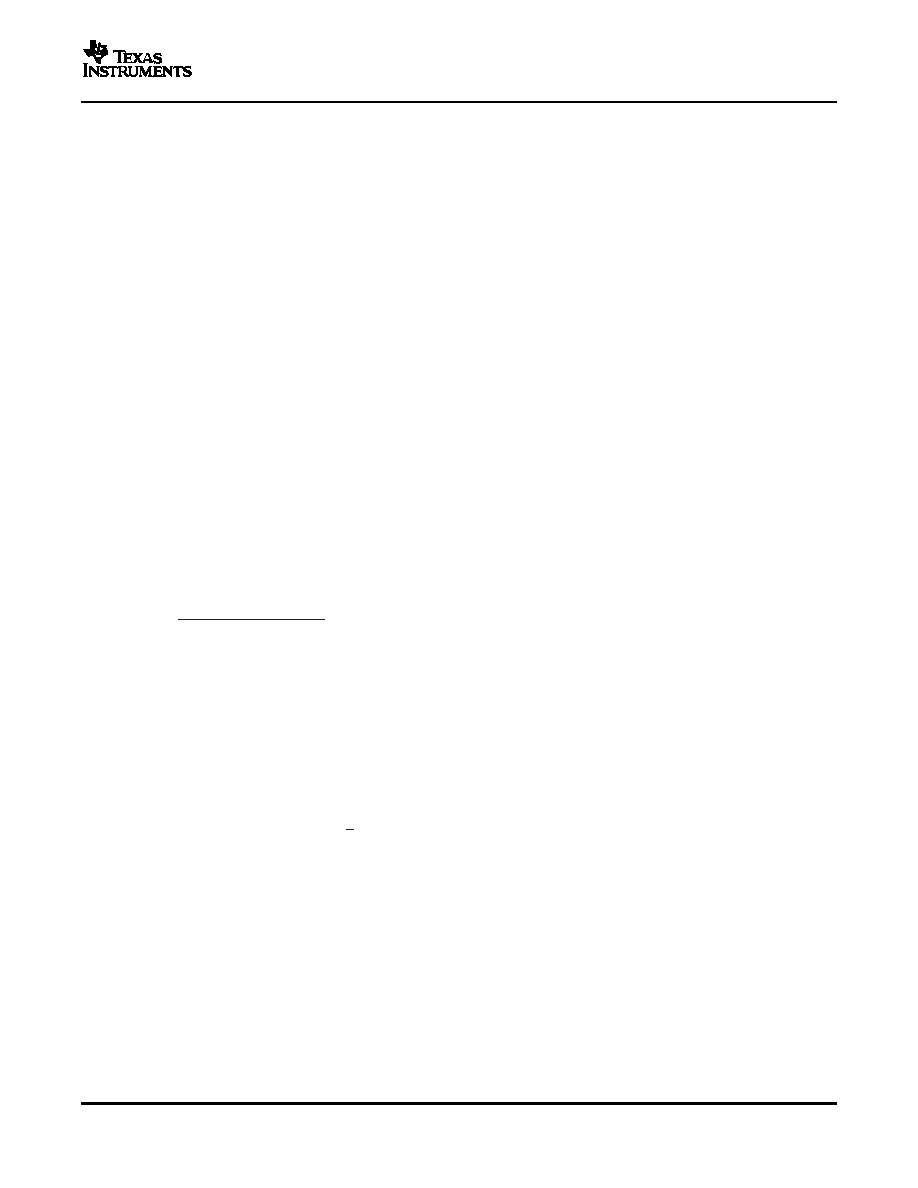
www.ti.com
Interaction Between Soft-Start and Tracking Startup
Overcurrent Protection
R
ILIM +
V
ILIM
gm
CSA
R
LDC
I
OC
W
(29)
t
OC + * RILIM
C
ILIM
ln 1
*
1
n
(s)
(30)
SLUS726 – SEPTEMBER 2006
APPLICATION INFORMATION (continued)
Since the TPS40101 provides two means of controlling the startup (closed loop soft-start and tracking) care
must be taken to ensure that the two methods do not interfere with each other. The two methods should not be
allowed to try and control the output at the same time. If tracking is to be used, the reference input to the
tracking amplifier (TRKIN) should be held low until soft-start completes, or the voltage at the SS pin is at least
above 1.04 V. This ensures that the soft-start circuit is not trying to control the startup at the same time as
tracking circuit. If it is desired to have soft-start control the startup, then there are two options:
Disconnect the tracking amplifier output from the FB node (this is the recommended solution. The tracking
amplifier can then be used for other system purposes if desired)
Maintain the tracking amplifier output connection to the FB circuit - the reference to the tracking amplifier
should be tied to VDD pin in this case. This places the tracking amplifier output (TRKOUT) in a low state
continuously and therefore removes any influence the tracking circuit has on the converter startup.
Additionally, when tracking is allowed to control the startup, soft-start should not be set to an arbitrarily short
time. This causes the output voltage to bump up when power is applied to the converter as soft-start ramps up
quickly and the tracking loop (which is necessarily low bandwidth) cannot respond fast enough to control the
output to zero voltage. In other words, the soft start ramp rate must be within the capability of the tracking loop
to override.
Overcurrent characteristics are determined by connecting a parallel R-C network from the ILIM pin to GND. The
ILIM pin sources a current that is proportional to the current sense amplifier transconductance and the voltage
between ISNS and VO. This current produces a voltage on the R-C network at ILIM. If the voltage at the ILIM
pin reaches 1.48 V, an overcurrent condition is declared and the outputs stop switching for a period of time. This
time period is determined by the time is takes to discharge the soft-start capacitor with a controlled current sink.
To set the overcurrent level:
where
V
ILIM is the overcurrent comparator threshold (1.48 V typically)
I
OC is the overcurrent level to be set
gm
CSA is the transconductance of the current sensing amplifier
R
LDC is the equivalent series resistance of the inductor (or the sense resistor value)
R
ILIM is the value of the resistor from ILIM to GND
The response time of the overcurrent circuit is determined by the R-C time constant at the ILIM pin and the level
of the overcurrent. The response time is given by:
where
t
OC is the response time before declaring an overcurrent
R
ILIM () and CILIM (F) are the components connected to the ILIM pin
n is the multiplier of the overcurrent. If the overcurrent is 2 times the programmed level, then n is 2.
By suitable manipulation of the time constant at ILIM, the overcurrent response can be tailored to ride out short
term transients and still provide protection for overloads and short circuits. The gm of the current sense amplifier
has a temperature coefficient of approximately -2000 ppm/
°C. This is to help offset the temperature coefficient of
resistance of the copper in the inductor, about +4000 ppm/
°C. The net is a +2000 ppm/°C temperature
coefficient. So, for a 100
°C increase in temperature, the overcurrent threshold decreases by 20%, assuming
good thermal coupling between the controller and the inductor. Temperature compensation can be done as
described earlier if desired.
When an overcurrent condition is declared, the controller stops switching and turns off both the high-side
25