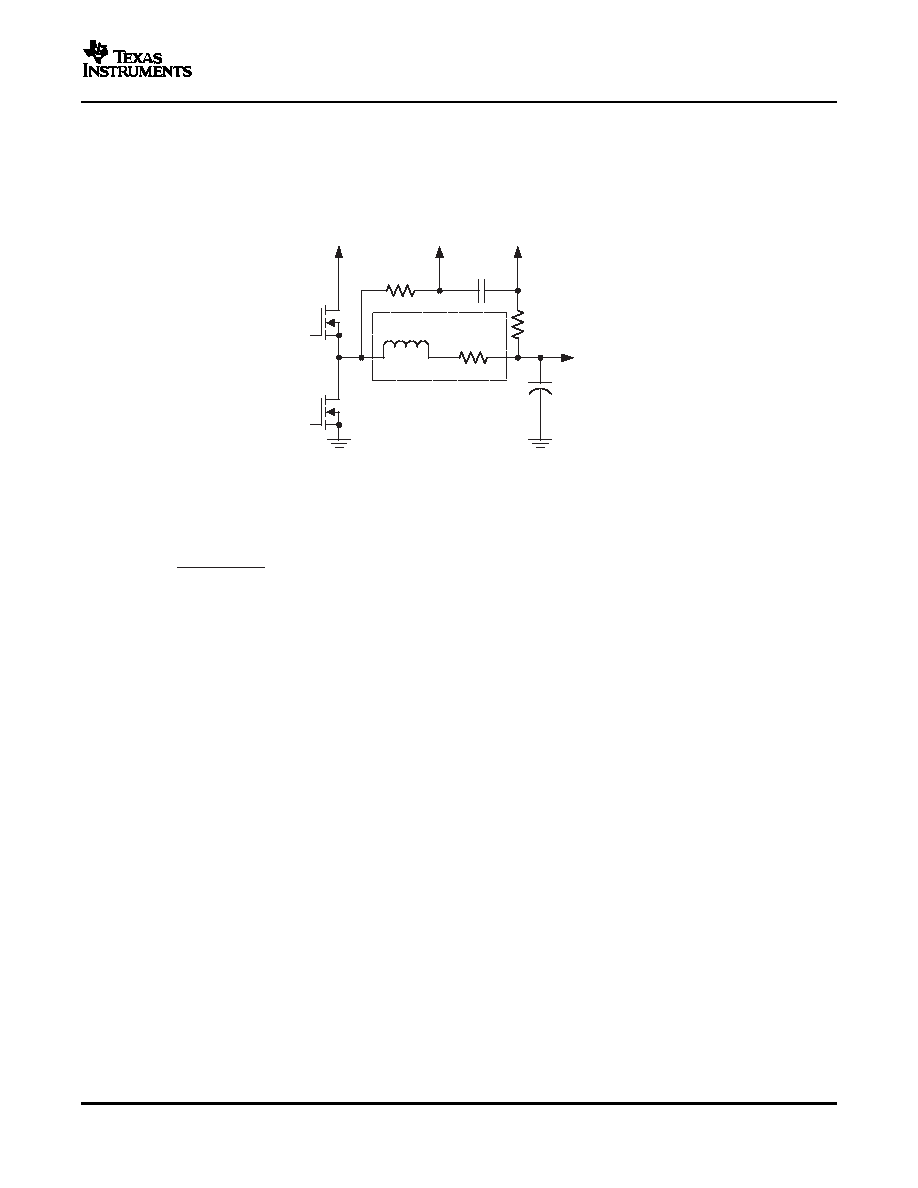
www.ti.com
Calculating the Current Sense Filter Network
L
To ISNS pin
UDG04150
To VO pin
VO
CO
RLDC
CFLT
VIN
RFLT
100
R
FLT +
L
R
LDC
C
FLT
* 100 (W)
(6)
Compensation for Inductor Resistance Change Over Temperature
SLUS726 – SEPTEMBER 2006
APPLICATION INFORMATION (continued)
The TPS40101 gets current feedback information by sensing the voltage across the inductor resistance, RLDC. In
order to do this, a filter must be constructed that allows the sensed voltage to be representative of the actual
current in the inductor. This filter is a series R-C network connected across the inductor as shown in
Figure 29.Figure 29. Current Sensing Filter Circuit
If the RFLT-CFLT time constant is matched to the L/RLDC time constant, the voltage across CFLT is equal to the
voltage across RLDC. It is recommended to keep RFLT 10 k or less. CFLT can be arbitrarily chosen to meet this
condition (100 nF is suggested). RFLT can then be calculated.
where
R
FLT is the current sense filter resistance ()
C
FLT is the current sense filter capacitance (F)
L is the output inductance (H)
R
LDC is the DC resistance of the output inductor ()
When laying out the board, better performance can be accomplished by locating CFLT as close as possible to the
VO and ISNS pins. The closer the two resistors can be brought to the device the better as this reduces the
length of high impedance runs that are susceptible to noise pickup. The 100-
resistor from V
OUT to the VO pin
of the device is to limit current in the event that the output voltage dips below ground when a short is applied to
the output of the converter.
The resistance in the inductor that is sensed is the resistance of the copper winding. This value changes over
temperature and has approximately a 4000 ppm/°C temperature coefficient. The gain of current sense amplifier
in the TPS40101 has a built in temperature coefficient of approximately -2000 ppm/°C. If the circuit is physically
arranged so that there is good thermal coupling between the inductor and the device, the thermal shifts tend to
offset. If the thermal coupling is perfect, the net temperature coefficient is 2000 ppm/°C. If the coupling is not
perfect, the net temperature coefficient lies between 2000 ppm/°C and 4000 ppm/°C. For most applications this
is sufficient. If desired, the temperature drifts can be compensated for. The following compensation scheme
assumes that the temperature rise at the device is directly proportional to the temperature rise at the inductor. If
this is not the case, compensation accuracy suffers. Also, there is generally a time lag in the temperature rise at
the device vs. at the inductor that could introduce transient errors beyond those predicted by the compensation.
Also, the 100-
resistor in
Figure 29 is not shown. However, it is required if the output voltage can dip below
ground during fault conditions. The calculations are not afffected, other than increasing the effective value of RF1
by 100-
.
17