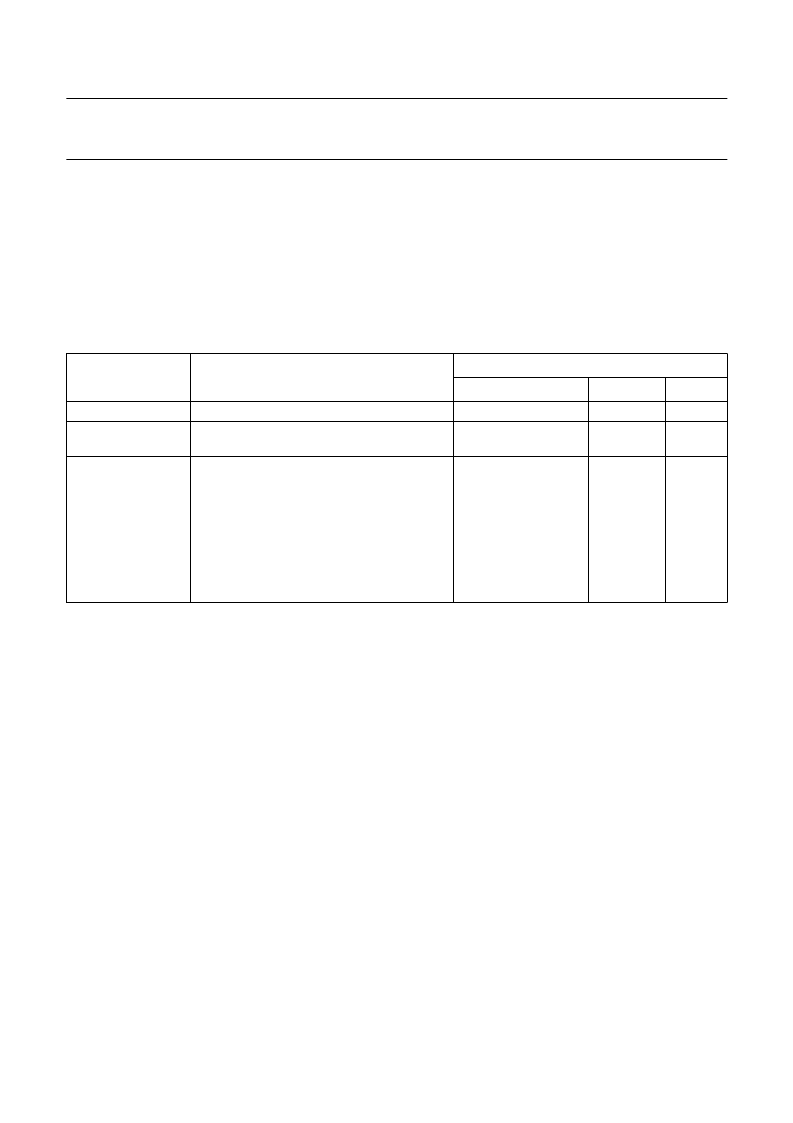
2003 Sep 09
20
Philips Semiconductors
Product specification
GreenChip
II SMPS control IC
TEA1506P; TEA1506AP;
TEA1506T; TEA1506AT
dispensing. The package can be soldered after the
adhesive is cured.
Typical dwell time of the leads in the wave ranges from
3 to 4 seconds at 250
°
C or 265
°
C, depending on solder
material applied, SnPb or Pb-free respectively.
A mildly-activated flux will eliminate the need for removal
of corrosive residues in most applications.
M
ANUAL SOLDERING
Fix the component by first soldering two
diagonally-opposite end leads. Use a low voltage (24 V or
less) soldering iron applied to the flat part of the lead.
Contact time must be limited to 10 seconds at up to
300
°
C. When using a dedicated tool, all other leads can
be soldered in one operation within 2 to 5 seconds
between 270 and 320
°
C.
Suitability of IC packages for wave, reflow and dipping soldering methods
Notes
1.
For more detailed information on the BGA packages refer to the“(LF)BGA Application Note” (AN01026); order a copy
from your Philips Semiconductors sales office.
All surface mount (SMD) packages are moisture sensitive. Depending upon the moisture content, the maximum
temperature (with respect to time) and body size of the package, there is a risk that internal or external package
cracks may occur due to vaporization of the moisture in them (the so called popcorn effect). For details, refer to the
Drypack information in the “Data Handbook IC26; Integrated Circuit Packages; Section: Packing Methods”
For SDIP packages, the longitudinal axis must be parallel to the transport direction of the printed-circuit board.
These transparent plastic packages are extremely sensitive to reflow soldering conditions and must on no account
be processed through more than one soldering cycle or subjected to infrared reflow soldering with peak temperature
exceeding 217
°
C
±
10
°
C measured in the atmosphere of the reflow oven. The package body peak temperature
must be kept as low as possible.
These packages are not suitable for wave soldering. On versions with the heatsink on the bottom side, the solder
cannot penetrate between the printed-circuit board and the heatsink. On versions with the heatsink on the top side,
the solder might be deposited on the heatsink surface.
If wave soldering is considered, then the package must be placed at a 45
°
angle to the solder wave direction.
The package footprint must incorporate solder thieves downstream and at the side corners.
Wave soldering is suitable for LQFP, QFP and TQFP packages with a pitch (e) larger than 0.8 mm; it is definitely not
suitable for packages with a pitch (e) equal to or smaller than 0.65 mm.
Wave soldering is suitable for SSOP, TSSOP, VSO and VSSOP packages with a pitch (e) equal to or larger than
0.65 mm; it is definitely not suitable for packages with a pitch (e) equal to or smaller than 0.5 mm.
Hot bar soldering or manual soldering is suitable for PMFP packages.
2.
3.
4.
5.
6.
7.
8.
9.
MOUNTING
PACKAGE
(1)
SOLDERING METHOD
WAVE
REFLOW
(2)
DIPPING
not suitable
Through-hole mount DBS, DIP, HDIP, SDIP, SIL
Through-hole-
surface mount
Surface mount
BGA, LBGA, LFBGA, SQFP, SSOP-T
(4)
,
TFBGA, VFBGA
DHVQFN, HBCC, HBGA, HLQFP, HSQFP,
HSOP, HTQFP, HTSSOP, HVQFN, HVSON,
SMS
PLCC
(6)
, SO, SOJ
LQFP, QFP, TQFP
SSOP, TSSOP, VSO, VSSOP
suitable
(3)
not suitable
suitable
PMFP
(9)
not suitable
suitable
not suitable
(5)
suitable
suitable
not recommended
(6)(7)
not recommended
(8)
suitable
suitable
suitable